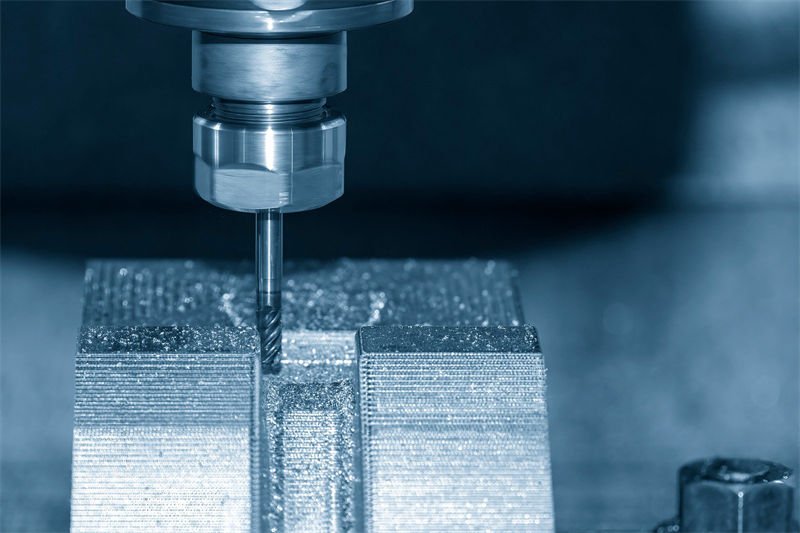
Unlock the potential of your milling machine by mastering the art of cutting perfect rectangular shapes.
To cut rectangular shapes with a milling machine, utilize face milling for flat surfaces and peripheral milling for contours. CNC programming enhances precision and efficiency, enabling sharp corners and accurate dimensions.
While the basic principles provide a quick overview, delving deeper into each method reveals the nuances and detailed steps necessary for professional-grade results. Continue reading to uncover advanced techniques and tips for optimizing your milling process.
Face milling creates flat surfaces on rectangles.True
Face milling uses a rotating cutter to efficiently remove material, creating flat surfaces.
What is Face Milling and How Does It Work?
Face milling is a critical technique used in machining to achieve flat surfaces on workpieces.
Face milling involves using a rotating cutter with multiple cutting edges to remove material from the surface of a workpiece, creating a flat surface. The cutter rotates perpendicular to the workpiece surface, ensuring efficient material removal and smooth finishes.
Understanding Face Milling
Face milling is one of the most common and versatile milling operations used in various industries. The primary goal is to create flat surfaces on the workpiece, which can be crucial for ensuring that parts fit together seamlessly in an assembly.
Unlike peripheral milling, where the cutting edges are on the periphery of the cutter, face milling uses a cutter with teeth on the face and periphery. This allows for cutting at multiple points simultaneously, making it highly efficient for larger surfaces.
Tools and Equipment
The tooling for face milling typically involves a face mill cutter that attaches to the spindle of a milling machine. These cutters come in various sizes, enabling them to handle different scales of workpieces efficiently. The choice of cutter depends on factors such as the material of the workpiece, the required surface finish, and the machine’s capacity.
Tool Type | Features | Suitable For |
---|---|---|
Face Mill | Multiple teeth on face & edge | Large surface areas |
Fly Cutter | Single-point cutting tool | Fine finishing tasks |
Working Principle
The face milling process involves securing the workpiece on the machine’s worktable and adjusting the cutter’s height to achieve the desired depth of cut. The cutter is then set to rotate perpendicular to the surface being milled. As the cutter rotates, its teeth engage the workpiece, slicing away material with each pass.
The worktable moves in either X or Y direction (or both) to cover the entire surface area, ensuring uniform material removal. The depth of cut, feed rate, and spindle speed must be carefully adjusted to optimize efficiency and surface finish.
Applications and Advantages
Face milling is predominantly used in applications where flat surfaces are crucial, such as creating parting lines for molds or preparing stock for further machining.
The advantages of face milling include:
- Efficiency: Multiple cutting edges allow for faster material removal compared to single-point operations.
- Versatility: Applicable to a wide range of materials including metals, plastics, and composites.
- Surface Finish: Capable of producing a high-quality surface finish suitable for many applications.
To explore more about how face milling is implemented in specific industrial applications, consider looking into industrial face milling techniques1.
Face milling uses a single-point cutting tool.False
Face milling uses a cutter with multiple teeth, not a single-point tool.
Face milling creates flat surfaces on workpieces.True
The primary purpose of face milling is to achieve flat surfaces.
How Does Peripheral Milling Shape Rectangular Contours?
Peripheral milling is key for precision machining of rectangular contours, ensuring accuracy and smooth edges.
Peripheral milling shapes rectangular contours by using an end mill cutter to follow the perimeter of a rectangle, ensuring precise edge formation and dimensional accuracy.
Understanding Peripheral Milling
Peripheral milling is a process that focuses on machining the outer edges or the periphery of a workpiece. This method is particularly advantageous for creating detailed shapes, such as rectangles, with high precision. The key to successful peripheral milling lies in the selection of an appropriate end milling cutter and the accurate control of its movement along the workpiece’s contour.
Step-by-Step Process
-
Tool Selection: Choose an end milling cutter suitable for the material and the desired edge finish. The diameter of the cutter should be compatible with the dimensions of the rectangle to ensure precision.
-
Workpiece Setup: Securely clamp the workpiece onto the milling machine’s table. Proper alignment is crucial to maintain the accuracy of the milled contours.
-
Path Programming: Program the milling machine to follow the rectangle’s perimeter. This involves setting precise movement instructions for the X-axis and Y-axis to guide the tool along each side.
-
Executing the Cut: Start milling along one long edge of the rectangle, ensuring that the tool maintains a consistent distance from the workpiece’s edge.
-
Corner Transition: As the cutter reaches a corner, it must change direction smoothly to continue along the adjacent side without overshooting or undercutting.
-
Completing the Contour: Continue this process until all four sides of the rectangle are milled. Ensure that each side is straight and adheres to dimensional specifications.
Benefits of CNC in Peripheral Milling
CNC programming enhances peripheral milling by offering unparalleled control over tool paths. Through precise G-code commands, operators can dictate exact movements, ensuring consistent results across multiple parts. This is particularly beneficial in batch production, where maintaining uniformity is essential.
Incorporating CNC also allows for real-time adjustments to be made if deviations from expected dimensions occur during machining. This adaptability is invaluable in maintaining quality standards while minimizing material waste.
Practical Application: Milling a Rectangular Mold Insert
Consider a scenario where you need to mill a rectangular mold insert. By leveraging peripheral milling techniques2, you can achieve sharp, well-defined edges that meet stringent industry standards. The ability to precisely follow complex contours without manual intervention ensures that each mold produced is identical, thus enhancing product consistency and reliability.
Peripheral milling uses an end mill cutter.True
End mill cutters are essential for precise edge formation in peripheral milling.
Peripheral milling is unsuitable for rectangular contours.False
Peripheral milling is ideal for shaping rectangular contours with high precision.
Why is CNC Programming Essential for Milling Rectangles?
Discover how CNC programming revolutionizes the precision and efficiency of milling rectangular shapes.
CNC programming is crucial for milling rectangles as it ensures precise tool paths, consistent cutting speeds, and repeatable results, enhancing accuracy and efficiency in machining processes.
Understanding CNC Programming in Milling
CNC programming is the heart of modern machining, converting complex engineering designs into precise machine instructions. For milling rectangular shapes, CNC programming plays a critical role in defining accurate tool paths3, which is essential for maintaining the integrity of rectangular dimensions.
Tool Path Precision: By utilizing G-codes and M-codes, CNC programming defines the exact trajectory of the milling cutter. This precision ensures that each side of the rectangle is cut to the specified length and angle, minimizing errors that are common in manual operations. For instance, when executing a program with commands such as G01 for linear interpolation, the machine precisely follows the specified path, resulting in straight edges and sharp corners.
Consistent Cutting Speeds: Another advantage of CNC programming is its ability to maintain consistent cutting speeds across different sections of the rectangle. By controlling spindle speed and feed rates through M03 (spindle forward rotation) and other commands, CNC programs prevent material overheating and tool wear, leading to a cleaner cut and longer tool life.
Enhancing Efficiency and Repeatability
CNC machines shine in their ability to perform repetitive tasks with high precision. Once a program is written for a specific rectangle size, it can be reused for batch production, significantly reducing setup time and human error. Batch production benefits4 from this repeatability, providing uniform parts that meet exact specifications every time.
Automated Adjustments: In addition to accuracy, CNC programming allows for real-time adjustments during the milling process. This adaptability is crucial when dealing with material inconsistencies or unexpected obstacles, as programs can be modified on-the-fly without stopping production.
Examples of CNC Programming Impact
Consider a scenario where a manufacturing company needs to produce 500 rectangular metal plates with identical dimensions. Using CNC programming, the process becomes streamlined:
- Program Setup: Engineers create a single program with all necessary parameters for cutting each rectangle.
- Execution: The same program runs continuously on CNC machines, ensuring each plate matches the required dimensions.
- Quality Control: Post-production checks confirm that each piece adheres to quality standards due to the machine’s consistent performance.
CNC programming thus not only enhances precision but also boosts operational efficiency by minimizing waste and reducing manual interventions during milling operations.
CNC programming ensures precise tool paths for milling.True
CNC uses G-codes to define exact trajectories, ensuring precision.
Manual milling is more efficient than CNC for rectangles.False
CNC enhances efficiency with repeatability and automation.
Can Milling Machines Achieve Sharp Internal Corners?
Mastering the precision of milling machines can help achieve sharp internal corners effectively.
Milling machines struggle with sharp internal corners due to the tool’s radius. Utilizing specialized cutting tools or additional processes like EDM can help achieve the desired sharpness.
Challenges of Achieving Sharp Internal Corners
Milling machines inherently face difficulties when attempting to create sharp internal corners. This challenge arises primarily due to the radius of the milling cutter, which limits its ability to reach perfect 90-degree angles internally. When the tool navigates around the corner, it leaves behind a small radius that prevents the corner from being truly sharp.
To illustrate, imagine a typical end mill used in a milling machine. As the cutter approaches a corner, it cannot make an abrupt 90-degree turn without leaving a radius equal to half its diameter. Therefore, achieving completely sharp internal corners is virtually impossible with standard milling tools.
Overcoming Limitations with Specialized Tools
One way to counteract this limitation is by utilizing specialized cutting tools designed for intricate internal geometries. These tools include smaller-diameter end mills or corner-rounding end mills, which can minimize the leftover radius. For example, if you need a very sharp internal corner, opting for a smaller tool can reduce the radius significantly.
Table: Tool Options for Sharp Corners
Tool Type | Typical Use Case | Benefits |
---|---|---|
Small End Mills | Tight internal corners | Reduced radius |
Corner Rounding | Smooth transitions in contours | Enhanced edge definition |
Incorporating EDM for Precision
For industries where extremely sharp internal corners are non-negotiable, integrating electrical discharge machining (EDM) post-milling is a viable solution. EDM utilizes electrical discharges to remove material and can precisely shape corners that milling machines cannot reach. By combining both milling and EDM, manufacturers can achieve intricate details and meet stringent design specifications.
This method proves particularly advantageous in applications requiring high-precision components such as molds or aerospace parts, where every millimeter counts.
Conclusion
While traditional milling machines have limitations regarding sharp internal corners, combining different techniques and tools5 can overcome these challenges effectively. For precise and complex geometries, considering alternative methods like EDM ensures that design intentions are fully realized without compromise.
Milling machines can achieve perfect 90-degree internal corners.False
Due to the tool's radius, milling machines can't achieve perfect 90-degree corners.
EDM can be used to achieve sharp internal corners after milling.True
EDM removes material with precision, creating sharper corners post-milling.
Conclusion
Mastering these milling techniques empowers you to efficiently craft precise rectangular shapes, enhancing your machining capabilities.
-
Explore practical industrial uses and benefits of face milling techniques.: This technique is commonly used at all stages of machining, but it is most often chosen for preliminary (rough) cutting.
-
Explore how peripheral milling enhances precision and efficiency in mold making.: A face mill removes material from the workpiece’s top surface, an end mill (and its larger cousin, the shell mill) removes it from the part’s periphery.
-
Learn how CNC ensures precise tool paths for flawless milling.: Controlling tool paths is essential for optimal machining outcomes, including surface finish and dimensional accuracy. Additionally, tool paths …
-
Explore how CNC enhances efficiency in batch production.: Using CNC machines for batch production can streamline the workflow because of the reliability, accuracy, and speed of CNC-based manufacturing.
-
Explore advanced techniques for achieving sharper corners with milling machines.: Optimizing sharp corners in CNC machining is achievable by early design consideration, proper use of non-CNC and a CNC process, and …