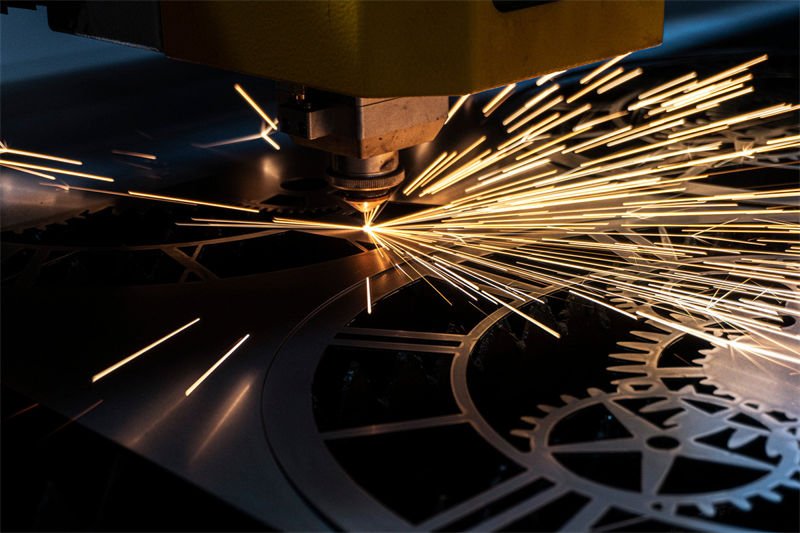
Have you ever marveled at how precisely a fiber laser cutting machine slices through metal? It’s truly fascinating!
A fiber laser cutting machine uses a high-powered laser beam generated through optical fibers to cut materials with precision. The laser is focused onto the material’s surface, melting or vaporizing it, while high-pressure gases blow away any molten or vaporized material, resulting in a clean cut.
But that’s just the tip of the iceberg! To truly harness the power of fiber lasers, let’s explore their inner workings, troubleshoot common challenges, and discover how to optimize them for your unique needs.
Fiber lasers use a solid-state laser source.True
Fiber lasers utilize optical fibers doped with rare earth elements.
What Are the Key Components of a Fiber Laser Cutting Machine?
Fiber laser cutting machines have distinct components that enable precise and efficient material processing.
Key components of a fiber laser cutting machine include the laser source, cutting head, CNC controller, cooling system, and assist gas system. Each part plays a crucial role in ensuring precision, speed, and quality of cuts.

The Laser Source
The heart of a fiber laser cutting machine is its laser source, which generates the high-powered laser beam necessary for cutting. This component determines the machine’s capability in terms of power and efficiency. Fiber lasers are known for their superior energy efficiency and long lifespan compared to other laser types.
The Cutting Head
The cutting head is where the laser beam is focused onto the material. It includes lenses and nozzles that help in directing the beam precisely. The nozzle size can greatly influence the quality of the cut. For instance, a smaller nozzle often results in smoother cuts when dealing with sharp angles1.
CNC Controller
A CNC (Computer Numerical Control) controller manages the cutting process by directing the movement of the cutting head based on programmed instructions. It ensures accurate and repeatable cuts and enables complex designs to be executed with ease.
Cooling System
Laser cutting generates significant heat, which requires an efficient cooling system to prevent overheating and maintain operational stability. Typically, water chillers are used to cool the laser source and other components.
Assist Gas System
Assist gases like nitrogen, oxygen, or air are used in fiber laser cutting to enhance the cutting process. They help remove molten material from the cut area and can influence cut quality and speed. For example, nitrogen is often used to achieve oxide-free edges when cutting stainless steel.
Table: Key Components Overview
Component | Function |
---|---|
Laser Source | Generates high-powered laser beam |
Cutting Head | Focuses laser onto material |
CNC Controller | Manages movement and operation |
Cooling System | Prevents overheating and maintains stability |
Assist Gas System | Enhances cut quality and speed through gas application |
Understanding these components provides insights into how adjustments in settings can optimize performance. For instance, changes in nozzle aperture or adjustments in gas pressure can mitigate issues like dross on cut surfaces2.
Fiber lasers have superior energy efficiency.True
Fiber lasers use less energy compared to other types, enhancing efficiency.
Assist gases are unnecessary in laser cutting.False
Assist gases improve cut quality and speed by removing molten material.
How Do Fiber Lasers Differ from CO2 Lasers in Cutting?
Fiber and CO2 lasers are both powerful tools in industrial cutting, but how do they differ?
Fiber lasers and CO₂ lasers have many differences in cutting. Fiber lasers are pumped by diodes, with a wavelength of around 1 μm. They are excellent for cutting metals, fast, and have high precision. The equipment is expensive but has low maintenance costs and is small and highly flexible. CO₂ lasers generate lasers by exciting carbon dioxide gas, with a wavelength of 10.6 μm. They have wide material adaptability. The equipment is cheap but has high maintenance costs.

Understanding the Basics
To fully appreciate the differences between fiber and CO2 lasers, one must first understand how each type operates. Fiber lasers utilize a solid-state setup where the laser beam is generated through optical fibers doped with rare earth elements like erbium or ytterbium. This configuration allows for high efficiency and precision.
CO2 lasers, on the other hand, use a gas mixture of carbon dioxide, nitrogen, and helium as the lasing medium. The beam is generated by exciting these gases with electrical energy, making CO2 lasers suitable for cutting thicker materials due to their longer wavelength.
Efficiency and Precision
Fiber Lasers:
- Higher Efficiency: Fiber lasers generally convert electrical energy into light more efficiently than CO2 lasers.
- Precision: They produce a smaller beam diameter leading to more precise cuts, especially beneficial for intricate designs.
CO2 Lasers:
- Efficiency Challenges: While effective for certain tasks, they typically require more power, leading to higher operational costs.
- Thicker Material Cutting: Their longer wavelength allows them to cut through thicker materials effectively.
Versatility and Maintenance
Fiber lasers boast versatility in cutting various metals, including reflective ones like aluminum and copper, which often pose challenges for CO2 lasers due to reflection-induced damage.
Maintenance Aspects:
- Fiber Lasers: Minimal maintenance as they lack moving parts and mirrors within the laser cavity.
- CO2 Lasers: Require regular maintenance due to the complexity of their optical setup involving mirrors and lenses.
Cost Considerations
While fiber lasers might have a higher initial purchase cost, their operational savings over time—thanks to lower maintenance and energy costs—often make them more economical in the long run.
Feature | Fiber Lasers | CO2 Lasers |
---|---|---|
Initial Cost | Higher | Lower |
Operational Cost | Lower | Higher |
Efficiency | High | Moderate |
Precision | High | Moderate |
Maintenance | Low | High |
Material Versatility | High | Moderate |
Understanding these differences is crucial for industries aiming to select the right laser for their specific cutting needs. By evaluating aspects like efficiency3, maintenance requirements, and material compatibility, businesses can make informed decisions that enhance their operational capabilities.
Fiber lasers are more efficient than CO2 lasers.True
Fiber lasers convert electrical energy into light more efficiently.
CO2 lasers require less maintenance than fiber lasers.False
CO2 lasers need regular maintenance due to their complex optical setup.
What Are Common Problems in Fiber Laser Cutting and How to Solve Them?
Fiber laser cutting machines are efficient and precise, but users often encounter specific issues during operation.
Common problems in fiber laser cutting include poor cutting quality (such as rough surface and burrs), insufficient precision (deviation in size and perpendicularity), slag on materials, and equipment malfunctions (power drop and alarms). Solutions include reasonably adjusting parameters, correct programming, maintaining mechanical parts, ensuring normal auxiliary gas, and maintaining equipment components.
Understanding Layering Issues
Layering in the cut section can often disrupt the smoothness of a cut. This issue may arise due to inappropriate speed settings or gas pressure.
- Solution 1: Modify the cutting speed4 to ensure it aligns with the material type and thickness.
- Solution 2: Adjust the cutting gas pressure to maintain consistency in the cut quality.
- Solution 3: Consider changing the nozzle aperture or altering the negative defocus amount to achieve a sharper cut.
Managing Dross Accumulation
Dross, or unwanted material buildup, can be a persistent challenge. It occurs when melted material is not completely ejected from the cut area.
- Solution 1: Similar to layering, adjusting the cutting speed and gas pressure can be effective.
- Solution 2: Change the negative defocus amount to better focus the laser beam.
- Solution 3: Tweak the nozzle spacing to enhance material ejection.
Addressing Slow Cutting Speeds
Sluggish performance can severely impact productivity. Several factors could contribute to a reduced cutting speed:
Issue | Solution |
---|---|
Dirty optical lenses | Regularly clean lenses to maintain efficiency. |
Inappropriate gas pressure | Adjust the pressure to suit the material type. |
Incorrect defocus amount | Re-evaluate and modify as necessary. |
Power issues | Ensure laser power is at optimal levels. |
Preventing Nozzle Overheating
Nozzle overheating not only affects cutting quality but also can lead to equipment damage.
- Solution 1: Use a larger aperture nozzle to manage heat better.
- Solution 2: Check for contamination on protective lenses, which can exacerbate heat issues.
- Solution 3: Adjust focus settings while ensuring cutting precision is maintained.
Tackling Piercing Bursts
Piercing bursts can cause inconsistency in cuts, especially when dealing with thick materials.
- Solution 1: Reduce the piercing frequency and duty cycle.
- Solution 2: Adjust the piercing height and gas pressure for better control.
- Solution 3: Increase waiting time for blowing in multi-stage piercing to stabilize operations.
Ensuring a Smooth Cut Surface
A rough cut surface can result from improper settings or equipment wear and tear.
- Solution 1: Increase positive defocus slightly to enhance beam stability.
- Solution 2: Replace with a double-layer nozzle for a more consistent cut or use a smaller aperture single nozzle.
By understanding these common problems and applying tailored solutions, operators can significantly enhance their fiber laser cutting5 processes.
Layering issues in fiber laser cutting are caused by high gas pressure.False
Layering is often due to inappropriate speed settings or low gas pressure.
Dross accumulation is reduced by adjusting nozzle spacing.True
Tweaking nozzle spacing enhances material ejection, reducing dross.
How Can You Optimize Fiber Laser Cutting for Different Materials?
Optimizing fiber laser cutting for various materials requires understanding their unique properties and adjusting settings accordingly.
To optimize fiber laser cutting of different materials, parameters need to be adjusted. For metal materials, carbon steel uses oxygen as an assistant and adjusts power and speed according to thickness. Stainless steel uses nitrogen to prevent oxidation. Aluminum alloy uses argon gas and high-power cutting. In non-metallic materials, acrylic uses compressed air. For wood, prevent carbonization. For ceramics, cooling assistance is used. At the same time, pay attention to other settings.
Understanding Material Properties
Different materials react differently to laser cutting due to their unique thermal and physical properties. Metals like stainless steel, aluminum, and copper each require tailored approaches. Understanding these properties is crucial to optimizing the cutting process:
- Stainless Steel: Known for its strength and corrosion resistance, stainless steel benefits from a precise focus and higher power settings to ensure clean cuts.
- Aluminum: Reflectivity can be a challenge. Using appropriate coatings or anti-reflective lenses can help mitigate this issue.
- Copper: Highly reflective and thermally conductive, copper requires lower power settings and specialized nozzles to prevent damage.
Fine-Tuning Laser Parameters
Adjusting laser parameters is essential to achieving optimal results. Here’s how you can tweak the settings:
- Power and Speed: Higher power can increase speed but may cause burning. It’s important to find a balance.
- Focus Position: Adjusting the focus ensures that the laser beam concentrates precisely where needed.
- Gas Pressure: Different materials require varying gas pressures to aid in expelling molten material efficiently.
Material | Power Setting | Cutting Speed | Gas Type |
---|---|---|---|
Stainless Steel | High | Moderate | Oxygen |
Aluminum | Medium | Fast | Nitrogen |
Copper | Low | Slow | Nitrogen |
Addressing Common Cutting Issues
Certain issues are frequently encountered when cutting different materials with a fiber laser. Here’s how to address them:
- Layering in the Cut Section: Alter the cutting speed6 or adjust the gas pressure.
- Dross Formation: Modify the nozzle aperture or change the negative defocus amount.
- Nozzle Overheating: Consider using a larger aperture nozzle and check for contamination.
Practical Tips for Diverse Materials
When working with diverse materials, adopting specific strategies can enhance performance:
- Regular Maintenance: Ensure that optical lenses are clean and free of debris.
- Experimentation: Run test cuts on new materials to determine the best settings.
- Technology Upgrades: Invest in software or hardware upgrades that allow for more precise control over cutting parameters.
By understanding material properties and fine-tuning your machine’s parameters, you can significantly enhance the efficiency and quality of your laser cutting processes.
Stainless steel requires high power settings for clean cuts.True
High power ensures the laser cuts through stainless steel efficiently.
Copper needs high power and fast cutting speed settings.False
Copper requires lower power and slower speed due to reflectivity.
Conclusion
By mastering fiber laser cutting techniques and understanding common challenges, I can enhance my metalworking projects significantly. Let’s keep learning!
-
Explore how nozzle size affects cut quality for sharp angles.: The diameter of the copper nozzle is φ1.5mm, which is more suitable for the plate below 3mm, and the cutting surface is thinner. If you use a …
-
Discover tips to minimize dross on fiber laser cut surfaces.: Eliminating interaction with air is the simplest method available for preventing dross. You could use the nitrogen approach, but it may be a bit …
-
Explore detailed comparisons of laser efficiencies.: In terms of operational power use, CO2 lasers are around 5 to 10% efficient — meaning they draw 10 to 20 times as much electricity as they emit …
-
Learn how to correctly set cutting speeds for various materials.: The cutting speed, typically measured in meters per minute (m/min), should be adjusted according to the material’s thickness and the desired …
-
Discover techniques to boost fiber laser cutting efficiency.: In this article, we explore five key areas that can significantly improve laser cutting: material quality, programming/nesting, power, assist/cutting gases, …
-
Learn how adjusting speed affects cut quality and efficiency.: The cutting speed, typically measured in meters per minute (m/min), should be adjusted according to the material’s thickness and the desired …