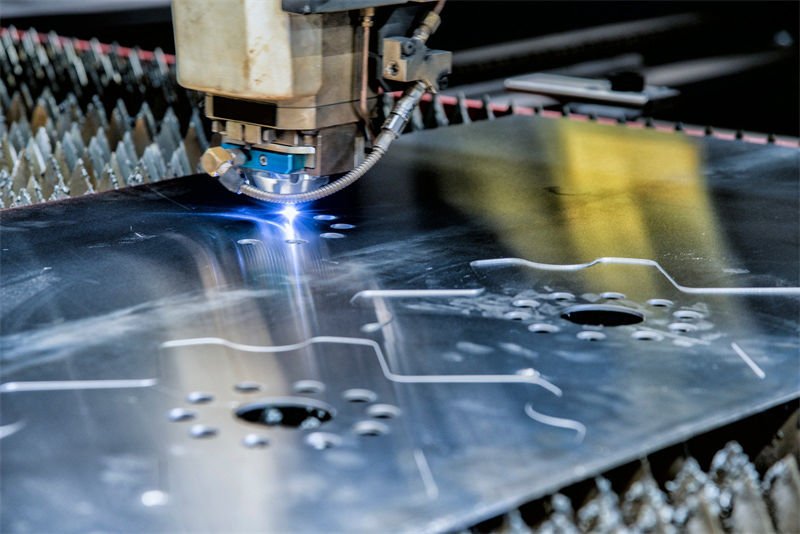
Aluminium’s allure in manufacturing is undeniable, but cutting it isn’t as straightforward as it may seem.
Laser cutting of aluminum has a good effect. It has high cutting quality with smooth edges and no burrs. The precision can reach below 0.1mm. The cutting speed is fast. For example, the speed of cutting 1mm thick aluminum alloy plate can reach about 40m/min, which can improve efficiency. Moreover, the heat affected zone is small. It is non-contact processing, which can reduce heat damage and avoid material deformation and discoloration.
But there’s so much more to it than just basic settings. Let’s dive into the intricacies of laser cutting aluminium and how you can master this challenging material.
Aluminium's high reflectivity complicates laser cutting.True
Aluminium reflects laser beams, requiring careful adjustment of power and focus.
What Makes Aluminium Challenging for Laser Cutting?
Aluminium’s high reflectivity presents unique challenges in laser cutting, necessitating precise equipment and settings.
Aluminum poses challenges for laser cutting mainly due to its high reflectivity. Most laser energy is reflected, reducing cutting efficiency. At the same time, aluminum has good thermal conductivity. Heat easily spreads, making it difficult to reach the high temperature required for cutting and it is prone to deformation. Moreover, oxidation easily occurs during cutting. The oxide layer will change the interaction process between laser and material, affecting cutting quality.
High Reflectivity Challenges
One of the most significant challenges when laser cutting aluminium is its high reflectivity. This property can cause the laser beam to reflect off the surface, leading to potential damage to the laser machine itself. To mitigate this, advanced lasers equipped with specialized optics are necessary. Moreover, adjusting parameters such as laser power and speed is essential to effectively manage reflections1.
Thermal Conductivity
Aluminium’s excellent thermal conductivity means that heat dissipates quickly across the material. While this characteristic is beneficial in many applications, it complicates the laser cutting process. The rapid heat dissipation requires a higher power input to maintain a precise cut. Additionally, consistent monitoring and adjustments are needed to ensure the cut remains clean and accurate.
Back Reflections and Equipment Safety
Another issue with cutting aluminium is the risk of back reflections. This occurs when the laser reflects back into the cutting machine, which can damage the equipment or reduce cutting efficiency. Using protective measures, such as beam absorbers or deflectors, and choosing appropriate lasers designed to handle such materials can prevent these issues.
Table: Example Settings for 3.5mm Aluminium Plate
Parameter | Setting |
---|---|
Duty Cycle | 65% |
Focus Position | 3mm from surface |
Pulse Frequency | 5000Hz |
Cutting Speed | 0.7-0.8m/min |
These settings are tailored to a specific scenario, demonstrating how precise control over various factors can result in effective laser cutting of aluminium.
Material Variability and Layering
Aluminium alloys vary in composition, which can affect how they respond to laser cutting. Understanding these differences is crucial for achieving optimal results. When layering occurs during cutting, it may be necessary to adjust duty cycles and pulse frequencies gradually to improve cut quality. Practical experimentation and observation are key in fine-tuning these settings.
Aluminium's high reflectivity damages laser machines.True
High reflectivity can cause laser beams to reflect back, risking damage.
Thermal conductivity simplifies aluminium laser cutting.False
High thermal conductivity dissipates heat quickly, complicating cutting.
Which Lasers Are Best Suited for Cutting Aluminium?
Choosing the right laser for cutting aluminium is essential due to its high reflectivity and thermal conductivity. Which types are most effective?
Fiber lasers and carbon dioxide lasers are relatively suitable for cutting aluminum. Fiber lasers have good beam quality and high energy density and can effectively cut aluminum. Moreover, their photoelectric conversion efficiency is high, and the power can be flexibly adjusted. The wavelength of carbon dioxide lasers is suitable for aluminum absorption and can generate enough heat to achieve cutting, and the cutting quality is also relatively ideal.
Understanding Laser Types for Aluminium Cutting
When it comes to cutting aluminium, two primary types of lasers stand out: fiber lasers2 and CO2 lasers. Each has distinct advantages and potential drawbacks, making it crucial to choose based on specific project requirements.
Fiber Lasers
Fiber lasers are widely recommended for cutting aluminium due to their high efficiency and precision. Their shorter wavelength (usually around 1µm) allows for better absorption by the aluminium, minimizing reflection issues. This results in:
- Higher Cutting Speeds: Fiber lasers can cut through aluminium more quickly than many other laser types.
- Improved Edge Quality: The precise focus of the laser beam leads to cleaner cuts.
- Reduced Power Consumption: They tend to use less power compared to CO2 lasers.
However, fiber lasers may require additional components to manage heat dissipation due to the high energy concentration.
CO2 Lasers
CO2 lasers operate at a wavelength of 10.6µm, making them less efficient with reflective metals like aluminium compared to fiber lasers. Yet, they remain a viable option under the right conditions:
- Thicker Materials: CO2 lasers can handle thicker aluminium sheets with proper settings.
- Cost-Effectiveness: For certain applications, they may be more cost-effective due to their lower initial investment.
- Versatility: They can cut a wide variety of materials, not just metals.
To effectively cut aluminium, CO2 lasers often require adjustments in power and gas flow, as well as enhanced safety measures to mitigate reflection-related risks.
Key Considerations for Choosing a Laser
Several factors influence the decision between fiber and CO2 lasers:
Factor | Fiber Laser | CO2 Laser |
---|---|---|
Cutting Speed | Faster | Moderate |
Reflectivity Handling | Better absorption | Requires adjustments |
Material Thickness | Ideal for thin to moderate | Suitable for thicker sheets |
Operational Costs | Lower power consumption | Potentially higher |
The choice ultimately depends on specific requirements such as thickness of the material, budget constraints, and desired speed and quality of cutting. Evaluating these criteria will help you select the most suitable laser system for your needs.
Fiber lasers are more efficient for aluminium cutting.True
Fiber lasers have a shorter wavelength, improving absorption and efficiency.
CO2 lasers are unsuitable for cutting thick aluminium sheets.False
CO2 lasers can handle thicker aluminium with proper settings.
How Do Laser Power and Speed Affect Cutting Quality?
Understanding how laser power and speed impact cutting quality is crucial for precision in manufacturing.
The laser power and speed significantly affect cutting quality. High power makes materials easier to melt and vaporize, but excessive power leads to a large heat-affected zone and rough cutting edges. Fast cutting speed can improve efficiency, but too fast will result in incomplete cutting. Only a proper combination of power and speed can ensure a smooth cutting surface and high precision.
The Role of Laser Power in Cutting Quality
Laser power determines the amount of energy delivered to the material, influencing how effectively it can be cut. Higher power settings generally enable cutting through thicker materials, but excessive power can lead to undesirable effects3 such as burning or melting, especially with reflective materials like aluminum. It’s important to calibrate the laser power according to the material thickness and type.
For instance, cutting a 3.5mm aluminum plate typically requires a power setting that balances energy input to avoid damaging the material while ensuring a smooth edge.
Impact of Cutting Speed on Results
Cutting speed refers to how quickly the laser moves across the material surface. Fast speeds may lead to incomplete cuts or rough edges, while slow speeds can cause overheating and material deformation. Finding the optimal cutting speed is crucial for achieving a clean cut without compromising the material’s structural integrity.
Here’s a quick reference table:
Material Thickness | Recommended Speed (m/min) |
---|---|
1mm | 1.5 – 2.0 |
3.5mm | 0.7 – 0.8 |
5mm | 0.5 – 0.6 |
Balancing Laser Power and Speed
The key to high-quality laser cutting lies in balancing power and speed. As a rule of thumb, increasing the laser power often requires an adjustment in speed to maintain quality. Adjustments should be made gradually, testing small sections to evaluate results before finalizing settings.
For example, when dealing with a highly reflective material4 like aluminum, a careful balance ensures that the laser does not bounce off and damage the equipment.
Practical Tips for Precision Cutting
- Test Runs: Conduct test cuts on scrap material to fine-tune settings.
- Monitoring: Continuously monitor the cutting process to make on-the-fly adjustments.
- Equipment Calibration: Regularly calibrate your machine to ensure consistency in power delivery and speed.
By understanding and implementing these factors, manufacturers can significantly enhance the quality of their laser-cut products.
Higher laser power enables cutting thicker materials.True
Higher power settings deliver more energy, allowing cuts through thicker materials.
Slow cutting speeds ensure better edge smoothness.False
Slow speeds can cause overheating and material deformation, affecting smoothness.
What Are Common Mistakes and How Can They Be Avoided?
Precision in laser cutting aluminium requires attention to detail. Discover the pitfalls and learn how to navigate them effectively.
Common errors include rough cutting surface and material deformation. Rough cutting surface may be due to inappropriate laser power or excessive cutting speed. Material deformation is caused by thermal influence. Aluminum material has fast heat conduction and is prone to thermal deformation. To avoid these errors, power and speed should be precisely adjusted, and the use of auxiliary gas should be considered to reduce thermal influence.
Misjudging Laser Power and Speed
The first mistake often occurs in setting inappropriate laser power and speed5. A higher power setting may seem effective for cutting through tough materials, but with aluminium, it can lead to excessive reflection and potential machine damage. Similarly, incorrect speed can result in burn marks or incomplete cuts.
Solution: Understand your machine’s specifications. Start with recommended settings and make small adjustments based on trial cuts. For a 3.5mm aluminium plate, consider starting with a duty cycle of 65% and a cutting speed of 0.7-0.8m/min.
Inaccurate Focus Adjustment
Another common issue is imprecise focus adjustment6. If the laser beam isn’t accurately focused on the material’s surface, it can cause melting instead of clean cutting.
Solution: Use positive focal positioning to ensure that the beam is concentrated exactly where needed. Regularly calibrate your laser cutter and perform test cuts to verify focus accuracy.
Neglecting Pulse Frequency and Duty Cycle Settings
Ignoring the right pulse frequency and duty cycle can disrupt the cutting process, especially for reflective materials like aluminium.
Parameter | Suggested Setting |
---|---|
Pulse Frequency | 5000Hz |
Duty Cycle | 65% |
Solution: Adjust these settings based on the thickness and reflectivity of the material. Monitor the cut for signs of overheating or incomplete penetration.
Overlooking Section Layering
Failing to manage section layering can result in uneven cuts and additional material waste.
Solution: Adjust pulse frequency and duty cycle gradually. Observe the cut closely to determine if further tweaks are necessary for cleaner results. Regular maintenance checks on your machine will also ensure optimal performance.
By avoiding these common mistakes through careful preparation and ongoing observation, you can enhance the effectiveness of your laser cutting process with aluminium.
Incorrect laser settings can damage the machine.True
Improper laser power and speed can cause reflections, damaging equipment.
Ignoring section layering leads to cleaner cuts.False
Neglecting section layering results in uneven cuts and material waste.
Conclusion
Mastering the art of laser cutting aluminium requires understanding its unique properties and mastering specific techniques. With careful adjustments, you can achieve precise results and elevate your fabrication game.
-
Discover strategies for handling reflections during aluminium laser cutting.: Basically, you need enough power to cut quickly before the (high) thermal conductivity of the metal heats up with work piece and causes …
-
Discover why fiber lasers excel at cutting reflective materials like aluminium.: Fast cutting speeds: The high power density and excellent beam quality of fiber lasers enable faster cutting speeds compared to other laser …
-
Explore how excessive laser power affects cutting outcomes.: For the majority of applications, increasing the power puts less heat into the material due to the increased cutting speed, which improves the edge sharpness.
-
Learn techniques for managing reflective materials during laser cutting.: Laser cutting machines are uniquely suited to handle highly reflective metals such as brass, aluminum, and silver with precision and efficiency.
-
Learn optimal laser settings for efficient aluminium cutting.: The first step is to program the laser cutting machine with specialized software. At this stage, experts set the cutting parameters, ensuring …
-
Master focus techniques for precise metal cutting.: How to set you laser cutter for optimum focus. Demonstration of different focal lengths.