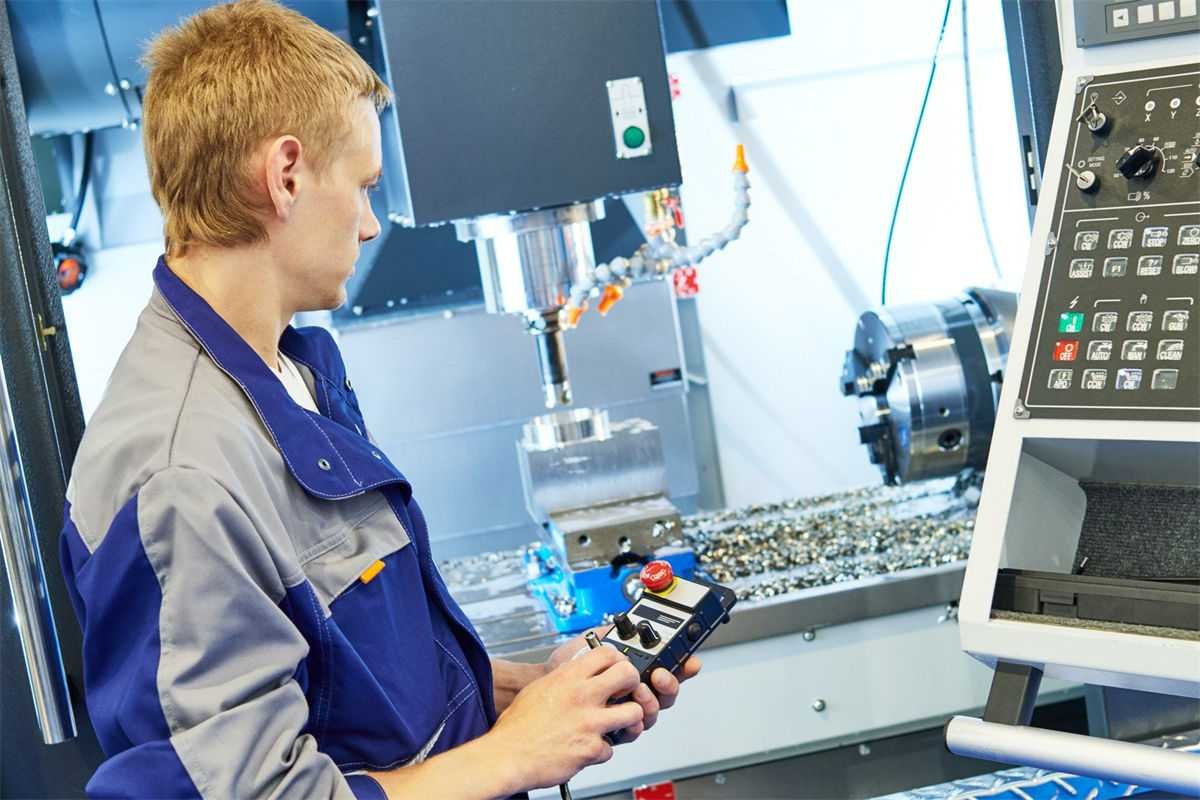
Have you ever wondered how intricate parts are created with precision in manufacturing? Let me take you on a journey through the fascinating world of vertical milling machines!
A vertical milling machine features a spindle oriented vertically, allowing for precise cutting and shaping. Key benefits include efficient flat-surface milling, contouring capabilities, and multifunctional operations like drilling and tapping, making it ideal for various industrial applications.
While understanding these primary features provides a solid foundation, diving deeper into the specific applications and advantages of vertical milling machines can reveal insights crucial for both seasoned professionals and those new to the field.
Vertical milling machines have horizontally oriented spindles.False
Vertical milling machines feature vertically oriented spindles, not horizontal.
How Does a Vertical Milling Machine Compare to a Horizontal Milling Machine?
Vertical milling and horizontal milling machines each have distinct features that cater to different manufacturing needs.
Vertical milling machines have a vertically oriented spindle, ideal for flat surface milling and detailed work. In contrast, horizontal milling machines feature a horizontally oriented spindle, suited for heavy-duty tasks and large-scale production due to their robust build and greater material removal capabilities.
Structural Differences
Vertical and horizontal milling machines differ primarily in spindle orientation. In vertical milling machines1, the spindle is perpendicular to the worktable, enabling operations like flat-surface milling, contouring, and drilling. Conversely, horizontal machines have a spindle parallel to the worktable, allowing the use of multiple cutters and handling heavier workpieces.
Table: Comparison of Spindle Orientation
Feature | Vertical Milling | Horizontal Milling |
---|---|---|
Spindle Orientation | Perpendicular to worktable | Parallel to worktable |
Primary Operations | Flat-surface, contouring, drilling | Heavy-duty cutting, slotting |
Machining Capabilities
The vertical milling machine excels in precision work and versatility. It can handle intricate designs and is commonly used for detailed jobs such as die sinking and mold making. On the other hand, the horizontal milling machine2 is designed for more aggressive material removal, making it suitable for larger, heavier components like gears and shafts.
Application Fields
Vertical mills are prevalent in industries requiring precision and detailed work, such as mold manufacturing and equipment maintenance. Horizontal mills dominate sectors that demand bulk processing, such as automotive and aeronautics, where efficiency in cutting large volumes is crucial.
- Vertical Milling: Ideal for detailed parts, smaller batch production.
- Horizontal Milling: Suited for large-scale production with repetitive tasks.
Cost Considerations
Typically, vertical milling machines are more affordable, making them accessible to smaller businesses or workshops focusing on precision tasks. In contrast, horizontal mills are an investment for large manufacturing facilities due to their higher initial cost but greater productivity in bulk production.
By understanding these differences, manufacturers can select the appropriate milling machine that aligns with their operational needs and budget constraints.
Vertical mills are more affordable than horizontal mills.True
Vertical mills typically cost less, making them accessible for small businesses.
Horizontal mills are ideal for detailed mold manufacturing.False
Horizontal mills are suited for heavy-duty tasks, not detailed work like molds.
What Are the Specific Advantages of Using a Vertical Milling Machine in Mold Manufacturing?
Vertical milling machines are indispensable in mold manufacturing, offering unmatched precision and versatility.
In mold manufacturing, vertical milling machines provide superior precision in shaping mold cavities and contours, essential for producing high-quality molds. Their vertical spindle orientation allows for efficient material removal, flexibility in complex contour milling, and multitasking capabilities, such as drilling and tapping, crucial for intricate mold designs.
Enhanced Precision in Mold Cavity Shaping
Vertical milling machines excel at achieving high precision required for mold cavity shaping3. The vertically oriented spindle allows tools to reach into deeper cavities while maintaining tight tolerances. This is especially critical in producing molds for injection molding, where even minor deviations can lead to defective products.
Key Precision Features:
- Spindle Orientation: Vertical spindles provide better control over depth and position.
- Tool Versatility: Accommodates various tools like face mills and end mills for detailed work.
- Stable Worktable: Ensures minimal vibration, enhancing accuracy.
Flexibility in Complex Contour Milling
The versatility of vertical milling machines shines in their ability to mill complex contours. This flexibility is particularly advantageous in mold manufacturing, where molds often require intricate shapes.
Applications in Mold Manufacturing:
- Creating complex geometric forms with precision.
- Customizing molds with unique design features.
- Streamlining the production of complex parts by reducing setup changes.
Multifunctional Operations Enhance Efficiency
Vertical milling machines offer multifunctional capabilities beyond just milling. They can also perform drilling, reaming, and tapping, making them a one-stop solution for mold manufacturing needs.
Operation | Description | Benefit |
---|---|---|
Drilling | Creating holes for inserts or fasteners | Enhances mold assembly flexibility |
Reaming | Refining hole precision | Ensures tight fit and alignment |
Tapping | Adding threads to holes | Facilitates easy assembly with bolts |
Practicality in Small-Batch Mold Production
In small-batch production scenarios, vertical milling machines offer quick setup and adaptability. This is crucial for rapid prototyping and custom mold designs, where the ability to switch between operations efficiently can save time and reduce costs.
For instance, when a custom mold design4 requires specific features or adjustments, vertical milling machines allow manufacturers to swiftly implement changes without extensive downtime. This adaptability is vital for meeting tight deadlines in dynamic production environments.
Vertical milling machines excel in mold cavity shaping.True
Their precision and spindle orientation make them ideal for shaping molds.
Vertical milling machines are limited to milling only.False
They can also perform drilling, reaming, and tapping operations.
Why Is Spindle Orientation Crucial in Milling Machines?
Spindle orientation is a defining characteristic of milling machines, affecting precision and versatility in machining.
Spindle orientation in milling machines determines the direction of the tool’s cutting force. Vertical spindles allow for precise vertical cuts, while horizontal spindles facilitate high-speed horizontal operations. This orientation impacts machining efficiency, accuracy, and the types of operations a machine can perform.
The Fundamentals of Spindle Orientation
In a milling machine, the spindle orientation5 dictates how the cutting tool engages with the workpiece. This orientation can be either vertical or horizontal, significantly influencing the machine’s capabilities and applications.
Vertical Spindle:
-
The spindle is aligned perpendicularly to the worktable, enabling precise vertical cuts. This setup is ideal for tasks requiring accuracy, such as flat-surface milling and contouring.
-
Machines with vertical spindles can perform multiple operations, including drilling and tapping, enhancing their versatility.
Horizontal Spindle:
-
Here, the spindle is parallel to the worktable, allowing for high-speed horizontal cutting. This setup excels in removing large volumes of material quickly and efficiently.
-
These machines are often employed for heavy-duty tasks like slab milling and slotting, where precision is less critical than speed.
Impact on Machining Capabilities
Spindle orientation directly influences a milling machine’s operational efficiency and the variety of tasks it can perform:
-
Precision and Accuracy: Vertical spindles offer superior precision for detailed work, making them indispensable in industries requiring meticulous attention to detail.
-
Material Removal Rates: Horizontal spindles are better suited for aggressive material removal, providing a faster solution for less intricate machining tasks.
Aspect | Vertical Spindle | Horizontal Spindle |
---|---|---|
Precision | High | Moderate |
Material Removal Rate | Moderate | High |
Suitable Operations | Flat-surface milling, contouring | Slab milling, slotting |
Versatility | Multifunctional | Specialized |
Applications Across Industries
Each spindle orientation has its niche within different sectors:
-
Vertical Milling Machines: Predominantly used in sectors that demand intricate and precise machining like mold manufacturing and automotive industries.
-
Horizontal Milling Machines: More common in industries where rapid material removal is prioritized over precision, such as large-scale metal fabrication and construction.
Understanding the nuances of spindle orientation allows professionals to select the right machine for their specific needs, optimizing productivity and ensuring quality outcomes. Exploring these differences6 can lead to more informed decisions in machinery investments.
Vertical spindles are better for high-speed operations.False
Vertical spindles excel in precision, not speed, unlike horizontal ones.
Horizontal spindles allow for rapid material removal.True
Horizontal spindles are designed for fast material removal, enhancing efficiency.
What Role Does a Vertical Milling Machine Play in Small-Batch Production?
In small-batch production, precision and adaptability are paramount, and vertical milling machines deliver both effortlessly.
Vertical milling machines streamline small-batch production by offering flexibility in machining various parts with precision. Their capability to perform multiple operations like milling, drilling, and tapping on a single setup makes them indispensable in producing limited quantities efficiently.
The Versatility of Vertical Milling Machines
Vertical milling machines excel in small-batch production due to their adaptability and efficiency. With the spindle oriented vertically, these machines can perform diverse operations without frequent setup changes. This flexibility is crucial for small batches where frequent part changes7 and unique specifications are commonplace.
For instance, when manufacturing custom brackets or fittings, a vertical milling machine can seamlessly transition between milling flat surfaces and intricate contour milling. This adaptability reduces downtime and increases productivity, allowing for quicker turnarounds on small orders.
Precision in Limited Runs
Small-batch production often demands high precision, especially in industries like aerospace or medical device manufacturing. Vertical milling machines provide the necessary accuracy by maintaining tight tolerances during machining processes. By utilizing digital readouts (DROs) and CNC capabilities, operators can ensure each piece meets exact specifications, reducing material waste and rework.
Cost-Effectiveness and Efficiency
The ability to perform multiple operations such as drilling, tapping, and milling in a single setup translates to cost savings. For businesses engaged in low-volume manufacturing8, the reduced need for different machines minimizes equipment costs and shop floor space.
Furthermore, vertical milling machines require less manual intervention once set up correctly, freeing operators to manage other tasks or machines, optimizing labor efficiency.
Application in Diverse Industries
Whether it’s repairing equipment9 or creating prototypes, vertical milling machines are invaluable in various sectors. In maintenance operations, these machines can quickly machine spare parts or tools required for repairs, minimizing downtime.
Similarly, in prototyping, the ability to rapidly produce and modify parts helps designers iterate designs effectively, speeding up the development process for new products.
Vertical milling machines offer precision in small batches.True
Vertical mills maintain tight tolerances, ensuring high precision.
Vertical milling machines require frequent setup changes.False
They perform diverse operations with minimal setup changes.
Conclusion
Vertical milling machines are indispensable for precision, versatility, and efficiency in manufacturing. Understanding their features empowers informed decisions in your operational journey.
-
Learn more about the precision capabilities of vertical mills.: Simplicity: Vertical mills require no additional fixtures and are relatively simple to operate and maintain. The smaller learning curve means …
-
Explore why horizontal mills are ideal for heavy-duty tasks.: Speed: If you need a machine that offers high output and a quick turnaround time, a horizontal milling machine can cut faster than a vertical …
-
Explore how vertical milling enhances precision in mold cavity shaping.: Generally speaking, vertical milling machines are more economical and space-efficient. They can easily carry out elaborate mold-making because they are suitable …
-
Discover how vertical milling aids in flexible, custom mold production.: Vertical milling machines have the benefit of being usually less complicated than horizontal milling machines. Vertical milling machines are thus more cost- …
-
Discover how spindle orientation affects machining processes and capabilities.: The Spindle Orientation lets you position the spindle to a programmed angle. This option provides inexpensive, accurate positioning.
-
Understand the key distinctions to choose the right milling machine.: Horizontal milling machines feature shorter and thicker tools capable of taking deeper cuts and removing more material than vertical milling machines.
-
Understand how to manage frequent part changes efficiently.: Since you’re starting new batches more often, there is an increase in downtime. Each time you change something in your product design, you have …
-
Discover the advantages of low-volume manufacturing approaches.: These benefits of low volume manufacturing include: Lower costs: Eliminate excessive tooling costs that require minimum orders to be offset, reduce barriers to …
-
Learn how vertical mills assist in quick equipment repairs.: I got an awesome new milling machine from an auction, but its broken and its time to fix it! Thank …