How Can You Set Up Handheld Laser Welders for Optimal Material Compatibility?
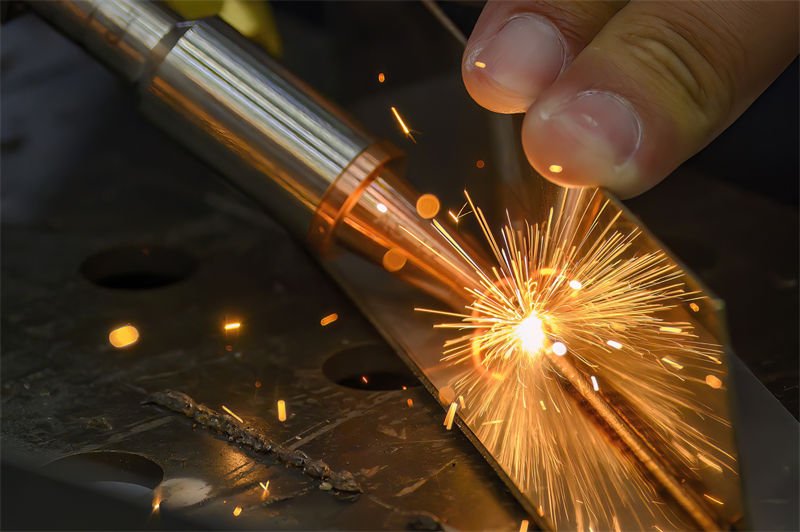
Setting up handheld laser welders requires careful adjustment of key parameters such as laser power, focus, welding speed, and shielding gas. Understanding material properties like thermal conductivity and reflectivity is crucial for achieving optimal results. Each setting plays a vital role in ensuring precision and quality in welding processes. Testing sample welds helps fine-tune these settings to prevent defects like burn-through or incomplete penetration. Additionally, selecting the right shielding gas is essential to protect the weld from oxidation and enhance its quality. By mastering these techniques, you can transform your welding projects into seamless successes.
Why Is Regular Calibration Essential for Handheld Laser Welding Machines?
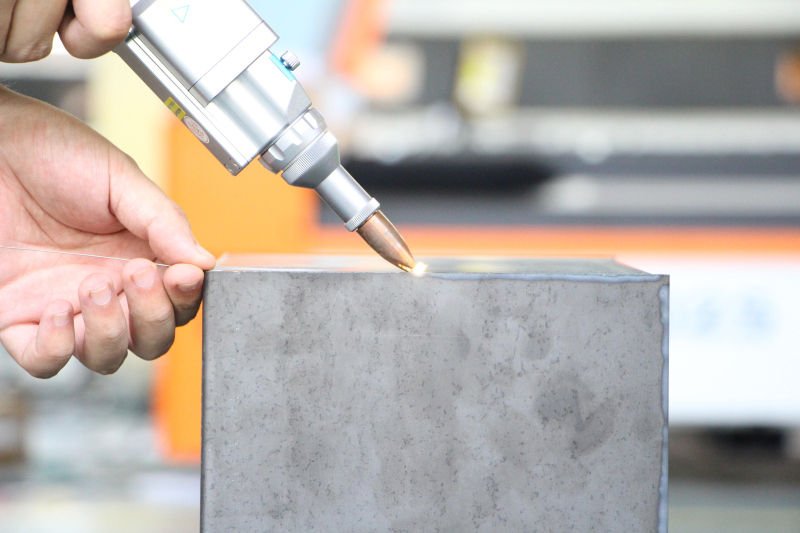
Regular calibration is essential for handheld laser welding machines to maintain optimal performance. It ensures the laser’s power, focus, and alignment are precise, preventing defects and reducing wear on components. This practice not only boosts efficiency but also extends the lifespan of the equipment. Industries that rely on precision benefit significantly from regular checks as they enhance measurement accuracy, ensure compliance with industry standards, and improve overall workflow efficiency. By implementing a routine calibration schedule and utilizing appropriate tools like power meters and beam profilers, businesses can avoid costly repairs and maintain high-quality standards in their operations.
Which Handheld Laser Welding Machines Are Best for Small Workshops?

Choosing the right handheld laser welding machine is essential for small workshops. This guide highlights top models such as the Ironsten XING Laser 1500W and ZAC 1500Watt MAX Fiber Laser Welder, which offer multifunctionality including welding, cutting, and cleaning. These machines are designed to fit compact spaces while providing powerful performance suitable for various materials like carbon steel and titanium. Key considerations include power output (1000W to 1500W), portability, material compatibility, and budget constraints. Affordable options like STYLECNC’s 1000W model cater to beginners without sacrificing quality. Understanding these factors will help you select a machine that enhances productivity in your workshop.
Why Are Fiber Laser Sources Enhancing the Reliability of Handheld Welders?
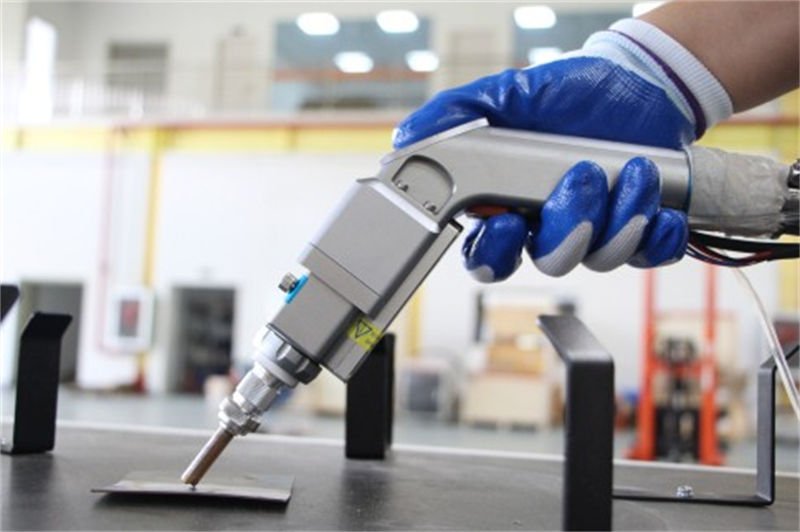
Fiber lasers are revolutionizing the welding industry by providing exceptional reliability in handheld welders. With a lifespan exceeding 100,000 hours, these solid-state lasers require minimal maintenance and deliver high energy efficiency. Their robust design ensures consistent performance even in harsh environments, while their superior beam quality allows for precise welding across various materials. This adaptability makes fiber lasers an invaluable tool for industries requiring precision and durability. Additionally, their compact design enhances operator comfort during extended use. Explore how fiber laser technology is transforming welding practices and boosting productivity across sectors.
What Are the Essential Safety Precautions for Using a Plasma Cutter?

Using a plasma cutter can be exciting but comes with risks. Essential safety precautions include wearing appropriate personal protective equipment (PPE), ensuring good ventilation to remove harmful fumes, and maintaining equipment regularly. Proper air flow is crucial for worker safety, while flame-resistant clothing, gloves, goggles, and ear protection are necessary to prevent injuries. Regular inspections of cables and tools help avoid electric shocks. A tidy workspace free from combustibles further enhances safety. Training staff on emergency protocols ensures preparedness in case of accidents. By following these guidelines, you can enjoy the benefits of plasma cutting while minimizing risks.
Which Industries Benefit Most from Plasma Cutting?
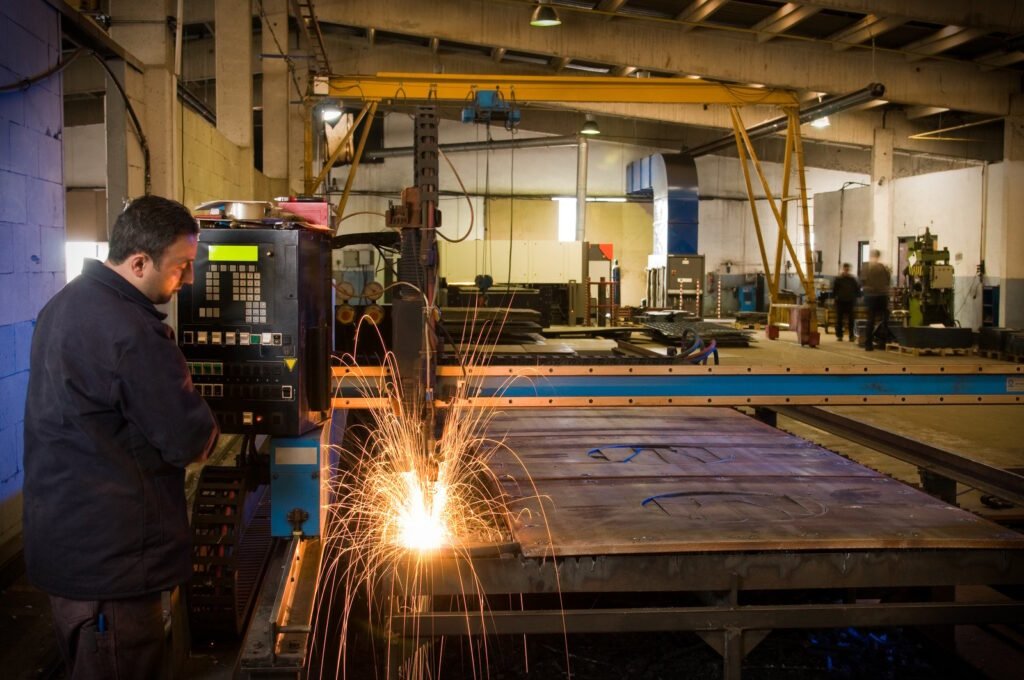
Plasma cutting is a transformative technology that benefits various industries including automotive, aerospace, construction, and metal art. It offers remarkable speed and precision in cutting metals of different thicknesses. This method enhances operational efficiency by minimizing material waste and labor costs while ensuring high-quality results. Plasma cutters are versatile tools that adapt to diverse materials and complex designs, making them invaluable in modern manufacturing processes. Additionally, their eco-friendly nature aligns with the industry’s sustainability goals. Discover how plasma cutting can elevate your operations and artistic endeavors.
What Does Backlash Mean on a Milling Machine and Why Is It Important?
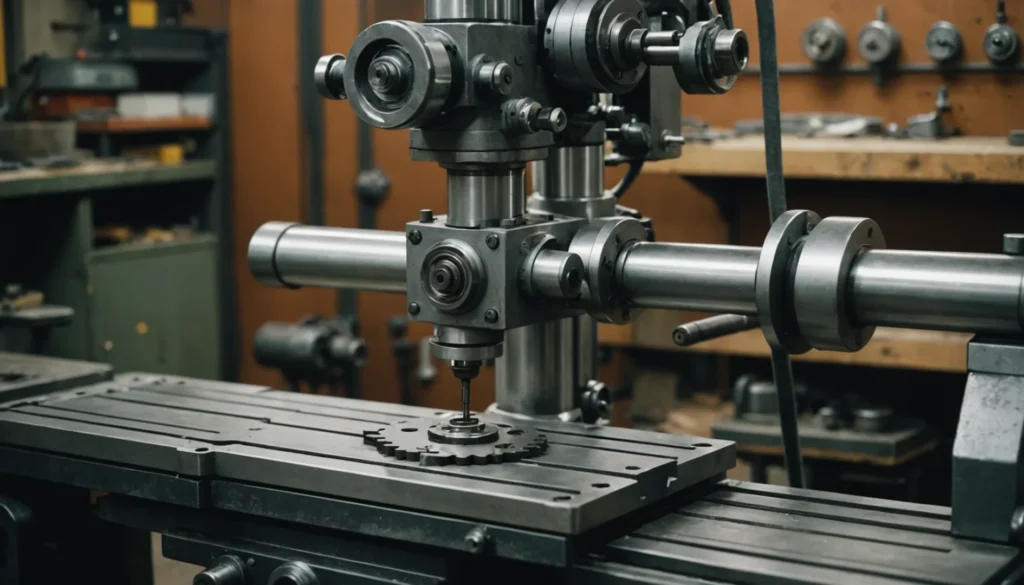
Understanding backlash is key to mastering the art of precision machining on milling machines. This phenomenon can significantly impact dimensional accuracy, surface quality, and overall machining performance. In this post, I explore what backlash is, how it affects machining, and practical ways to mitigate its effects.
What Should You Consider When Choosing a Custom CNC Turning Lathe?
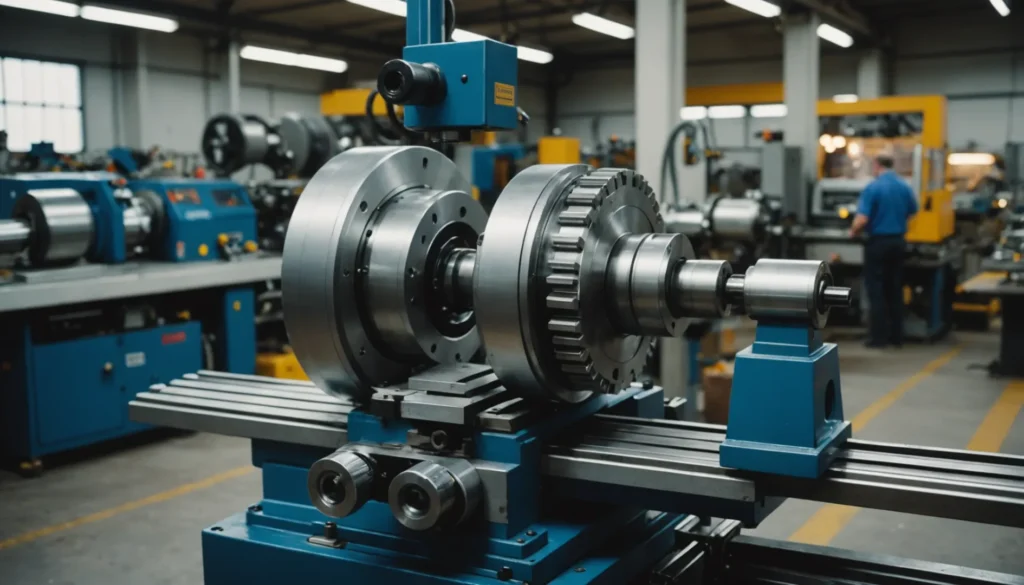
Selecting the right custom CNC turning lathe involves evaluating several critical factors. Key considerations include the size and complexity of parts to be machined, required precision levels for different industries, material characteristics that affect tool wear and machining efficiency, as well as performance parameters like spindle speed and torque. Additionally, understanding the costs associated with purchase and operation is essential for budget management. Automation features can enhance productivity by reducing manual intervention. Ultimately, aligning these factors with your specific operational needs will ensure optimal performance and long-term satisfaction with your CNC lathe investment.
What Are the Best Applications for CNC Machines?
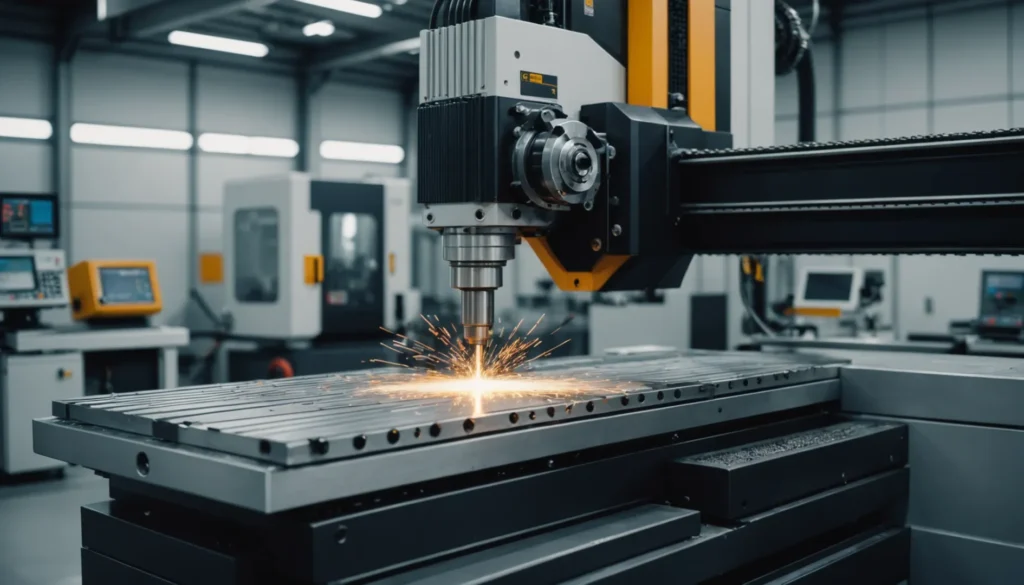
CNC machines have transformed manufacturing by enabling high precision and automation across multiple industries. In aerospace, they create critical aircraft parts; in automotive, they ensure engine component accuracy. Electronics benefit from CNC’s ability to produce intricate circuit boards and heat sinks. Mold manufacturing relies on CNC for crafting detailed molds essential for plastic products. Additionally, the medical field utilizes CNC technology to manufacture surgical instruments and implants with exceptional precision. This article explores how different sectors leverage CNC machines to optimize production processes while maintaining stringent quality standards.
Is Investing in a CNC Machine Worth It for Your Business?

Investing in a CNC machine can significantly boost your business’s production efficiency, product quality, and market competitiveness. While the initial financial outlay is substantial, the long-term benefits often outweigh these costs. CNC machines automate machining processes, reduce manual errors, and allow for continuous operation, which enhances productivity. They also offer flexibility to adapt to changing production requirements quickly. However, businesses must evaluate their specific needs, budget constraints, and potential return on investment before making such a significant purchase. Understanding both the upfront costs—including equipment purchase and installation—and ongoing operational expenses is crucial for ensuring that this investment aligns with long-term growth strategies.
What Are the Best Alternatives to CNC Milling Machines?
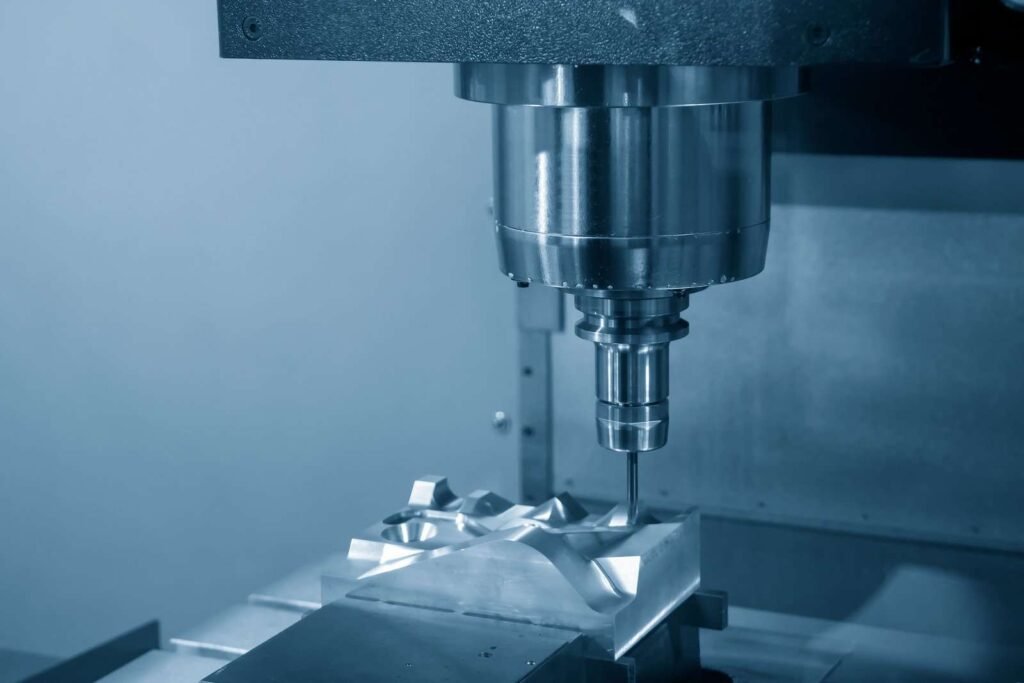
This blog post discusses the best alternatives to CNC milling machines, highlighting traditional manual and semi-automatic milling options, as well as advanced technologies like 3D printing (FDM and SLA) and laser cutting. Each method is explored in terms of its advantages for different tasks such as small batch production, prototyping, and intricate designs. The article emphasizes the importance of selecting the right tool based on project complexity, precision requirements, and budget constraints. Whether you’re a hobbyist or a professional seeking efficiency in manufacturing processes, understanding these alternatives can help you make informed decisions that align with your specific needs.
What Are the Key Advantages of Using a Milling Machine?

Milling machines are indispensable tools in modern manufacturing. They offer unparalleled precision and versatility, enabling engineers to create complex parts with exceptional accuracy. This article explores the key advantages of milling machines, including their efficiency, material compatibility, and cost-effectiveness, providing insights into how they can transform your manufacturing processes.