Glass vs. Metal CO2 Laser Tubes: Which is Better?

Choosing between glass and metal CO2 laser tubes involves understanding their differences in cost, durability, performance, and maintenance. Glass tubes are cheaper but fragile; metal tubes are more durable and efficient. This guide explores the pros and cons of each type to assist in making an informed decision based on specific needs and budget considerations. Whether for light tasks or heavy industrial use, knowing the right tube can enhance operational capabilities while balancing upfront costs with long-term savings.
What Are the Risks and Benefits of Sourcing Chinese CO2 Laser Cutters on Alibaba Compared to Direct Manufacturer Negotiations?
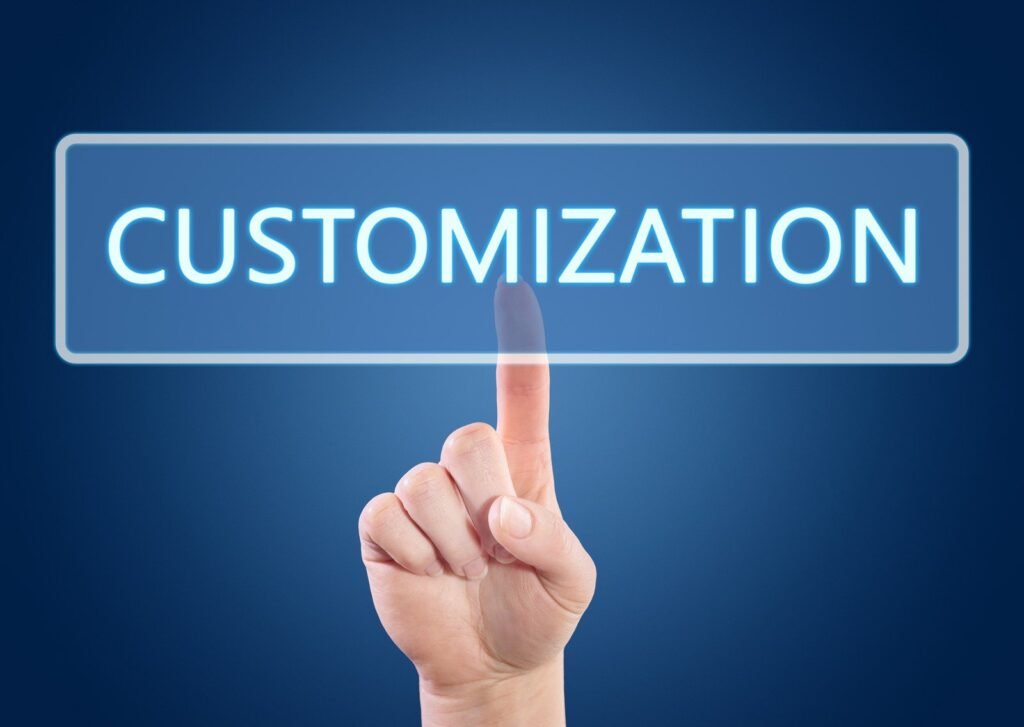
When sourcing CO2 laser cutters, businesses face a choice between using platforms like Alibaba or negotiating directly with manufacturers. Alibaba offers a wide selection, buyer protection, and ease of comparison but may involve risks like low-quality suppliers and hidden costs. In contrast, direct negotiations allow for better control over product specifications, stronger relationships, and potential cost savings but come with challenges such as supplier vetting difficulties and logistical complexities. Understanding these factors helps businesses decide which approach aligns best with their needs.
How Can You Ensure Quality and Reliability When Buying Chinese CO2 Laser Cutters?
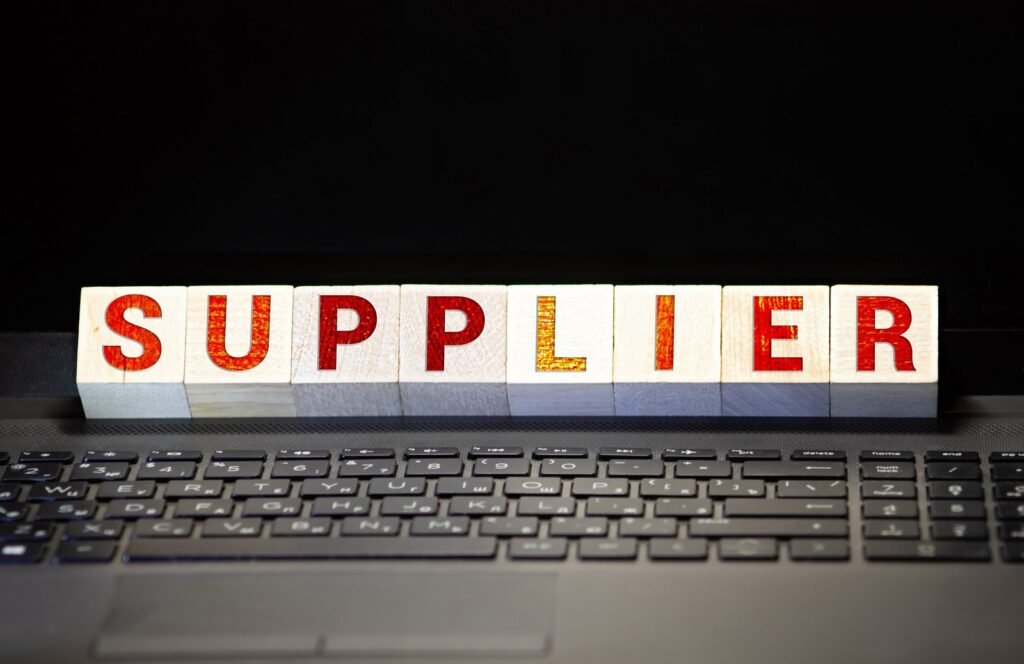
When buying Chinese CO2 laser cutters, ensuring quality and reliability is crucial for business success. Key steps include verifying supplier credentials, evaluating product specifications, requesting samples for testing, and confirming robust after-sales support. Focus on suppliers with industry certifications like ISO 9001 and CE to guarantee adherence to quality standards. Assess financial health and operational transparency to avoid potential pitfalls. Customer feedback is invaluable; positive reviews indicate reliable service and product quality. Additionally, understanding the importance of detailed product specifications can enhance performance outcomes. Sample testing mitigates risks by validating product claims before purchase. Finally, strong after-sales support ensures ongoing satisfaction through technical assistance, warranty services, and spare parts availability—essential for maintaining equipment efficiency over time.
What Challenges Do Buyers Face When Importing Chinese CO2 Laser Cutters and How Can They Overcome Them?
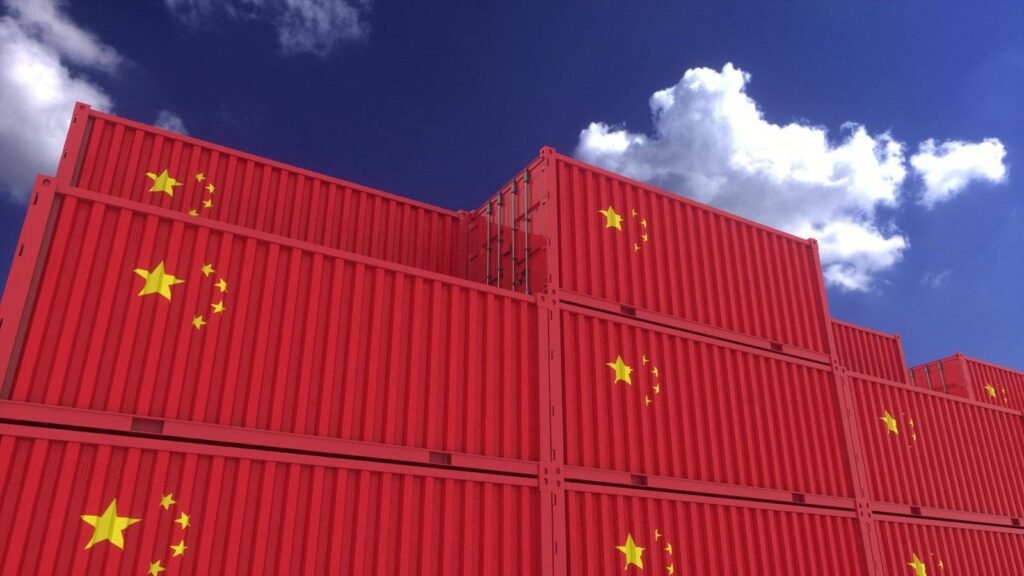
Importing CO2 laser cutters from China can be rewarding but fraught with challenges such as quality variability, communication issues, and shipping delays. To navigate these obstacles effectively, buyers should conduct thorough supplier evaluations, request product samples to ensure quality, and implement robust quality control measures. Clear communication is vital; utilizing professional translators and documenting all agreements helps prevent misunderstandings. Additionally, partnering with experienced freight forwarders can streamline shipping processes while understanding local customs regulations minimizes delays. After-sales support is crucial too—establishing clear warranty terms and maintaining spare parts availability ensures customer satisfaction. By adopting these strategies, buyers can enhance their importing experience and secure high-quality products.
How Can You Select the Right Gas for Plasma CNC Cutting Based on Material Type?

Choosing the appropriate gas for plasma CNC cutting is crucial to achieving optimal results. Compressed air offers versatility, while nitrogen provides clean cuts on stainless steel and aluminum. Oxygen allows fast cuts on carbon steel but may oxidize edges, whereas argon-hydrogen mixtures excel in cutting thick stainless steel and aluminum with minimal dross. Consider factors like cost, desired cut quality, and material thickness when selecting a gas. Understanding these elements can enhance your cutting efficiency and product quality while ensuring safety during operations.
What Factors Should You Consider When Choosing the Best Plasma Cutter?
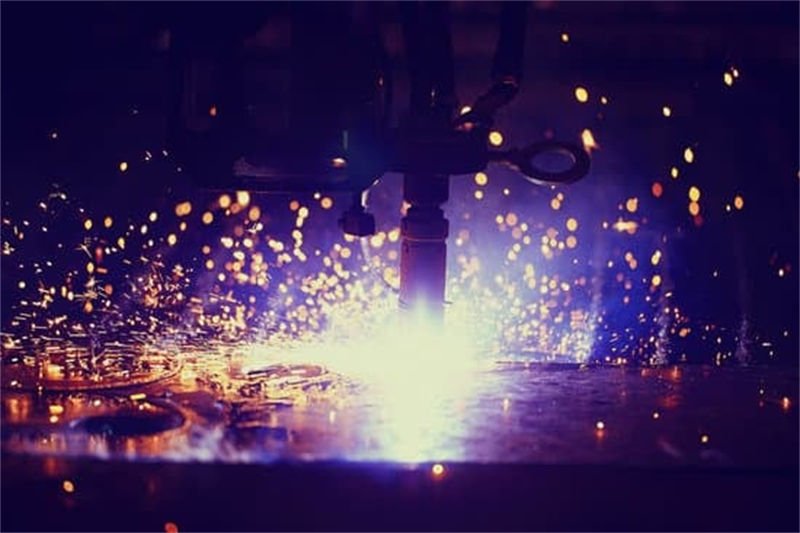
Selecting the right plasma cutter can be overwhelming due to the variety of models and features available. Key factors to consider include the type and thickness of materials you’ll be cutting, as well as the amperage capacity necessary for efficient performance. Understanding power sources—whether 120V or 240V—and opting for dual-voltage machines can enhance versatility in different work environments. Advanced features such as pilot arc technology are crucial for handling challenging surfaces without pre-cleaning. Additionally, evaluating portability and CNC compatibility is essential for maximizing productivity. Balancing these considerations with your budget ensures you find a plasma cutter that meets your needs effectively.
What Are the Key Factors to Consider When Choosing a Plasma Cutter for Industrial Use?

Selecting the right plasma cutter for industrial applications requires careful consideration of several key factors. These include cutting capacity, which determines how thick materials can be efficiently cut; duty cycle, which indicates how long the machine can operate before needing to cool down; and power requirements, ensuring compatibility with industrial power supplies. Additionally, advanced features such as CNC compatibility enhance precision and automation in cutting processes. Understanding these elements will help you choose a plasma cutter that meets your specific needs while maximizing productivity and minimizing downtime in demanding environments.
What Are the Best Tools for Cutting Carbon Steel?
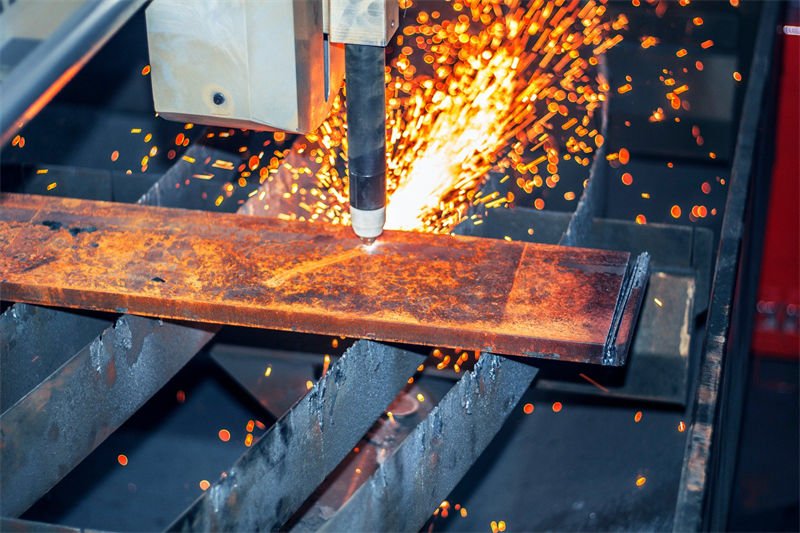
Selecting the best tool for cutting carbon steel can be challenging due to various options available. Plasma cutters are ideal for thick materials (over 5-6mm), providing speed and efficiency, while laser cutters excel in precision for thinner sheets (up to 10mm). CNC machines like flame and band saws serve specific needs based on material thickness. Understanding project requirements—such as desired precision, production scale, and budget constraints—is crucial in making an informed decision. This guide explores the strengths of each cutting method to help you choose the right tool for your carbon steel projects.
Why Is the Mazak Fiber Laser Cutter So Expensive?

Mazak fiber laser cutters command high prices because they incorporate cutting-edge technology, exceptional design quality, and unmatched performance. These machines enhance workshop productivity with smart features and robust components. Investing in a Mazak cutter not only boosts production but also attracts clients seeking high-quality outputs. The INTEGREX series exemplifies multi-tasking capabilities that streamline operations, while user-friendly CNC controls simplify complex tasks. Additionally, adaptive automation solutions optimize workflows further. Ultimately, the initial cost is offset by long-term benefits such as reduced setup times and increased customer satisfaction, making Mazak a leader in modern manufacturing.
Who is the Leading Manufacturer of Laser Fiber Cutting Machines?
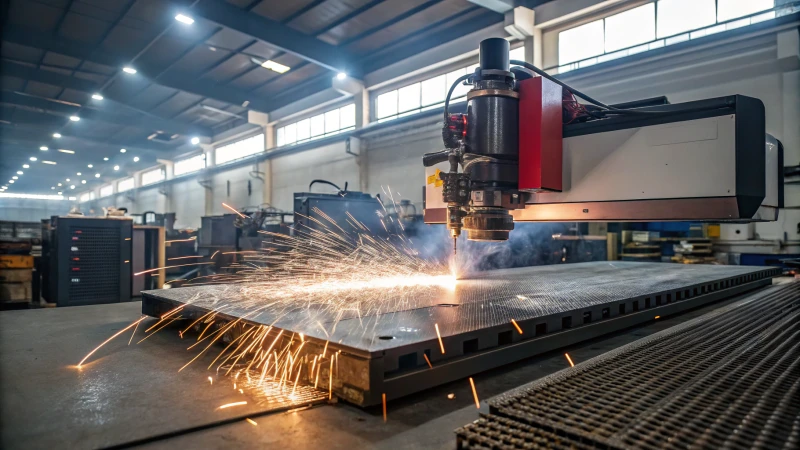
This article explores the top manufacturers of laser fiber cutting machines: Germany’s Trumpf, known for precision; Switzerland’s Bystronic with innovative designs; China’s Hans Laser offering cost-effective solutions; and Japan’s Amada renowned for reliability. Each brand provides distinct benefits tailored to different industrial requirements. Understanding these differences is crucial when selecting a machine that fits specific operational needs, budget constraints, and material types. The piece emphasizes the importance of evaluating technological advancements, after-sales support, and overall performance to make an informed decision in this competitive market.
What Should You Consider When Sourcing Chinese CO2 Laser Cutting Machines for Large-Scale Production?

Sourcing Chinese CO2 laser cutting machines for large-scale production requires careful consideration of several factors. Key aspects include machine specifications like power output and material compatibility, build quality, operational costs, and robust supplier support. Understanding the total cost of ownership (TCO) is crucial; it encompasses not just the initial purchase price but also ongoing operating expenses and maintenance costs. Reliable suppliers provide essential after-sales support that enhances operational efficiency and minimizes downtime. By evaluating these elements thoroughly, businesses can make informed decisions that align with their production goals while ensuring a reliable investment in machinery.
What Types of Parts Can a CNC Lathe Efficiently Process?
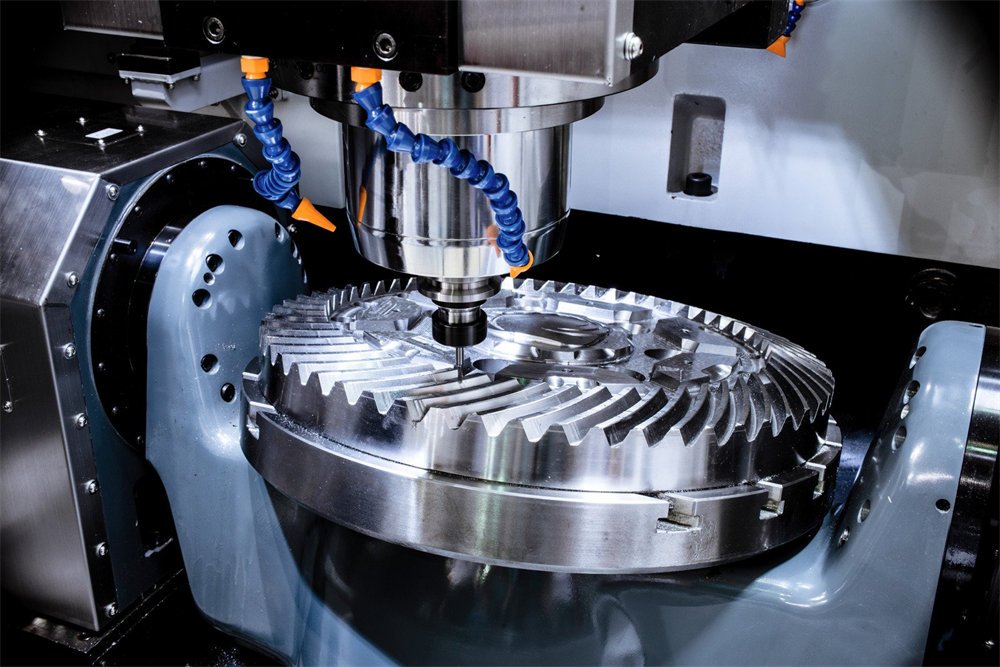
CNC lathes are essential in modern manufacturing for processing a wide range of cylindrical and axially symmetrical parts. They excel at crafting shafts, spindles, flanges, gears, bushings, screws, and nuts with remarkable precision and surface quality. The automation capabilities of CNC lathes enhance efficiency by reducing errors and material waste while maintaining consistent quality across production runs. Their adaptability allows for machining complex geometries from diverse materials like carbon steel and stainless steel. With advanced programming and real-time monitoring systems, CNC lathes ensure tight tolerances and exceptional surface finishes crucial for high-performance applications in industries such as automotive and aerospace.