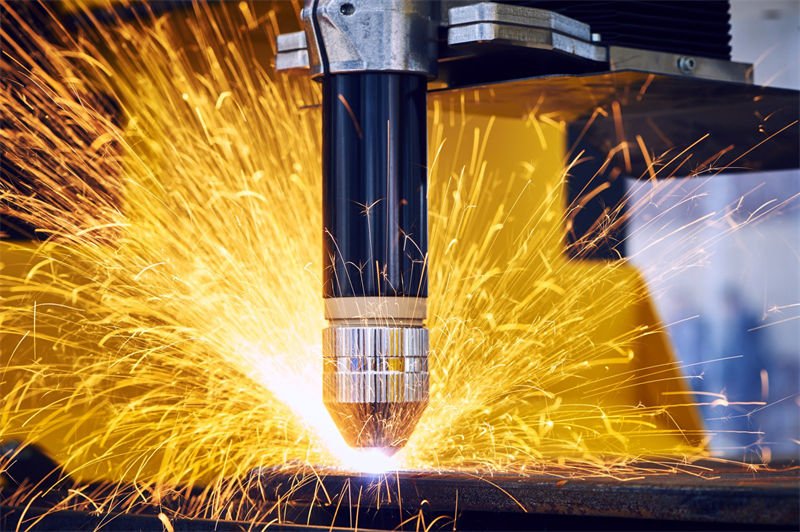
When I first started working with plasma cutters, I was amazed by their power and precision.
Plasma cutters are incredible tools that allow for precise and fast cutting of metals. To work efficiently, ensure proper preparation, including a stable power supply and suitable gas selection, manage your cutting speed and arc voltage, and maintain your equipment regularly.
But there’s so much more to it! Let’s explore each aspect in detail so you can take your plasma cutting skills to the next level.
Plasma cutters require a stable power supply for optimal performance.True
A stable power supply prevents voltage fluctuations, ensuring consistent cutting quality.
What Preparation Steps Are Essential Before Using a Plasma Cutter?
Preparation is key to achieving high-quality cuts with a plasma cutter.
Essential preparation steps for using a plasma cutter include ensuring a stable power supply and grounding, selecting appropriate gas types, and performing thorough torch inspections.
Ensuring a Stable Power Supply and Grounding
A plasma cutter requires an independent and stable power supply1 to function optimally. Sharing the power source with other large equipment can lead to voltage fluctuations, adversely affecting cutting quality. Proper grounding is equally crucial. The grounding resistance should meet the equipment’s specifications, which can be verified using a professional grounding resistance tester. Effective grounding minimizes electromagnetic interference and enhances operator safety. In workshops with numerous electrical devices, a dedicated grounding line for the plasma cutter can significantly reduce arc instability.
Selecting the Right Gas Type and Adjusting Gas Pressure
The choice of gas is critical and depends on the material and its thickness. For instance, pure argon gas might be ideal for thin plate cutting, whereas medium-thick carbon steel often requires compressed air. However, attention must be paid to the air’s humidity and impurity levels. Installing air drying and filtering devices can be beneficial. Moreover, the gas pressure must be precisely adjusted; optimal values are typically determined through several tests. For example, a 6mm thick stainless steel plate can achieve superior cutting quality using an argon-hydrogen mix (approximately 95% argon and 5% hydrogen) at a pressure of 0.5 – 0.6 MPa.
Thorough Torch Inspection
Before each use, inspect the torch carefully, focusing on the electrode and nozzle wear. Even slight wear can cause arc instability and compromise cutting quality, while severe wear necessitates immediate replacement. Keeping spare electrodes and nozzles on hand allows for quick swaps as needed. Additionally, examine the torch’s cooling system to ensure that coolant circulates correctly or air cooling channels remain unobstructed, preventing torch overheating and potential damage.
These preparatory steps form the foundation for successful plasma cutting operations, setting the stage for efficient and high-quality metalworking results.
Proper grounding reduces arc instability in plasma cutting.True
Grounding minimizes electromagnetic interference, enhancing stability.
Pure argon is ideal for cutting medium-thick carbon steel.False
Compressed air is preferred for medium-thick carbon steel, not argon.
How Do You Optimize Cutting Speed and Arc Voltage?
Optimizing cutting speed and arc voltage is key to achieving precise and efficient plasma cuts.
To optimize cutting speed and arc voltage, consider material type, thickness, current settings, and use trial cuts to find optimal settings. Adjust arc voltage automatically or manually for consistent quality.
Understanding the Basics of Cutting Speed and Arc Voltage
Cutting speed and arc voltage are critical parameters in plasma cutting. The cutting speed influences the quality of the cut edges, while the arc voltage affects the stability and concentration of the cutting arc. Understanding these parameters can lead to more precise cuts and reduced waste.
The Importance of Material and Thickness
Different materials require different cutting speeds. For instance, cutting aluminum2 may demand a different speed than carbon steel due to their inherent properties. Thickness also plays a crucial role: thicker materials generally need slower cutting speeds to ensure clean cuts.
Determining Optimal Cutting Speed
The optimal cutting speed is not a fixed number but varies based on several factors, including material type, thickness, and current settings. Here’s a simplified guide:
Material | Thickness (mm) | Current (A) | Speed (mm/min) |
---|---|---|---|
Aluminum | 10 | 200 | 200 – 250 |
Carbon Steel | 6 | 150 | 150 – 200 |
Stainless Steel | 5 | 180 | 180 – 230 |
Trial cuts are essential to find the perfect balance, as they allow operators to observe cut quality and adjust speeds accordingly.
Fine-Tuning Arc Voltage for Quality Cuts
Arc voltage adjustments can often be handled by an automatic system that changes the voltage based on torch-to-workpiece distance. However, manual adjustments might be necessary for complex shapes or varying thicknesses.
- High Arc Voltage: Leads to a dispersed arc, causing heat to spread over a larger area. This can result in wider kerfs and less defined edges.
- Low Arc Voltage: Risks forming a double arc, which can damage the torch and compromise cut quality.
Manual fine-tuning can ensure the arc remains stable, especially in intricate workpieces with height differences.
Real-World Applications and Adjustments
Consider a workshop scenario: when cutting a complex shape on a variable thickness plate, an operator might manually adjust the arc voltage to maintain consistency in cut quality. Similarly, when encountering slag or irregular cuts during operation, adjusting the speed or voltage based on real-time feedback can mitigate issues.
For optimal results, continual monitoring and adjustments are necessary. Implementing systems that record parameters such as current, voltage, and speed can help operators refine their techniques over time.
Higher arc voltage results in wider kerfs.True
Higher arc voltage disperses the arc, causing wider kerfs.
Thicker materials require faster cutting speeds.False
Thicker materials need slower speeds for clean cuts.
Why Is Torch Maintenance Crucial for Efficiency?
Torch maintenance is the cornerstone of efficient plasma cutting, ensuring precision and longevity of the equipment.
Regular maintenance of the torch is vital for efficient plasma cutting. It prevents wear-related issues like unstable arcs and decreased cutting quality, ensuring the machine operates at peak performance.
The Importance of Regular Torch Inspection
A well-maintained torch is less likely to suffer from issues that affect cutting quality and machine performance. Before each use, inspect the torch meticulously, focusing on the wear of the electrode and nozzle. Even slight wear can result in unstable arcs, compromising the precision of cuts. Regular checks can preemptively identify wear-related problems, allowing for timely replacements.
Example: In a busy metalworking shop, a thorough inspection routine revealed minor nozzle wear, preventing potential disruptions.
Maintaining the Cooling System
Ensuring that the torch’s cooling system is functioning optimally is essential to prevent overheating. Whether the system uses air or liquid coolant, blockages or leaks can lead to torch damage. Regular maintenance includes checking coolant circulation and cleaning air channels to maintain unobstructed cooling pathways.
Example: By routinely cleaning air cooling channels with compressed air, a fabricator extended the life of their torch significantly.
Cleaning and Storage Practices
After each use, cleaning the torch can prevent residue buildup that affects performance. Specialized tools should be used to remove slag and dust effectively, safeguarding against any impact on subsequent cuts.
Additionally, when the torch is not in use, proper storage conditions—such as dry environments away from direct sunlight—are recommended to prevent moisture damage and corrosion.
The Role of Spare Parts
Having spare electrodes and nozzles on hand ensures that any necessary replacements can be made without delay. This preparedness minimizes downtime and maintains consistent cutting quality.
Example: A workshop equipped with a stockpile of spare parts was able to swiftly address a worn electrode issue, avoiding production halts.
Routine Data Analysis for Predictive Maintenance
Recording and analyzing data from each cutting session helps in identifying trends and predicting maintenance needs. By monitoring variables such as arc voltage stability and cut quality, it becomes easier to plan maintenance schedules effectively.
Example: Data analysis showed increased roughness in cuts, leading to an early diagnosis of electrode wear and subsequent adjustments.
Learn more about plasma cutting maintenance3
By prioritizing torch maintenance, operators not only enhance efficiency but also extend the lifespan of their plasma cutters. This proactive approach fosters reliability and optimal performance across various metalworking projects.
Regular torch maintenance prevents unstable arcs.True
Regular checks prevent wear-related issues, ensuring stable arcs.
Spare parts are unnecessary for plasma cutting efficiency.False
Having spare parts minimizes downtime and maintains cutting quality.
What Role Does Data Analysis Play in Plasma Cutting?
Data analysis is the backbone of optimizing plasma cutting, ensuring precision, efficiency, and problem-solving in metal fabrication.
In plasma cutting, data analysis helps in fine-tuning cutting parameters by examining past performance metrics like current, voltage, and speed. This practice improves cut quality, reduces waste, and preempts equipment issues.
Enhancing Precision with Data Analysis
Data analysis in plasma cutting involves collecting and examining data from previous cuts to make informed decisions about future operations. By analyzing metrics such as current levels4, arc voltage, and gas pressure, operators can fine-tune settings for optimal performance.
For instance, recording the current and voltage used during cutting allows for the identification of patterns that affect cut quality. If a trend shows increasing roughness on cut edges over time, it might indicate electrode wear. Adjusting maintenance schedules based on these insights can preemptively address such issues.
Improving Efficiency Through Data Insights
Efficiency in plasma cutting isn’t just about speed; it’s about balancing speed with quality. Data analysis helps in identifying the optimal cutting speed5 for different materials and thicknesses. By keeping records of speed versus outcome data, operators can determine the best speeds to use without compromising on quality.
For example, if the data shows that a slower speed leads to less dross on thicker materials, operators can adjust their techniques accordingly. Furthermore, tracking gas consumption rates against cut quality can help in optimizing gas mixtures for better results.
Anticipating and Mitigating Equipment Issues
By regularly analyzing data such as gas flow rates6 and arc stability metrics, potential equipment problems can be identified before they cause significant downtime. Anomalies in data may point to issues like clogged nozzles or leaks in gas lines, prompting timely interventions.
For example, a sudden drop in gas flow rate might indicate a blockage that could lead to poor cuts if not addressed. Regular data reviews allow operators to spot these issues early and schedule maintenance accordingly.
Building a Knowledge Base for Continuous Improvement
Documenting data from each plasma cutting session builds a comprehensive knowledge base. This resource is invaluable for training new operators or when troubleshooting complex problems. It can guide adjustments and improvements in processes over time, contributing to continuous improvement in cutting quality and efficiency.
Incorporating data analysis into plasma cutting processes not only enhances the immediate quality of cuts but also builds a foundation for long-term success and innovation in metalworking.
Data analysis optimizes plasma cutting precision.True
Analyzing past performance metrics fine-tunes cutting parameters.
Gas flow rates don't affect plasma cutting quality.False
Gas flow rates impact cut quality by influencing arc stability.
Conclusion
Embracing these principles will not only enhance your plasma cutting efficiency but also prolong your equipment’s life. Start implementing these strategies today!
-
Learn why stable power ensures high-quality cuts and device longevity.: All plasma power supplies can produce a higher voltage (than the rated voltage) and a higher Wattage output, but the power supply has to work …
-
Discover ideal speeds for aluminum to enhance cut quality.: Our Cobot Cutter can easily cut faster than 100 IPM (depending on thickness). So you can almost eliminate distortion from excessive heat and …
-
Explore detailed maintenance strategies to boost plasma cutter efficiency.: Maintenance of your plasma cutting machine can help reduce the risk of breakdown. Here is a detailed guide on the maintenance of your plasma cutting …
-
Discover how current levels influence precision and efficiency.: Yes, voltage preset is proportional to cut height, higher voltage equals higher height. The height control reads the actual arc voltage as if you had a …
-
Learn how to determine the best cutting speeds.: Learn how to set up your plasma cutter for maximum results. We’ll also include handy charts to help you adjust settings based on material type and thickness.
-
Understand how gas flow rates affect cutting performance.: Common causes for low flow rates include insufficient air hose diameter, to many or contaminated air filters, or debris in air line. It is …