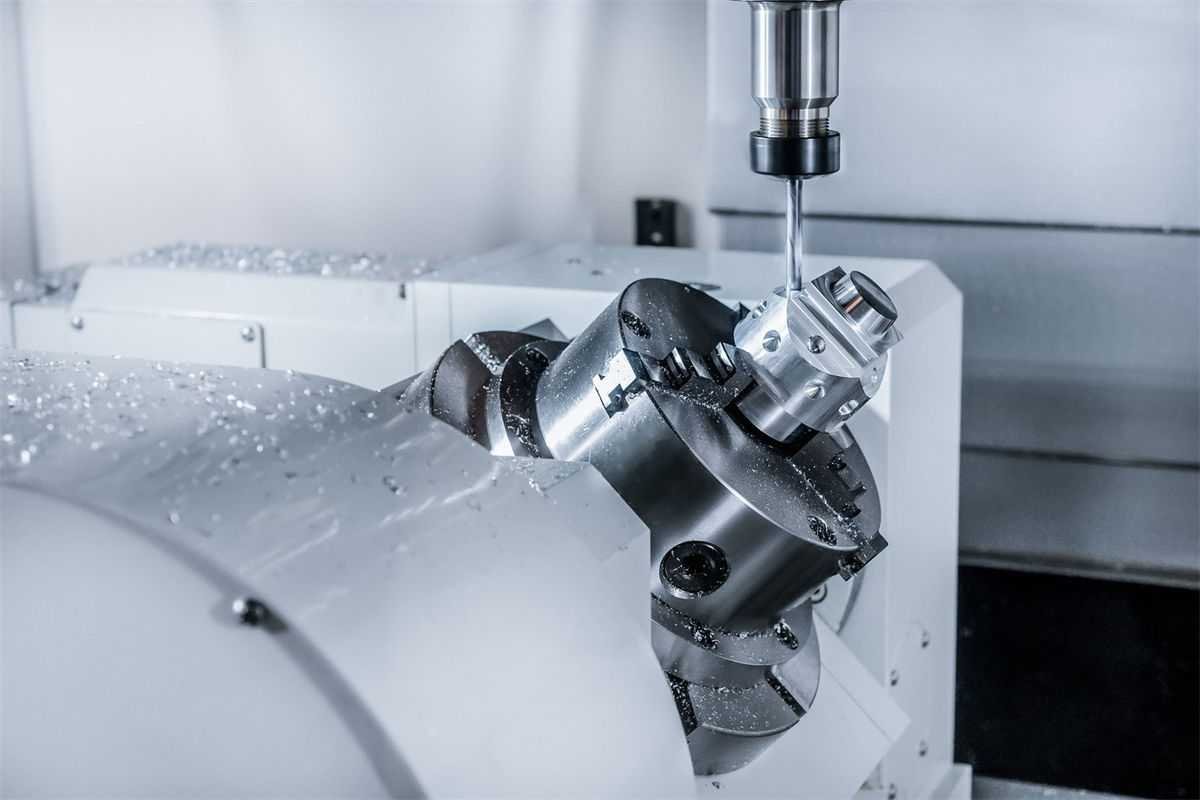
In the bustling world of manufacturing, where every second counts and precision is non-negotiable, milling machines stand out as a lifeline for engineers and manufacturers alike.
Milling machines offer a plethora of benefits such as high precision, versatility in operations, efficiency in production, material compatibility, and excellent surface finishes. These advantages make them essential in industries ranging from aerospace to automotive and electronics.
Understanding these advantages in detail can illuminate how milling machines can revolutionize your production process. Let’s dive deeper into each benefit!
Milling machines offer high precision with tolerances of 0.004mm.True
Milling machines achieve high precision through CNC technology, crucial for industries needing tight tolerances.
How Do Milling Machines Achieve High Precision?
Milling machines are renowned for their precision, achieving tolerances as tight as 0.004mm, crucial for high-demand industries.
Milling machines achieve high precision through advanced structural designs, CNC technology, and precise control over movement. By utilizing guides, transmission devices, and software, they ensure dimensional and shape accuracy essential for industries requiring tight tolerances.
Structural Design and Precision
The structural design of milling machines plays a pivotal role in achieving high precision. CNC (Computer Numerical Control) milling machines are equipped with precise guides and transmission devices that manage the movement of the worktable and the cutting tool. This level of control ensures that positioning accuracy can reach as tight as ±0.01mm or even higher.
For instance, in the aerospace industry, where precision is non-negotiable, CNC mills can machine parts like turbine blades with exact dimensional accuracy and shape accuracy. This involves precise control over the X, Y, and Z axes to maintain flatness, cylindricity, and groove dimensions.
CNC Technology and Automation
CNC technology is at the heart of achieving high precision in milling machines. By programming the machine to follow exact coordinates and paths, human error is minimized. This is crucial in industries such as medical device manufacturing, where any deviation can be detrimental.
Using advanced CAM software1, operators can pre-plan machining operations to ensure that every cut and movement adheres to the strictest standards of precision. Moreover, the inclusion of Automatic Tool Changing (ATC) systems further enhances precision by ensuring that the right tool is used at the right time without manual intervention.
Material Compatibility and Adaptation
The ability of milling machines to handle various materials also contributes to their precision. By adjusting cutting parameters such as speed and feed rate according to the material’s hardness, machines can maintain high accuracy across different materials. For example, machining high-hardness steel requires lower speeds and appropriate cutting tools to prevent inaccuracies due to material resistance.
Moreover, flexibility in machining tasks2 allows for rapid adjustments during production. If a design modification is needed, adjustments can be made quickly through CNC programming or manual calibration, ensuring that precision is never compromised.
Conclusion: A Crucial Tool for Precision Engineering
Understanding how milling machines achieve high precision is crucial for sectors that rely on meticulous standards. From structural designs that support accurate movement to cutting-edge CNC technology that eliminates human error, these machines are indispensable in precision engineering.
CNC milling machines use ATC systems for precision.True
Automatic Tool Changing (ATC) systems ensure precise tool usage, reducing errors.
Milling machines can't handle high-hardness steel accurately.False
By adjusting speed and tools, they maintain accuracy even with hard materials.
What Makes Milling Machines Versatile in Operations?
Milling machines, known for their versatility, can perform a variety of machining tasks that enhance manufacturing efficiency and flexibility.
Milling machines are versatile due to their ability to execute diverse machining operations like cutting, threading, and drilling. This versatility stems from their adaptability to different tasks and materials, making them essential in various industrial applications.
Diverse Machining Capabilities
Milling machines stand out in the machining world for their ability to perform a wide range of operations. These include slot cutting, threading, rabbeting, routing, planning, and drilling. This breadth of capabilities allows them to create complex parts and shapes in a single setup, significantly enhancing productivity.
For example, when manufacturing an automotive component that requires precise cuts and drilled holes, a milling machine can seamlessly transition between these tasks without needing to switch equipment.
Adaptability to Various Materials
One of the key factors contributing to the versatility of milling machines is their ability to handle a broad spectrum of materials. Whether it’s metals like steel and aluminum or non-metals such as plastics and wood, milling machines can adjust cutting parameters to optimize the process for different material properties.
For instance, by modifying cutting speeds and feed rates, machinists can efficiently work on softer materials like aluminum without compromising the tool’s lifespan or the product’s quality.
Integration of Multiple Functions
Milling machines often integrate multiple machining functions into a single setup. Besides milling various shapes, they can also perform drilling, reaming, boring, and tapping operations. This integration reduces the need for transferring workpieces between different machines, saving both time and resources.
A practical example is in the production of mechanical parts where milling the outer shape is followed by drilling and tapping on the same machine, streamlining the entire process.
Flexibility in Production
Milling machines cater to both single-piece and mass production environments. In single-piece production, machinists can quickly alter machining parameters to accommodate different designs. For mass production, CNC programming enables consistent quality across large batches with minimal human intervention.
In mold manufacturing, for example, milling machines adapt to produce various mold designs efficiently through flexible programming options.
Automated Operations
Modern CNC milling machines can achieve high levels of automation through the use of Computer-Aided Manufacturing (CAM) software and Automatic Tool-Changing (ATC) systems. This automation ensures precise execution of complex tasks with reduced human error and increased efficiency.
By automating tool changes during operations, milling machines not only save time but also maintain consistent precision across all machining tasks.
Understanding these aspects of versatility in milling machines can significantly enhance decision-making regarding their application in manufacturing. This adaptability makes them indispensable in industries like aerospace, automotive, and electronics, where precision and efficiency are paramount.
Milling machines can perform threading operations.True
Threading is a machining operation that milling machines can execute.
Milling machines cannot handle non-metal materials.False
Milling machines can work with metals and non-metals like plastics.
Why Are CNC Milling Machines More Efficient?
CNC milling machines redefine efficiency in manufacturing, combining speed, precision, and automation for unparalleled productivity.
CNC milling machines boost efficiency through automation, multitasking capabilities, and high precision. They reduce setup times and enhance production rates by executing complex tasks in a single setup, minimizing errors and optimizing the use of resources.
Automation and Precision
CNC milling machines excel in automation3 and precision. Their computer-controlled operations allow for minimal human intervention, ensuring consistent quality and repeatability in large production runs. Precision is achieved through advanced software that precisely dictates the tool’s path, eliminating human errors and ensuring each part meets exact specifications. This precision is crucial for industries where high accuracy is paramount, such as aerospace and medical devices.
Multitasking and Flexibility
One of the standout features of CNC milling machines is their ability to perform multiple operations without the need to switch setups. For instance, a machine equipped with a rotating tool carousel can automatically switch between different tools, allowing for milling, drilling, and tapping to be completed in a single operation. This capability reduces production time significantly. Additionally, the flexibility to adapt to various tasks makes these machines ideal for both small-batch and mass production. They can quickly adjust to different sizes and shapes of parts by modifying CNC programs.
Speed and Reduced Downtime
CNC milling machines are designed to operate at high speeds with minimal downtime. They can complete complex parts in a fraction of the time required by conventional methods. This speed is partly due to their ability to execute multiple processes in one setup and partly because of their optimized tool paths that reduce non-productive movements. The use of automatic tool changers further enhances efficiency by minimizing manual intervention, allowing operators to focus on other tasks while the machine runs.
Resource Optimization
By integrating various machining processes, CNC milling machines optimize the use of materials and tools. For example, they can achieve the desired surface finish during the initial machining process, reducing the need for additional finishing steps. This not only saves time but also conserves materials, reducing waste and lowering overall production costs. Furthermore, the ability to work with diverse materials like metals and plastics enhances their versatility across different industries.
In summary, CNC milling machines bring together automation, multitasking abilities, high speed, and resource optimization to enhance manufacturing efficiency dramatically.
CNC machines reduce setup times significantly.True
They perform multiple tasks in a single setup, minimizing errors.
Manual intervention is frequent in CNC milling.False
CNC milling relies on automation, reducing the need for human input.
How Does Material Compatibility Impact Milling Performance?
Material compatibility is crucial in milling, influencing efficiency, precision, and tool longevity. Let’s explore how choosing the right materials can transform milling outcomes.
Material compatibility significantly impacts milling performance by influencing tool wear, surface finish, and machining efficiency. Selecting suitable materials enhances production quality and tool lifespan while reducing costs.
Understanding Material Properties
The performance of milling operations heavily relies on the properties of the materials being machined. Hardness, thermal conductivity, and tensile strength are key factors that affect tool wear and machining efficiency. For instance, materials with high hardness, such as titanium alloys, require specific cutting tools and parameters to achieve optimal results without excessive wear.
Tool Wear and Material Interaction
When milling different materials, the interaction between the cutting tool and the workpiece is vital. Harder materials tend to accelerate tool wear, reducing tool life. This necessitates using appropriate coatings4 or material-specific cutting tools to enhance durability. Carbide tools with diamond coatings are often preferred for hard metals due to their resistance to wear.
Surface Finish Quality
The choice of material influences the surface finish quality of the machined part. Softer materials like plastics often result in smoother finishes but can lead to issues like melting if not machined with the right parameters. Conversely, metals may require multiple passes to achieve a desired finish. Understanding these nuances helps in selecting the right material for a given application.
Material Type | Common Issues | Recommended Solutions |
---|---|---|
Metals | Tool wear | Use coated carbide tools |
Plastics | Melting and deformation | Reduce cutting speed |
Composites | Delamination | Optimize feed rates |
Machining Efficiency
Material compatibility also affects machining efficiency. Metals typically require slower feed rates and higher spindle speeds compared to softer materials like plastics or wood. By tailoring these parameters according to material properties, manufacturers can improve efficiency and reduce production time.
Cost Considerations
Using incompatible materials can lead to increased tool wear and machining errors, driving up costs due to frequent tool replacements and rework. Proper material selection ensures cost-effectiveness by minimizing waste and optimizing tool usage.
By focusing on material compatibility, manufacturers can achieve superior milling performance that enhances quality while controlling costs effectively.
Material compatibility affects tool wear in milling.True
Choosing compatible materials reduces tool wear, enhancing lifespan.
Softer materials always result in rougher surface finishes.False
Softer materials can produce smoother finishes if machined correctly.
Conclusion
Milling machines are not just tools; they are game-changers in precision and efficiency. Embrace their advantages to elevate your manufacturing processes.
-
Discover how CAM software ensures precise CNC milling operations.: CAM software generates toolpaths and machining instructions based on the CAD model, optimizing tool movements, speeds, and feeds to achieve the desired … ↩
-
Learn how flexibility aids in maintaining precision in various tasks.: Vertical milling machines allow for greater project flexibility and diversity—users can work with a wider variety of shape and size … ↩
-
Discover how automation improves consistency and quality in CNC milling.: Automation is seeing widespread use in CNC machining, as it makes facilities exceptionally productive, cost-effective, safer, and more adaptable. ↩
-
Discover suitable coatings to improve tool durability and performance.: Two methods are essentially used for coating: PVD coating and CVD coating. We shall explain the differences and help you choose the right coating. ↩