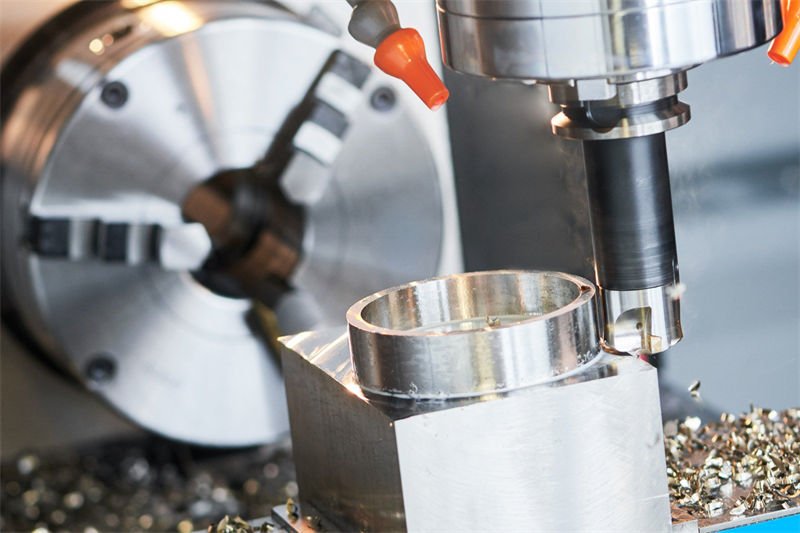
Have you ever wondered just how precise a milling machine can be? In precision manufacturing, accuracy is everything, and milling machines are at the heart of that process.
Milling machines vary in accuracy based on their type and application. High-precision machines achieve micron-level accuracy, while ordinary ones offer less. Understanding their precision helps inform manufacturing decisions.
Now that you have a glimpse into the world of milling machine accuracy, let’s dive deeper into the specifics. We’ll explore the types of machines, the factors influencing their precision, and how you can enhance your manufacturing processes.
CNC milling machines achieve higher precision than manual ones.True
CNC machines use automated controls, ensuring micron-level accuracy.
What Are the Differences in Precision Between CNC and Manual Milling Machines?
Milling machines are integral to precision manufacturing, but how do CNC and manual versions compare in accuracy?
CNC milling machines offer superior precision compared to manual ones due to automated controls. While CNC machines can achieve micron-level accuracy, manual machines depend on operator skill, leading to more variability. Choosing between them involves weighing precision needs against cost and complexity.
Positioning Precision
CNC milling machines boast exceptional positioning precision due to their automated control systems. These systems use digital signals to accurately position the cutting tool, minimizing human error. For instance, advanced CNC machines can achieve positional accuracy of up to 0.01 mm, a feat unattainable by manual machines that rely on operator skill and mechanical adjustments. This precise control allows CNC machines to excel in applications demanding high accuracy, such as aerospace or medical device manufacturing.
In contrast, manual milling machines often require operators to manually position the workpiece and tool, which introduces variability in precision. The reliance on human input means that even slight deviations in hand movements can lead to errors, resulting in less consistent outcomes.
Repeatability and Consistency
Repeatability is a crucial aspect of precision manufacturing, and CNC machines shine in this area. Once programmed, CNC machines can replicate complex parts with unparalleled consistency. For example, in a production run of thousands of components, a CNC machine will maintain the same level of accuracy from the first piece to the last.
Manual milling machines, however, are subject to the operator’s skill level and physical condition. Repeated tasks can introduce fatigue, leading to decreased precision over time. This inconsistency makes manual machines less suitable for large-scale production where uniformity is key.
Complexity of Machined Parts
CNC milling machines are capable of machining complex geometries with high precision. They can perform intricate cuts and shapes that would be challenging or impossible on a manual machine. This is due to their ability to follow precise programmed instructions and make intricate tool paths without human intervention.
Manual machines are limited by the operator’s ability to manipulate the machine’s controls. Complex shapes often require multiple setups and adjustments, increasing the potential for errors and reducing overall precision.
Impact of Human Factors
The proficiency of an operator significantly impacts the precision of manual milling. A highly skilled machinist can achieve impressive results; however, this level of skill takes years to develop. On the other hand, CNC machines reduce dependency on human factors by automating processes, enabling less experienced operators to produce high-quality parts consistently.
Cost Considerations
While CNC machines offer superior precision, they come at a higher initial cost compared to manual milling machines. The investment in CNC technology includes not only the machine itself but also software and training. Therefore, businesses must evaluate whether the increased precision justifies the additional expense based on their specific manufacturing needs.
Overall, understanding the differences between CNC and manual milling1 helps manufacturers choose the right machine type based on desired precision levels and production volumes.
CNC machines achieve 0.01 mm precision.True
CNC machines use digital signals for precise tool positioning.
Manual milling is more precise than CNC.False
Manual milling relies on operator skill, leading to variability.
How Do Material Characteristics Affect Milling Precision?
Material characteristics significantly influence the precision of milling processes. Various factors such as hardness, thermal properties, and material composition play crucial roles in determining the accuracy of machined parts.
Material characteristics impact milling precision through hardness, thermal expansion, and composition. Harder materials increase tool wear and machine vibration, reducing precision. Materials with high thermal expansion can deform under temperature changes, affecting dimensional accuracy.
Influence of Material Hardness
Material hardness is a primary factor affecting milling precision2. Harder materials such as steel require greater cutting forces, which can lead to faster tool wear and increased machine vibration. This results in diminished machining precision due to the excessive forces exerted during cutting. In contrast, softer materials like aluminum allow for smoother operations with less tool wear and vibration, enhancing the precision of the final product.
Thermal Expansion and Conductivity
Thermal properties of materials, including the coefficient of thermal expansion and thermal conductivity, directly influence milling precision. Materials with high thermal expansion coefficients may experience dimensional changes due to temperature fluctuations during machining, leading to inaccuracies. For instance, when machining polymers or certain alloys, maintaining a stable temperature is crucial to avoid thermal deformation. Conversely, materials with high thermal conductivity dissipate heat efficiently, reducing thermal distortion and improving precision.
Material | Thermal Expansion Coefficient (µm/m°C) | Thermal Conductivity (W/mK) |
---|---|---|
Steel | 11 | 50 |
Aluminum | 23 | 237 |
Copper | 17 | 401 |
Composition and Microstructure Effects
The composition and microstructure of a material can also influence milling precision. For example, composite materials may have varying densities and consistencies that challenge the uniformity of machining processes. Metals with inclusions or impurities can cause uneven tool wear or unexpected material behavior during cutting, impacting precision. Understanding these characteristics allows for better tool selection and machining strategies.
Examples from Industry Applications
In the aerospace industry, where precision is paramount, materials like titanium alloys are used despite their hardness due to their excellent strength-to-weight ratio. Special tooling and cutting strategies3 are necessary to maintain precision while minimizing tool wear. In contrast, in the electronics industry, materials with excellent thermal conductivity like copper are preferred for components that require precise thermal management without compromising dimensional accuracy.
Harder materials increase tool wear in milling.True
Hard materials require more force, causing faster tool wear.
Materials with low thermal expansion improve milling precision.True
Low thermal expansion reduces dimensional changes, enhancing accuracy.
What Role Does Machine Configuration Play in Achieving Precision?
Machine configuration significantly influences the precision of milling operations. But how exactly does it affect accuracy?
Machine configuration, including components like spindles, guides, and screws, directly impacts precision. High-quality configurations reduce errors and improve accuracy, crucial for complex machining tasks.
Understanding the Components of Machine Configuration
Machine configuration comprises several critical components that collectively determine the precision of milling operations. Key elements include the spindle, guides, screws, and the control system. Each component’s quality and performance significantly impact the machine’s ability to deliver high-precision results.
Spindles are vital for maintaining tool stability during operation. High-precision spindles reduce runout, ensuring consistent contact between the tool and workpiece, which is essential for achieving smooth surfaces and accurate dimensions. Similarly, guides and screws contribute to the stability and precision of linear movements along the axes.
For instance, a study comparing CNC milling machines equipped with high-end spindles and guides to those with standard components demonstrated a marked improvement in dimensional accuracy and surface finish quality.
The Impact of Hardware Quality
The quality of a milling machine’s hardware configuration is a defining factor in its precision capabilities. High-quality components are engineered to minimize vibration and thermal deformation, two primary sources of error in milling operations.
Component | Function | Impact on Precision |
---|---|---|
Spindle | Stabilizes tool rotation | Reduces runout, improves accuracy |
Guides | Directs linear movements | Minimizes friction and errors |
Screws | Facilitates precise positioning | Ensures repeatability |
Advanced CNC systems often feature enhanced control algorithms and sensors to adjust for real-time errors, further enhancing precision by dynamically compensating for minor discrepancies.
Control Systems and Their Influence
The control system plays a pivotal role in achieving precision by managing the machine’s movements and compensating for errors. Modern CNC machines use sophisticated control systems capable of real-time feedback and adjustments, allowing them to maintain high precision even under challenging conditions.
The integration of advanced feedback mechanisms, such as laser interferometers and encoders, allows these systems to detect and correct positional errors on-the-fly. This capability is particularly beneficial when machining complex geometries or operating at high speeds.
Research into control systems in CNC milling4 indicates that machines equipped with advanced controllers achieve higher accuracy compared to those with basic systems.
Configuration Customization for Specific Needs
Customization of machine configuration to meet specific manufacturing needs can also enhance precision. For instance, industries requiring ultra-precision—such as aerospace or watch manufacturing—often customize machines with components like anti-vibration mounts or thermal stabilization units.
Incorporating customized configurations5 tailored to specific material properties or operational environments can significantly boost a machine’s ability to maintain consistent precision over extended periods or varied conditions.
High-quality spindles reduce runout in milling.True
Precision spindles maintain consistent tool contact, reducing errors.
Standard components outperform high-end ones in precision.False
High-end components minimize errors, enhancing milling accuracy.
How Can Industry-Specific Needs Influence Milling Machine Selection?
Choosing the right milling machine is crucial for meeting specific industry requirements, but how do these needs shape the selection process?
Industry-specific needs dictate the choice of milling machines based on precision, material compatibility, and production volume. Aerospace demands high precision, while watchmaking requires ultra-precision for tiny components. Evaluating these needs ensures optimal machine performance.
Assessing Precision Requirements in Different Industries
Industries like aerospace6 and watch manufacturing7 demand extreme precision due to the stringent tolerances required. For instance, aerospace components often need micron-level accuracy to ensure safety and functionality, while watch parts require ultra-precision to maintain the intricate designs and mechanisms. Conversely, industries like woodworking may prioritize speed over precision.
Material Compatibility and Milling Machine Selection
Different materials require specific milling capabilities. In the mold manufacturing8 industry, for example, high-strength materials such as steel necessitate robust machines with high cutting forces and wear-resistant tools. Alternatively, softer materials like plastics or aluminum may require machines that focus on minimizing vibrations and ensuring surface finish quality.
Industry | Material Example | Machine Requirement |
---|---|---|
Aerospace | Titanium | High-precision CNC machines |
Watchmaking | Brass | Ultra-precision milling |
Mold Manufacturing | Steel | High-power milling capabilities |
Woodworking | Wood | Rapid processing speeds |
Production Volume and Machine Efficiency
The production volume is another critical factor. High-volume industries such as automotive manufacturing may need machines that offer a balance between speed and precision to meet large-scale production demands efficiently. Conversely, niche markets like custom jewelry may prioritize precision over volume, selecting machines capable of detailed work on a smaller scale.
Customization and Flexibility in Milling Machines
Industries with diverse product lines benefit from milling machines that offer customization and flexibility. For instance, industries needing frequent design changes may opt for machines with quick setup times and programmable features, ensuring swift transitions between different production runs. This adaptability is crucial for industries aiming to remain competitive in fast-paced markets.
Understanding the unique demands of your industry not only influences the type of milling machine required but also impacts long-term productivity and quality. Evaluating these needs against available technologies helps companies make informed decisions that align with their strategic goals.
Aerospace requires ultra-precision milling machines.True
Aerospace components need micron-level accuracy for safety and functionality.
Woodworking prioritizes precision over speed in milling.False
Woodworking often values rapid processing speeds more than extreme precision.
Conclusion
In conclusion, grasping the intricacies of milling machine accuracy is crucial for optimizing your manufacturing processes. Choosing the right machine and understanding the influencing factors will ensure precision and efficiency.
-
Explores detailed comparisons to aid informed decision-making.: It is absolutely more effective to program by CNC, than to manually machine something… Unless the something is so bloody simple.
-
Understanding material hardness helps optimize tool selection for better precision.: Along with increased hardness comes increased wear resistance because harder materials are more difficult to cut through. A material’s ability …
-
Discover strategies that enhance precision while machining hard materials.: The main ideas are to avoid galling, heat generation, work hardening, and workpiece or tool deflection. Use a lot of coolant at high pressure, keep speeds down …
-
Explore advancements in CNC control systems improving milling precision.: The CNC control system is in charge of managing the motion and speed of the machine tools used in everyday industrial processes.
-
Discover how custom machine setups enhance manufacturing precision.: Every CNC machine comes with WinCNC Software pre-installed. Ask about our industry-specific custom applications. SOFTWARE. Browse CNC Machines by Configuration.
-
Explore precision requirements essential for safety and performance in aerospace.: Aerospace components must ensure people’s safety while allowing high-precision equipment and machinery to function at their best.
-
Understand ultra-precision needs for small, intricate watch components.: The movement must meet strict criteria concerning its daily rate of accuracy, ranging from -4 to +6 seconds per day for mechanical watches.
-
Learn about the impact of material hardness on mold manufacturing precision.: The specific alloy selected for manufacture of a mold will have the largest impact on that mold’s performance, serviceability and life.