Have you ever wondered how 3D printers can craft such intricate designs?
3D printers create objects with interior holes by precisely following 3D models that specify these features. Technologies like FDM, SLA, and SLS each have unique methods for forming internal cavities, whether through reserved spaces or unsintered materials.
But understanding the magic behind these internal structures goes beyond just knowing the technology. Let’s dive deeper into the fascinating world of 3D printing and explore how you can optimize your designs!
FDM printers struggle with small interior holes.True
FDM's layer-by-layer process can cause irregularities in small holes.
What Role Do Different 3D Printing Technologies Play?
Explore how various 3D printing technologies contribute uniquely to creating intricate internal structures, including interior holes and cavities.
Different 3D printing technologies like FDM, SLA, and SLS play pivotal roles in forming internal holes by utilizing distinct methods. These include skipping extrusion, leaving unsolidified material, and reserving spaces to achieve desired geometries.
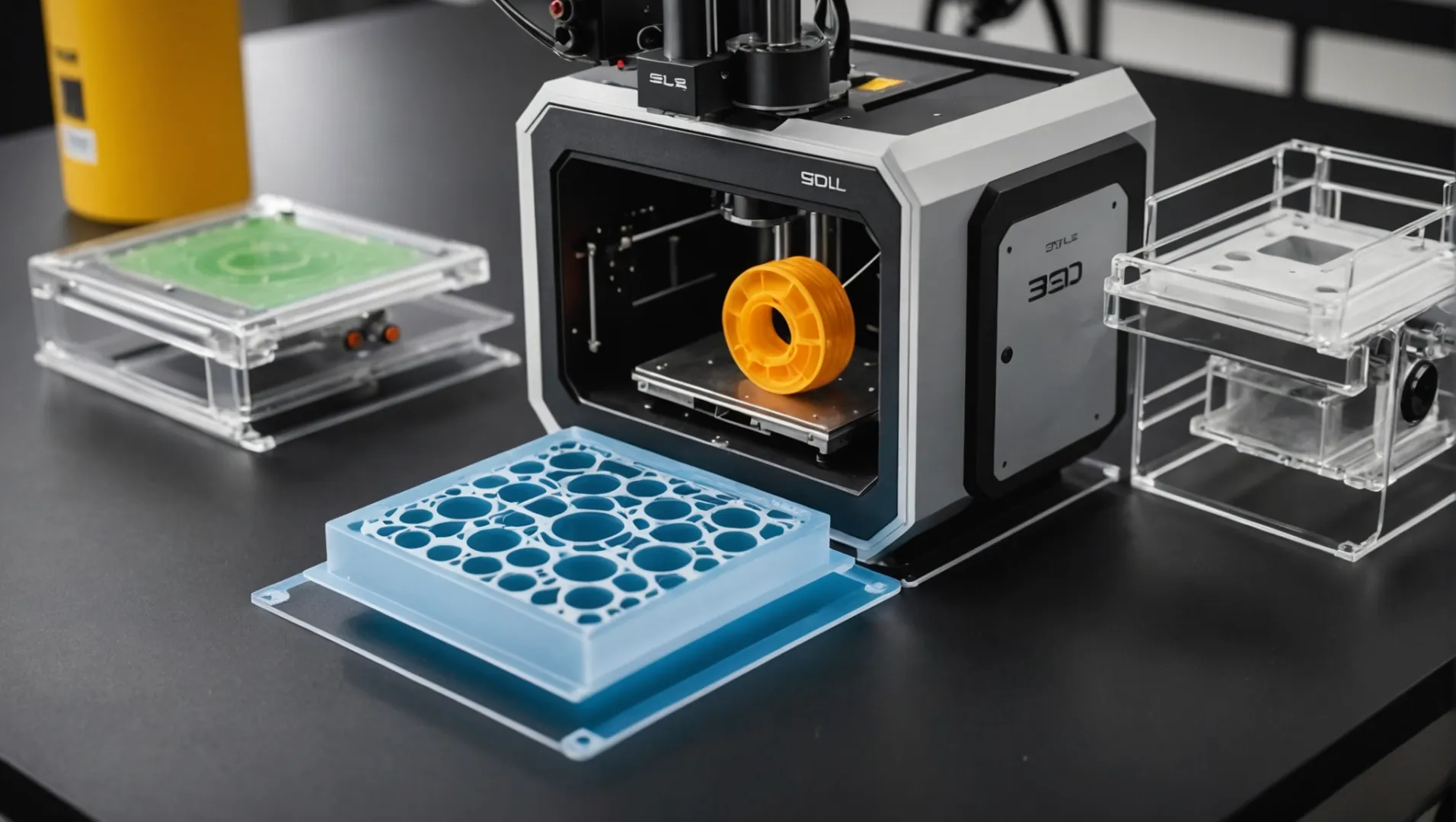
FDM Technology: Building Layer by Layer
FDM, or Fused Deposition Modeling, is a popular 3D printing technology known for its cost-effectiveness and ease of use. It operates by melting thermoplastic filaments and extruding them layer by layer to form an object. When it comes to creating internal holes, FDM relies heavily on the design of the 3D model and the slicing software used.
- Layered Construction: Each layer is carefully constructed by the printer following the model’s design, with specific areas left unfilled to create internal cavities.
- Surface Quality: Due to the nature of layering, the internal surfaces may exhibit lines or imperfections, particularly in smaller holes where precision is more challenging.
- Material Considerations: The choice of filament material can impact the quality and durability of internal structures. For example, PLA may work well for simple designs, while ABS might be needed for more demanding applications.
SLA Technology: Precision with Liquid Resin
SLA, or Stereolithography Apparatus, uses a laser to cure liquid resin into solid parts. It’s renowned for its high resolution and ability to produce intricate details, making it ideal for creating fine internal structures.
- Precision Details: The laser’s accuracy allows for smooth surfaces and precise geometries within the internal holes.
- Material Handling: Uncured resin inside the cavities is drained post-printing, ensuring that only solidified material remains.
- Applications: This technology is particularly useful in industries such as jewelry making or dental applications where high precision is paramount.
SLS Technology: Strength with Powdered Materials
Selective Laser Sintering (SLS) employs a laser to fuse powdered materials. This technology excels in creating strong and complex internal geometries without the need for support structures.
- Complex Structures: Loose powder acts as support during printing, allowing for the creation of complex channels and cavities without additional materials.
- Material Versatility: SLS supports a variety of materials, including metals and plastics, which makes it highly versatile for industrial applications.
- Post-Processing Needs: After printing, unsintered powder must be removed from cavities to reveal the final structure.
Comparing Technologies
Technology | Methodology | Best For |
---|---|---|
FDM | Layer extrusion | Cost-effective prototypes |
SLA | Laser resin curing | High-precision parts |
SLS | Laser powder sintering | Complex mechanical parts |
Each technology offers unique benefits and is suitable for different applications depending on precision needs, material considerations, and design complexity. Understanding these differences is key to choosing the right approach for your project.
FDM is the most precise 3D printing technology.False
SLA, not FDM, is known for high precision due to laser accuracy.
SLS can create complex structures without support.True
Loose powder acts as support, enabling complex geometries in SLS.
How Does Software Design Influence Internal Structures?
Explore how software design shapes the internal architecture of 3D printed objects, optimizing their functionality and strength.
Software design influences internal structures by providing precise control over 3D models, enabling intricate internal features. Slicing software converts these designs into printer instructions, ensuring accurate internal geometry creation.
The Power of 3D Modeling Software
Software design is crucial in shaping internal structures as it allows designers to create highly detailed 3D models with complex geometries. Users can specify the exact location and dimensions of internal features, like holes and cavities, during the modeling phase. This precision ensures that when the model is processed by slicing software, every aspect of the design is translated accurately into printable instructions.
3D modeling software often includes features that allow users to optimize the internal structure of objects for strength, weight, and material efficiency. For example, incorporating lattice structures within a model can significantly reduce weight while maintaining strength.
Slicing Software and Internal Structure Configuration
Once a model is finalized in a 3D modeling program, slicing software takes over to convert it into a series of layers that a printer can execute. This software plays a vital role in defining how internal structures are printed by determining the infill pattern and density.
Feature | Description |
---|---|
Infill Density | Adjusts the solidity of internal structures to affect weight and material usage. |
Infill Pattern | Patterns such as grid, honeycomb, or gyroid can be selected to influence strength and flexibility. |
Wall Thickness | Configures the thickness of outer walls to ensure stability and support for internal structures. |
By adjusting these parameters, designers can influence not only the strength and weight of a printed object but also its overall performance.
Customizing Internal Features for Functionality
Advanced slicing software enables customization of internal features for specific functional requirements. For instance, users can define different infill patterns for various sections of an object to optimize load-bearing capabilities or flexibility.
Designers also have the ability to simulate stress tests within these programs to identify potential weak points in their designs before printing. This foresight allows for adjustments that could enhance the longevity and functionality of the printed item.
Collaborative Design and Iteration
Another significant aspect of software design is its role in collaborative environments. Many platforms allow multiple users to work on the same project, facilitating an iterative design process where team members can propose modifications to internal structures based on testing feedback or new requirements.
This collaboration can lead to innovative solutions that might not have been possible through individual effort alone. Designers can share insights and develop more efficient ways to use material and space within a print.
As technology evolves, software continues to become more intuitive and powerful, offering even greater control over the intricacies of 3D printed internal structures. By harnessing these tools effectively, designers can push the boundaries of what’s possible with 3D printing technology.
3D modeling software allows precise internal feature design.True
3D modeling tools enable detailed specification of internal features.
Slicing software does not affect 3D print infill patterns.False
Slicing software determines infill patterns and density.
What Are the Challenges of Printing Small Interior Holes?
Printing small interior holes in 3D objects can be tricky, requiring precision and careful planning to overcome various technological and material constraints.
The primary challenges of printing small interior holes include precision limitations, layer adhesion issues, and material constraints. Achieving high accuracy and smooth surfaces can be difficult due to the intricacies of different 3D printing technologies.

Precision Limitations in 3D Printing
When dealing with small interior holes, precision is critical. The most common 3D printing technologies—FDM, SLA, and SLS—each come with unique precision challenges. In FDM printing, the nozzle size and layer height directly affect the ability to produce fine details. For instance, a hole smaller than the nozzle diameter might not print accurately, leading to a rough or irregular surface.
SLA printers offer higher precision due to laser solidification but are still limited by the resin’s properties and the laser’s focus. Meanwhile, SLS technology faces challenges in managing unsintered powders within tiny cavities, potentially leading to blockages or imperfections.
To achieve better precision:
- Consider using a smaller nozzle size with FDM.
- Opt for resins with lower viscosity in SLA.
- Ensure proper powder distribution in SLS.
Material Constraints and Properties
The choice of material significantly impacts the ability to print small holes. Some materials may not adequately support thin walls or detailed features due to their physical properties. For example, certain thermoplastics used in FDM might not provide the required rigidity or flexibility, causing deformation or clogging during printing.
In SLA printing, resin viscosity can hinder the formation of small features if not properly managed. Choosing a resin specifically designed for fine details can mitigate this issue. In SLS, the particle size of the powder plays a crucial role; finer powders generally yield better resolution for small holes.
Here’s a comparison table for material considerations:
Technology | Material Concerns | Suggested Solutions |
---|---|---|
FDM | Nozzle diameter, filament quality | Use high-quality filaments |
SLA | Resin viscosity | Select resins for high precision |
SLS | Powder particle size | Opt for finer powder materials |
Layer Adhesion and Support Structures
In FDM and SLA printing, achieving proper layer adhesion in small holes can be problematic. Poor adhesion might lead to structural weaknesses or incomplete features. Support structures are sometimes needed but can introduce additional complexity in removing them without damaging the part.
Techniques to improve layer adhesion include:
- Adjusting print speed and temperature settings in FDM.
- Using higher resolution settings in SLA to ensure complete curing.
- Designing internal supports that are easy to remove post-printing.
In summary, while technologies like FDM1, SLA2, and SLS3 each have inherent challenges when printing small interior holes, understanding these limitations and optimizing design and material choices can significantly enhance print quality.
FDM printing struggles with holes smaller than nozzle diameter.True
FDM's nozzle size limits precision, affecting small hole accuracy.
SLA printers handle small holes without any precision issues.False
SLA faces challenges with resin properties and laser focus limitations.
How Can You Optimize Designs for Better Internal Cavities?
Unlock the full potential of 3D printing by mastering the art of optimizing designs for internal cavities. Discover essential techniques to enhance your prints!
To optimize designs for better internal cavities, consider adjusting infill density, utilizing escape holes, and selecting appropriate materials and support structures. These strategies ensure high-quality prints with functional and precise internal features.

Leveraging Infill Density and Patterns
One of the primary ways to optimize internal cavities is by adjusting the infill density and patterns in your slicing software. Reducing infill density can save material and time, while specific patterns can improve structural integrity.
For instance, using a gyroid infill pattern can enhance strength without significantly increasing weight. Experimenting with different patterns and densities in a controlled manner can lead to an optimal balance between strength, weight, and material usage.
Designing for Escape Holes
Incorporating escape holes is crucial, especially when dealing with hollow prints or complex internal cavities. These holes allow excess material, such as resin or powder, to be removed after printing, preventing defects.
Positioning these holes strategically ensures they do not compromise the structural integrity or aesthetic appeal of the final product. Consider the size and location carefully during the design phase.
Feature | Purpose |
---|---|
Escape Holes | Facilitate removal of excess material |
Support Structures | Aid in maintaining shape during print |
Choosing the Right Materials and Support Structures
Material selection plays a significant role in optimizing internal cavities. Some materials handle internal geometries better than others; for example, SLA is known for its precision, making it suitable for intricate designs.
Support structures are often necessary for maintaining the shape of complex internal features during printing. However, their placement should be strategic to ensure they are easily removable and do not leave marks.
Post-Processing Techniques
Post-processing can refine internal cavities. Techniques such as drilling or sanding can improve the precision and finish of these areas. For threaded holes, using inserts or nuts post-printing is often more reliable than printing threads directly.
Embracing these design strategies4 will enable you to produce high-quality 3D printed objects with optimized internal cavities, enhancing functionality and aesthetic appeal.
Gyroid infill pattern enhances strength without weight gain.True
Gyroid patterns improve structural integrity efficiently.
Escape holes are unnecessary for hollow 3D prints.False
Escape holes prevent defects by removing excess material.
Conclusion
By embracing these design strategies and understanding the technology behind them, you can unlock endless possibilities in 3D printing.
-
Explore solutions for precision issues in FDM printing.: Look for a Hole Horizontal Expansion setting in your slicer and try adjusting that. Another method for repairing 3D printed holes that are too …
-
Find resins ideal for high-detail SLA printing.: How to choose the right 3D printing material? Most commercial 3D resins exhibit poor mechanical properties, such as poor toughness and mechanical strength.
-
Learn how powder size affects SLS print quality.: EOS’ Fine Detail Resolution SLS technology leverages CO lasers to achieve higher resolution and accuracy comparable to injection molding.
-
Discover practical strategies to enhance 3D print quality and functionality.: Learn how to optimize support structures in 3D printing to enhance model stability, minimize material costs, and maintain model aesthetics.