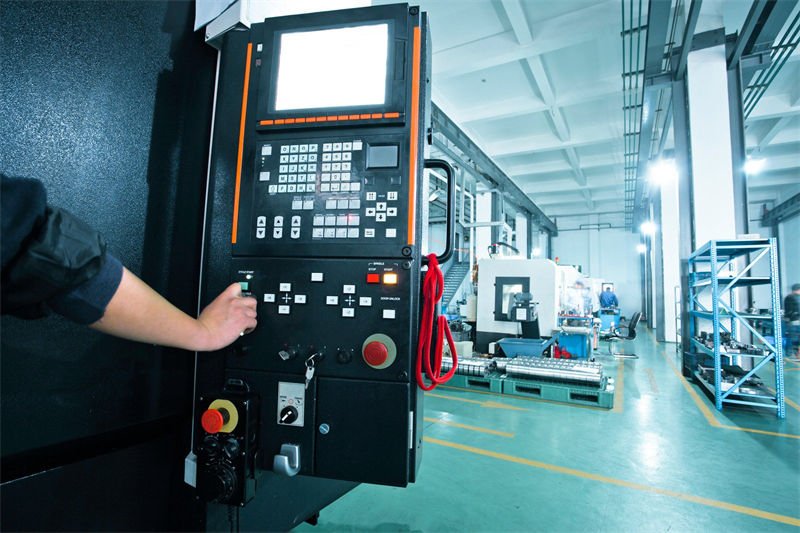
Ever wondered what makes a CNC machine truly universal? Let’s explore the fascinating features that make these machines a game-changer in manufacturing.
Universal CNC machines stand out due to their ability to perform a wide range of machining operations, handle complex shapes, and maintain high precision, making them ideal for diverse industrial applications.
While we’ve touched on the core attributes of these machines, there’s so much more to uncover about how they operate, adapt, and enhance productivity across various sectors.
Universal CNC machines can perform both milling and drilling.True
Universal CNC machines integrate multiple operations like milling and drilling.
How Do Universal CNC Machines Enhance Machining Efficiency?
Universal CNC machines are revolutionizing efficiency in the machining industry through their multifunctional capabilities and precision.
Universal CNC machines enhance machining efficiency by integrating multiple operations, offering high precision, and reducing setup times. These machines streamline production processes, decrease manual intervention, and allow for versatile applications across various industries.
Multifunctional Capabilities
Universal CNC machines excel by consolidating numerous machining operations into a single system. These machines can perform milling, drilling, reaming, boring, and tapping without transferring workpieces between different stations. For example, when creating complex mechanical parts, the machine can seamlessly switch from milling contours to drilling installation holes. This integration reduces the setup time and minimizes error risks associated with multiple transfers.
High-Precision Engineering
Equipped with advanced mechanical structures, universal CNC machines achieve remarkable precision. Components like high-precision guides and ball screws ensure minimal vibration during operations. The machine’s advanced control systems1 meticulously monitor tool positions, maintaining accuracy within ±0.01 mm. This level of precision is crucial when machining components such as precision molds and mechanical parts.
Automated Tool Changing Systems
The incorporation of automatic tool changers significantly boosts productivity. These systems can accommodate a diverse range of tools and automate the transition between different machining tasks. During the production of parts with multiple features, the machine can autonomously switch from a milling cutter to a drill bit, then to a reamer, without manual intervention. This automation not only saves time but also enhances consistency across batches.
Enhanced Programming Flexibility
Programming software such as Mastercam and UG empowers CNC machines with exceptional flexibility. These tools generate optimized tool paths based on 3D models, reducing idle movements and cutting time. They also simulate machining processes to preemptively address potential collisions or errors. This programming optimization2 ensures that machining is both efficient and safe.
Feature | Benefit |
---|---|
Multifunctionality | Reduces setup times and minimizes transfer errors |
High Precision | Ensures accuracy for complex and high-precision parts |
Automation | Increases efficiency by automating tool changes |
Flexible Programming | Optimizes machining paths for improved safety and reduced cycle times |
Universal CNC machines reduce setup times.True
They integrate multiple operations, minimizing the need for transfers.
Manual tool changes are common in universal CNC machines.False
Automatic tool changers automate transitions, reducing manual intervention.
What Industries Benefit the Most from Universal CNC Machines?
Universal CNC machines have revolutionized various industries by offering unmatched versatility and precision. But which sectors benefit the most from these technological marvels?
Industries such as aerospace, automotive, and mold manufacturing gain significant advantages from universal CNC machines due to their ability to handle complex shapes, ensure high precision, and perform diverse operations efficiently.
Aerospace Industry
The aerospace industry3 significantly benefits from universal CNC machines due to their ability to machine complex and precise components like engine blades and structural parts. These machines can handle intricate designs and materials, ensuring reliability and safety in aircraft manufacturing. The flexibility in programming allows for customization in production, catering to specific aerodynamic needs.
Automotive Industry
In the automotive sector4, universal CNC machines play a crucial role in producing engine components, transmission parts, and other critical elements with high precision. Their ability to integrate multiple machining processes, such as milling and drilling, into one setup reduces production time and costs. The adaptability of CNC machines also supports the innovation and customization required in modern vehicle design.
Component Type | Machining Operations | Benefits of CNC Machines |
---|---|---|
Engine Blocks | Milling, Boring | Precision, Reduced Time |
Transmission Parts | Reaming, Tapping | Cost-Effective, High Quality |
Mold Manufacturing
Universal CNC machines are indispensable in the mold manufacturing industry5. These machines can produce molds with intricate details and high precision, essential for injection molding and die-casting processes. The automatic tool changers enhance efficiency by allowing rapid transitions between different machining tasks without manual intervention.
Medical Device Manufacturing
The medical device industry6 requires components with stringent quality standards and precision. Universal CNC machines enable the production of complex parts used in medical equipment and implants. Their ability to work with biocompatible materials while maintaining accuracy ensures that medical devices meet regulatory standards and patient safety requirements.
Renewable Energy Sector
In the renewable energy field7, CNC machines contribute significantly by manufacturing components for wind turbines and solar panels. Their precision ensures optimal performance and efficiency in energy generation technologies. The capability to handle large-scale projects makes them ideal for sustainable energy initiatives.
CNC machines reduce automotive production costs.True
By integrating multiple processes, CNC machines lower costs.
Mold manufacturing doesn't benefit from CNC machines.False
CNC machines enhance precision and efficiency in mold making.
How Do Universal CNC Machines Achieve High Precision?
Universal CNC machines are renowned for their exceptional precision, a critical factor in modern manufacturing success.
Universal CNC machines achieve high precision through advanced mechanical structures, state-of-the-art control systems, and cutting-edge technologies such as compensation and feedback mechanisms.
Advanced Mechanical Structures
Universal CNC machines are built with high-precision mechanical components that are fundamental to achieving accurate machining. The machine bed, guides, and ball screws are precisely manufactured and assembled to minimize vibration and error during operation. For example, high-precision guides ensure the smooth movement of the worktable, while ball screws provide accurate displacement control for both worktables and cutting tools.
Table: Mechanical Components of Universal CNC Machines
Component | Function |
---|---|
Machine Bed | Provides stability and support for precision machining |
Guides | Ensure straightness and smoothness of worktable movement |
Ball Screws | Control displacement with high precision |
Cutting-Edge Control Systems
The integration of sophisticated CNC systems enables universal CNC machines to perform precise position control and motion trajectory planning. These systems manage the movement of cutting tools across multiple axes with remarkable accuracy. Feedback devices, like grating scales, continuously monitor the tool’s position, allowing real-time adjustments to maintain machining precision.
In applications requiring high precision, such as precision mold machining8, these systems ensure the positioning accuracy is within ±0.01 mm and repeat positioning accuracy is about ±0.005 mm.
Advanced Detection and Compensation Technologies
Universal CNC machines utilize innovative detection and compensation technologies to enhance precision further. These technologies involve real-time monitoring of factors like temperature changes and tool wear that could affect machining accuracy. By compensating for these variables, CNC machines maintain high precision even in dynamic operating environments.
For instance, thermal compensation systems adjust for temperature-induced distortions, ensuring consistent output quality. Similarly, tool wear detection systems predict when tools need replacing or reconditioning, thereby reducing downtime and maintaining precision throughout the production process.
These technological innovations make universal CNC machines indispensable in industries that require exacting standards, such as aerospace and automotive manufacturing. By leveraging these advancements, manufacturers can produce complex parts with tight tolerances efficiently and reliably.
Universal CNC machines use ball screws for precise control.True
Ball screws enable accurate displacement control for CNC machines.
Thermal compensation systems are not used in CNC machines.False
Thermal compensation systems adjust for temperature-induced distortions.
What Makes Programming Universal CNC Machines Flexible?
Universal CNC machines are renowned for their adaptability in programming, allowing manufacturers to tailor operations for various tasks. But how do they achieve this flexibility?
Programming flexibility in universal CNC machines is achieved through advanced software, multi-axis capabilities, and diverse coding options, enabling precise control over complex machining operations.
Versatile Programming Software
One of the key aspects of flexibility in programming universal CNC machines lies in the use of advanced CNC programming software such as Mastercam9 and UG (Unigraphics)10. These tools allow operators to create intricate programs tailored to specific machining tasks. With user-friendly interfaces and powerful features, these programs simplify the creation of complex tool paths, even for parts with challenging geometries.
- Automatic Toolpath Generation: The software can automatically generate toolpaths from 3D models, significantly reducing manual input and errors.
- Simulation Capabilities: Before actual machining, operators can simulate the process to identify potential issues, such as collisions or inefficiencies, enhancing both safety and productivity.
Multi-Axis Machining
Universal CNC machines often support multi-axis machining, including three, four, or even five-axis operations. This capability allows for simultaneous movement across multiple axes, providing greater flexibility in machining complex parts.
- Complex Geometry Handling: Multi-axis machining enables the production of intricate shapes by allowing the cutting tool to approach the workpiece from various angles.
- Reduction of Setups: It reduces the need for multiple setups, saving time and increasing efficiency.
Diverse Coding Options
Programming these machines involves a variety of coding languages, primarily G-codes and M-codes, which offer extensive control over machine functions.
- G-Codes: These codes dictate specific movements and positions of the machine parts.
- M-Codes: These manage miscellaneous functions like tool changes and coolant flow.
The ability to customize these codes allows operators to adapt the machine’s operations to meet specific requirements efficiently.
Real-Time Adjustments and Feedback
Modern universal CNC machines are equipped with real-time feedback systems that enable operators to make adjustments during the machining process.
- Adaptive Control: Some systems can automatically adjust machining parameters based on real-time feedback, optimizing performance.
- Error Detection: Immediate detection and correction of errors enhance precision and reduce waste.
Through these technologies, universal CNC machines provide a flexible platform that can be adapted to a wide range of manufacturing scenarios.
Mastercam software generates automatic toolpaths.True
Mastercam simplifies CNC programming by automatically creating toolpaths from 3D models.
Multi-axis CNC machines require more setups than single-axis.False
Multi-axis machining reduces the need for multiple setups, enhancing efficiency.
Conclusion
Universal CNC machines are redefining manufacturing with unmatched versatility and precision. Dive deeper into their capabilities to unleash efficiency and innovation in your production processes.
-
Discover how control systems enhance precision in CNC operations.: MIP utilizes FANUC controls to power a 12-axis machine that produces consistent, precision tool parts, increasing productivity by more than 300%. ↩
-
Learn how programming optimizations improve CNC machining efficiency.: 1 Choose the right tools · 2 Optimize the cutting parameters · 3 Simplify the program structure · 4 Use advanced techniques · 5 Test and verify your … ↩
-
Explore how CNC machines optimize aerospace component production.: One of the most significant benefits of CNC machining in aerospace is its ability to fabricate lightweight components. Aerospace engineers … ↩
-
Learn how CNC technology enhances automotive part precision.: CNC machines for auto parts are used to produce high-quality and consistent parts, reducing the risk of errors and increasing efficiency. ↩
-
Discover the role of CNC machines in efficient mold creation.: CNC machining is the leading production style for mold making. Molds are most commonly machined out of tool steel and stainless steel, but aluminum is also … ↩
-
Find out how CNC precision is vital for medical device quality.: CNC machining is utilized in the production of microdevices used in various medical applications, including biosensors and diagnostic systems. These devices … ↩
-
See how CNC technology aids renewable energy advancements.: The CNC machining renewable energy industry efficiently creates functional parts and advanced equipment, from solar cells to hydraulic valves for the oil and … ↩
-
Discover how CNC machines achieve high precision in mold manufacturing.: We offer three axis and five axis CNC machining as well as CNC boring for all industries. EDM Machining in Michigan We provide sinker type electrical discharge … ↩
-
Discover how Mastercam simplifies CNC programming with automatic toolpath generation.: Mastercam delivers innovative CAD/CAM software and solutions that solve the world’s manufacturing challenges. Intuitive and easy to use. ↩
-
Learn about UG’s role in creating efficient CNC machining programs.: What are the Benefits of Unigraphics? · It reduces NC programming and machining time. · Improves finishing, accuracy, and quality of the surface. · It reduces … ↩