
Have you ever marveled at the intricate designs on your favorite jewelry piece? Those delicate patterns are often made possible by the magic of laser cutting!
Lasers can cut a variety of materials. For metals, it can cut carbon steel, stainless steel, aluminum and aluminum alloys, copper and copper alloys. For non-metals, it is suitable for wood, plastic, leather, ceramics and glass. The cutting principles of different materials vary due to their characteristics.
But there’s so much more to explore beyond just the basics of which materials can be cut! Join me as we delve into the fascinating world of laser cutting technology, its applications, and how to ensure safety while working with it.
Lasers can safely cut PVC materials.False
PVC produces toxic fumes when cut with lasers, posing safety hazards.
How Does Laser Cutting Work?
Laser cutting uses focused light beams to cut materials with high precision and efficiency.
Laser cutting uses a high-power density laser beam to irradiate the workpiece, causing the material to rapidly heat up and melt and vaporize. At the same time, the molten material is blown away by auxiliary gas to achieve cutting.
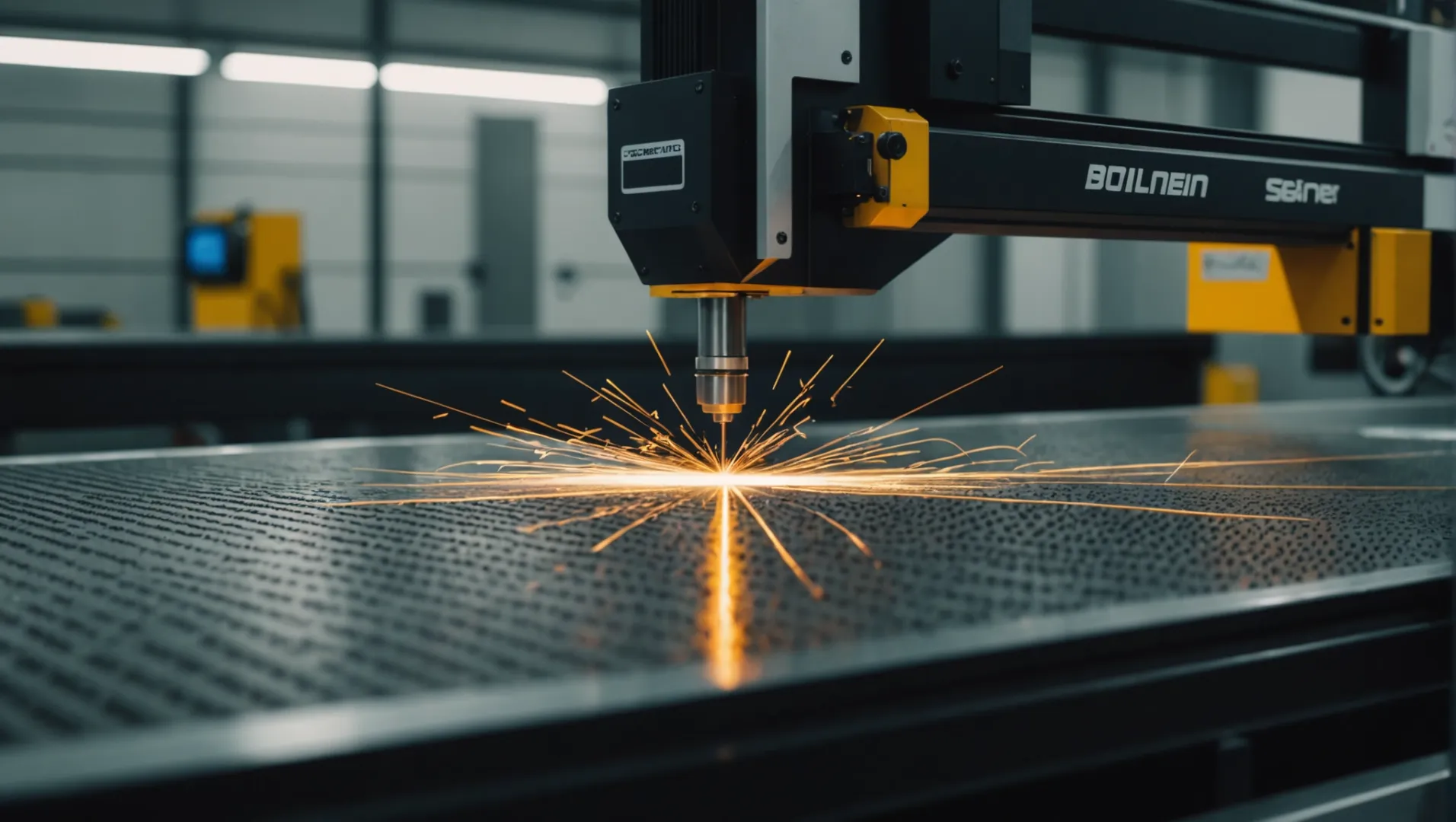
The Basics of Laser Cutting
Laser cutting involves directing the output of a high-power laser through optics. The focused laser beam is guided by computer numerical control (CNC) to follow a defined path, allowing it to cut or engrave the desired pattern into the material. This process relies heavily on precision, as even minor deviations can affect the quality of the cut.
Types of Lasers Used in Cutting
There are several types of lasers commonly used in laser cutting:
- CO2 Lasers: Suitable for cutting, boring, and engraving non-metallic materials like wood and acrylic.
- Fiber Lasers: Known for cutting metals such as stainless steel and aluminum with high precision.
- Nd:YAG Lasers: Primarily used for applications requiring high energy density.
Each type has its own advantages and limitations, making the choice of laser crucial depending on the material and application.
How Lasers Interact with Materials
The interaction between the laser beam and the material is critical for effective cutting. For example, metals absorb laser light effectively, allowing fiber lasers to cut through them easily. On the other hand, non-metals like glass or PVC have different absorption rates, which can lead to suboptimal results or hazards.
The table below highlights how different materials react to laser cutting:
Material | Laser Compatibility | Notes |
---|---|---|
Carbon Steel | High | Excellent for precision parts |
Stainless Steel | High | Common in industrial applications |
Aluminum | Medium | Requires careful control due to reflectivity |
Acrylic | High (with CO2) | Ideal for creating clear, polished edges |
PVC | Low | Produces toxic fumes; not recommended |
Glass | Low | Can shatter due to thermal stress during cutting |
Applications Across Industries
Laser cutting’s versatility makes it indispensable in numerous industries. For instance, in jewelry making1, it allows for the creation of intricate designs in metals such as gold and silver. In the automotive industry2, it facilitates the production of custom parts with unmatched precision.
In each application, understanding the material properties and aligning them with the appropriate laser technology ensures optimal results.
Safety and Precision
While laser cutting offers precision, it also demands strict adherence to safety protocols. Proper ventilation is essential when cutting materials like PVC to avoid exposure to harmful fumes. Additionally, training in handling CNC machines can mitigate risks associated with high-powered lasers.
By understanding how laser cutting works and tailoring practices to specific materials, industries can leverage this technology for maximum efficiency and innovation.
CO2 lasers are ideal for cutting metals.False
CO2 lasers are best for non-metallic materials like wood and acrylic.
Fiber lasers are used for cutting stainless steel.True
Fiber lasers excel in cutting metals, including stainless steel, with precision.
What Are the Advantages of Laser Cutting?
Laser cutting has revolutionized manufacturing with its precision and versatility, making it indispensable across industries.
Laser cutting has many advantages. It has high cutting precision and can achieve complex and fine shape cutting. The cutting speed is fast and the efficiency is high. The heat affected zone is small, reducing the damage to material properties. The incision quality is good and the edge is smooth. Moreover, it is non-contact cutting, which causes little damage to materials and has wide applicability.
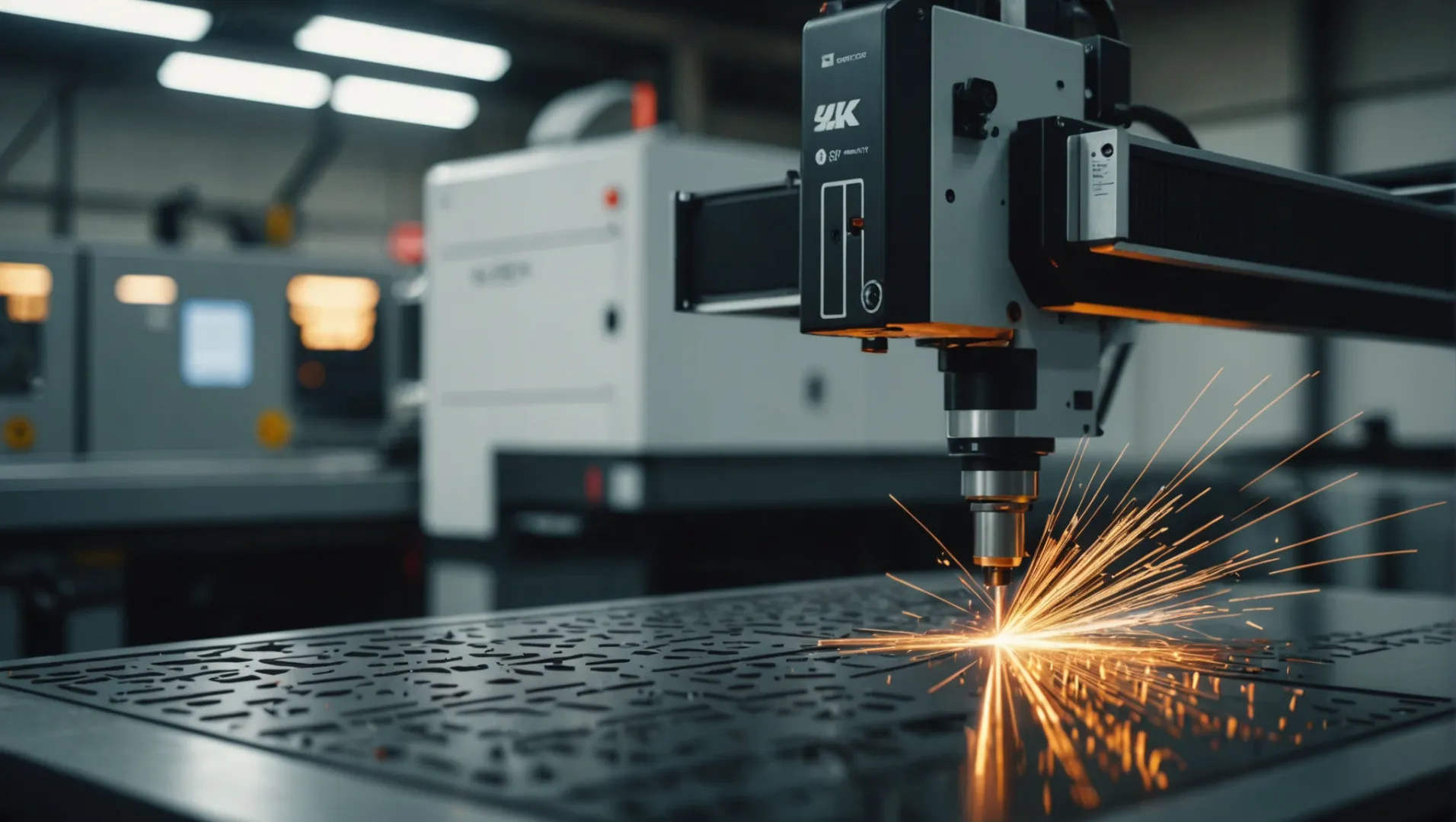
High Precision and Accuracy
One of the standout advantages of laser cutting is its remarkable precision and accuracy. Laser cutters can achieve complex shapes and intricate designs with minimal tolerance levels, which is crucial in industries like electronics manufacturing3 and jewelry making. This precision reduces the need for additional processing or finishing work, saving both time and resources.
Efficiency and Speed
Laser cutting is also known for its efficiency and speed. Unlike traditional cutting methods that might require multiple passes or setups, laser cutting can complete tasks in a single pass, significantly reducing production time. This speed is particularly beneficial in high-volume production environments, such as automotive manufacturing4, where time efficiency translates to cost savings.
Versatility Across Materials
The ability to cut a wide range of materials—from metals like carbon steel and aluminum to delicate items like thin sheets of metal—adds to the versatility of laser cutting. This adaptability makes laser cutters a preferred choice in industries like eyewear manufacturing5, where materials and design requirements vary widely.
Material Type | Examples | Laser Cutting Suitability |
---|---|---|
Metals | Carbon steel, aluminum | High |
Non-metals | PVC, fiberglass | Low (due to safety risks) |
Minimal Material Waste
Laser cutting is an efficient process that minimizes material waste. The focused laser beam allows for tight nesting of parts on the material sheet, ensuring maximum usage of the available surface. This not only reduces costs but also contributes to more sustainable manufacturing practices by minimizing scrap.
Reduced Risk of Material Contamination
Since laser cutting is a non-contact process, there’s a reduced risk of contaminating the material being cut. This is crucial in industries such as medical device manufacturing6, where maintaining material integrity is vital.
By examining these facets, it’s clear that laser cutting not only enhances productivity but also opens doors to innovative applications across diverse sectors. Understanding these advantages can help you leverage laser technology to its fullest potential.
Laser cutting minimizes material waste effectively.True
The focused laser beam allows tight nesting, reducing waste.
Non-metals like PVC are highly suitable for laser cutting.False
PVC is less suitable due to safety risks during laser cutting.
Which Industries Benefit Most from Laser Cutting?
Laser cutting technology is revolutionizing industries with its precision and versatility, becoming indispensable in various sectors.
The industries such as automobile manufacturing, electronics, aerospace, architecture, and advertising packaging benefit the most from laser cutting. Automobiles use it to cut parts with high precision. The electronics industry can precisely process circuit boards. Aerospace cuts special materials. Architecture enhances precision and aesthetics. Advertising packaging creates exquisite products.
Automotive Industry: Precision and Customization
The automotive sector thrives on precision engineering and customization. Laser cutting enables the production of intricate parts with high accuracy, essential for modern vehicles. It is especially beneficial in cutting lightweight materials like aluminum, crucial for manufacturing fuel-efficient vehicles. The ability to produce complex geometries quickly also supports rapid prototyping and innovation.
Electronics: Miniaturization and Complexity
In the electronics industry, miniaturization and the need for intricate designs are paramount. Laser cutting provides the precision required to produce tiny components such as circuit boards and connectors. It ensures clean cuts without damaging sensitive electronic materials, facilitating the manufacturing of compact and efficient devices.
Jewelry: Intricate Designs in Precious Metals
The jewelry industry greatly benefits from laser cutting’s ability to work with precious metals like gold and silver. The technology allows for the creation of detailed and precise designs that were previously difficult to achieve. This precision enables jewelers to offer customized pieces, meeting specific customer demands with high-quality finishes.
Eyewear: Delicate Frames and Components
In the eyewear industry, laser cutting is used to create delicate frames and detailed components. This technology allows manufacturers to design lightweight, durable, and aesthetically pleasing glasses. It also enables the production of custom-fit eyewear, enhancing both functionality and style for consumers.
Lighting: Decorative and Functional Elements
Laser cutting is employed in the lighting industry to design both decorative and functional elements. It allows for the creation of intricate patterns on metal sheets used in lamps and fixtures, contributing to unique design aesthetics while maintaining structural integrity.
Expanding Horizons: Future Applications
While these industries currently benefit significantly from laser cutting, ongoing advancements in laser technology continue to expand its applications. For instance, the development of new laser types may eventually enable safe cutting of non-metal materials, broadening the scope of industries that can leverage this technology.
By understanding how various industries utilize laser cutting7, businesses can better align their production processes to maximize efficiency and innovation while adhering to safety standards. As technology evolves, staying informed about the latest developments is crucial for maintaining a competitive edge.
Laser cutting is essential in automotive for lightweight materials.True
Laser cutting enables precise shaping of aluminum, crucial for fuel efficiency.
Jewelry industry rarely uses laser cutting for intricate designs.False
Laser cutting is widely used for detailed designs in precious metals like gold.
What Safety Precautions Should Be Taken When Laser Cutting?
Laser cutting is an impressive technology, but safety remains paramount. How can you ensure a safe environment?
When performing laser cutting, wear appropriate goggles to prevent damage to the eyes from lasers. Ensure good ventilation in the work area to expel smoke and exhaust gas generated by cutting. Set up protective screens to avoid accidental leakage of laser beams. Ground and protect equipment from leakage, and also perform regular maintenance and inspections.
The Importance of Ventilation
One of the foremost safety considerations in laser cutting is ensuring proper ventilation systems8 are in place. During the cutting process, harmful fumes and particulates can be released, particularly when cutting certain metals or coated materials. Effective ventilation helps to eliminate these dangers by filtering out hazardous air contaminants. It’s crucial to routinely inspect and maintain your ventilation setup to keep it functioning efficiently.
Protective Gear for Laser Cutting
While operating a laser cutter, wearing appropriate protective gear is non-negotiable. Protective eyewear, specifically designed to shield against laser wavelengths, is essential to prevent potential eye damage. Additionally, depending on the materials being cut, operators might need respiratory protection to avoid inhaling any residual particulates or fumes.
Fire Safety Precautions
Given that lasers generate heat, the risk of fire must not be underestimated. Ensure that your workspace is equipped with appropriate fire extinguishers and that they are easily accessible. Regularly check that all materials around the laser cutter are non-flammable and keep a safe distance between any combustible materials and the laser cutting area.
Fire Safety Checklist:
Item | Action Required |
---|---|
Fire Extinguishers | Regularly inspect and test |
Combustible Materials | Store safely and away |
Smoke Detectors | Ensure functionality |
Equipment Maintenance and Operator Training
Routine maintenance of the laser cutting machine not only prolongs its lifespan but is critical for safety. Regular checks should be carried out on the laser optics, cooling systems, and control panels to prevent malfunctions.
Moreover, comprehensive training for operators is vital. They must be well-versed in not only the operational aspects of the machine but also emergency protocols. This training ensures they can respond appropriately if any issues arise during the cutting process.
By following these safety guidelines, you can minimize risks associated with laser cutting and create a safer work environment.
Proper ventilation is essential in laser cutting.True
Ventilation removes harmful fumes released during the cutting process.
Fire extinguishers are optional in laser cutting areas.False
Fire extinguishers are necessary due to the heat generated by lasers.
Conclusion
By understanding laser cutting capabilities and prioritizing safety, you can unlock its full potential for your projects.
-
Explore how lasers create intricate jewelry designs efficiently.: Among the main advantage of laser cutters is the ability to create unique shapes and custom engraved parts. Whatever shape and design you want, …
-
Learn about precision and customization in auto part production.: What are the benefits of laser cutting in the automotive industry? · Clean and perfect cuts – no edge reworking necessary · No material fixation necessary …
-
Explore the importance of precision in electronics manufacturing.: Laser cutting is an efficient, safe, and extremely accurate method compared to other traditional sheet metal-cutting techniques.
-
Understand how laser cutting boosts automotive production efficiency.: Laser cutting improves production speed and efficiency, shortening the manufacturing cycle and increasing throughput. The flexibility of laser …
-
Discover why laser cutting is ideal for eyewear production.: A laser cutting machine can quickly produce several styles of eyeglass frames, solving the problem of personalized customization, which is very …
-
Learn about non-contact processing benefits in medical device production.: Non-contact measurement is another increasingly required feature of medical device metrology solutions. Non-contact measurement can be …
-
Explore diverse industrial applications of laser cutting technology.: Learn about the many industries that rely on precision laser cutting, including agriculture, military, construction, and contract manufacturing.
-
Explore advanced ventilation options for safer laser cutting environments.: Wondering if there are recommendations for in-house exhaust or air filtration systems to replace venting laser cutting fumes externally from the …