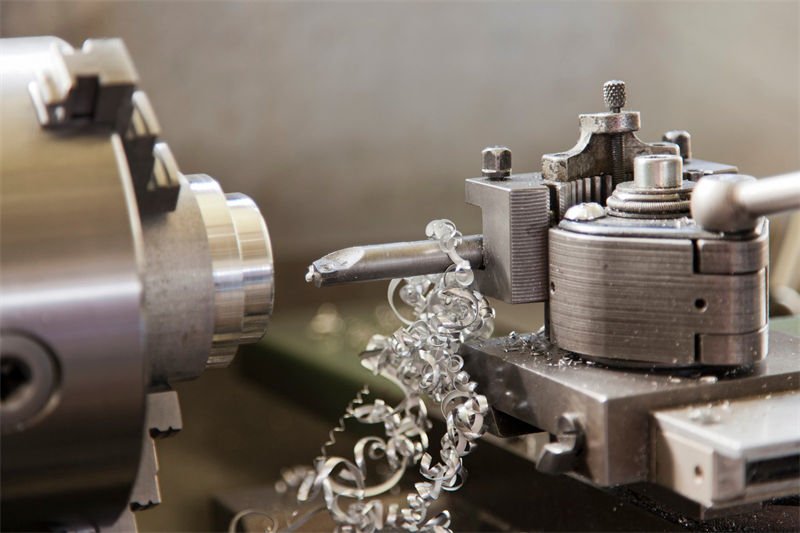
Considering a plunge into CNC machining? You’re not alone! Many share the same question: just how tough is it to operate a CNC mill or lathe?
Operating a CNC mill or lathe involves understanding both basic mechanical principles and more complex programming tasks. While beginners with some mechanical knowledge may find initial operations straightforward, mastering advanced programming and precision takes significant time and practice.
In this post, we’ll explore the various aspects that influence the difficulty of operating CNC machinery. From basic operation to intricate programming and troubleshooting, we’ll provide insights that can guide your decision-making process.
Programming a CNC machine is easy for beginners.False
Basic programming is manageable, but complex tasks require advanced skills.
What Skills Do You Need to Operate CNC Machines?
Thinking about operating a CNC machine? Discover the essential skills required for this high-tech craft.
Operating CNC machines requires mechanical aptitude, programming skills, precision control, and problem-solving abilities. While basic operations might be straightforward for those with mechanical backgrounds, advanced programming and precise machining demand continuous learning and expertise.
Mechanical Aptitude and Understanding
Operating a CNC machine begins with a fundamental understanding of mechanical principles. Individuals should grasp how machines function, including the concepts of workpieces and cutting tools. For those new to this field, developing these skills can take time but is essential for safely and efficiently handling CNC equipment.
To illustrate, imagine a beginner learning about various cutting tools used in CNC1 operations. Understanding the differences between end mills, drills, and turning tools is crucial for selecting the right tool for each task.
Programming Proficiency
CNC machines operate on programmed instructions that guide their movements and actions. Mastering G-code and M-code is foundational, enabling operators to instruct machines for simple tasks such as milling flat surfaces or turning cylindrical shapes. However, more complex programming, like 5-axis machining, requires a deeper understanding of geometric relationships and interpolation methods.
A programmer working on 3D CNC programming techniques2 must be adept at visualizing spatial relationships to produce accurate components.
Precision and Tolerance Control
Achieving precise measurements is vital in CNC machining, especially when producing parts with tight tolerances. Operators must adjust feed rates, spindle speeds, and depths of cut to maintain accuracy. Mastering these adjustments ensures that parts meet design specifications, whether for coarse or high-precision applications.
Problem-Solving Skills
Troubleshooting is an integral part of operating CNC machines. From tool breakage to electrical glitches, operators should quickly identify issues and implement solutions. Developing effective problem-solving skills comes with experience and an understanding of common operational challenges.
For example, addressing issues like tool wear in CNC machining3 is crucial for maintaining consistent production quality.
Continuous Learning and Adaptability
The world of CNC machining is dynamic, with constant advancements in technology and techniques. Staying updated with the latest developments ensures that operators remain competent and competitive. Engaging in regular training sessions and seeking out new information are essential for those looking to excel in this field.
Mechanical aptitude is optional for CNC operators.False
Mechanical understanding is essential for safely and efficiently operating CNC machines.
CNC programming requires mastering G-code and M-code.True
G-code and M-code are foundational instructions that guide CNC machine operations.
How Does CNC Programming Complexity Vary?
CNC programming ranges from simple tasks to highly complex operations, depending on various factors. Understanding these differences can enhance your skills and efficiency.
CNC programming complexity varies based on task requirements, tool paths, and the dimensionality of the machining process. Simple 2D tasks involve basic G-codes, while advanced 3D machining requires multi-axis coordination and intricate tool path planning.
Basic CNC Programming: 2D Operations
At the foundational level, CNC programming for 2D operations involves using basic G-codes and M-codes. These codes direct the machine’s movements and functions, like G00 for rapid positioning or M03 for spindle start. Learning these codes4 typically requires logical thinking and familiarity with the machine’s interface.
- Example: A common task such as creating a flat surface or a simple pocket only requires understanding how to plot a path on a single plane. With practice, operators can execute these tasks efficiently in just a few weeks.
Advanced CNC Programming: 3D and Multi-Axis Machining
As tasks become more complex, such as when dealing with 3D surfaces or multi-axis machining, the difficulty increases significantly. Here, understanding geometric relationships in three-dimensional space is crucial. The use of advanced interpolation methods and software is necessary to manage tool paths effectively.
- Example: Consider a component with intricate curves and angles that require five-axis machining. The programmer must account for continuous tool orientation changes while maintaining precision.
The Role of Software and Tools
Modern software tools have revolutionized CNC programming, making it more accessible but also more demanding in terms of skill. Computer-aided design (CAD) and computer-aided manufacturing (CAM) software are often used to create complex tool paths.
Software | Functionality | Complexity |
---|---|---|
CAD | Designing parts | Moderate |
CAM | Tool path generation | High |
- Example: Mastering CAM software can take months, as it involves understanding both the software’s capabilities and the limitations of the CNC machines.
Challenges in Precision Control
Achieving high precision in CNC programming often involves tight tolerances, requiring advanced understanding of machine parameters like feed rates and spindle speeds. This level of control is crucial when manufacturing parts for industries like aerospace.
- Example: Producing a part with a tolerance of ±0.01mm demands not only precise programming but also experience in adjusting machine settings to minimize external influences such as temperature fluctuations.
Overall, CNC programming complexity is influenced by the scale of the task, required precision, and the tools used. Operators need a balance of theoretical knowledge and practical experience to excel in this field.
Basic CNC tasks only use G-codes.False
Basic CNC tasks use both G-codes and M-codes for operations.
Advanced CNC programming requires CAD software.True
CAD software is essential for designing parts in advanced CNC tasks.
What Are the Challenges in Achieving Precision?
Precision is the backbone of CNC machining, yet achieving it can be a formidable challenge. High-precision work demands not only technical prowess but also a deep understanding of the machines and materials involved.
Achieving precision in CNC machining requires mastering machine capabilities, controlling environmental factors, and continuously improving operational techniques. Tolerances as tight as ±0.01mm necessitate experience, understanding of machine dynamics, and meticulous control over cutting conditions.
Understanding Machine Capabilities
When aiming for high precision, it’s crucial to comprehend your CNC machine’s inherent capabilities. This includes its positioning accuracy, repeatability, and the physical limits of its components. Positioning accuracy refers to how closely a machine can achieve a desired position, while repeatability is the ability to return to a specific position consistently. Knowing these parameters helps in setting realistic expectations and ensures that you don’t push the machine beyond its limits.
The Role of Environmental Factors
Environmental conditions play a pivotal role in achieving precision. Factors like temperature fluctuations can cause the machine components to expand or contract, leading to deviations in the machining process. For instance, maintaining a stable temperature can significantly reduce the risk of thermal distortion5. Vibration is another aspect; even minor vibrations from nearby machinery or foot traffic can affect precision. To mitigate these issues, workshops often employ vibration-dampening bases and controlled climate environments.
Tool Wear and Cutting Forces
Tool wear is inevitable in machining but managing it is key to maintaining precision. As tools wear down, their cutting efficiency diminishes, which can lead to inaccuracies. Regular inspection and replacement of tools are necessary practices. Additionally, controlling cutting forces is critical; excessive force can lead to tool deflection and workpiece distortion. Properly setting feed rates, spindle speeds, and depths of cut are essential techniques to mitigate these effects.
Continuous Improvement and Experience
Achieving high levels of precision isn’t just about technical knowledge—it’s also about experience. Seasoned machinists develop an intuitive understanding of how their machines respond under various conditions. This experience allows them to make real-time adjustments that newer operators might miss. Continuous learning and improvement, such as adopting new technologies or techniques, further enhance precision capabilities.
To aid in the journey toward precision, many machinists turn to advanced software solutions6 that offer simulation and real-time monitoring tools. These solutions help predict potential issues and allow for preemptive adjustments, minimizing errors before they occur.
Temperature fluctuations affect CNC machining precision.True
Temperature changes cause material expansion or contraction, impacting precision.
Tool wear does not impact CNC machining accuracy.False
Tool wear reduces cutting efficiency, leading to inaccuracies in machining.
How Important Is Troubleshooting Expertise?
Troubleshooting expertise in CNC machining is crucial for maintaining operational efficiency and minimizing downtime. Whether facing minor glitches or major mechanical failures, a skilled troubleshooter can be the difference between quick recovery and prolonged disruptions.
Troubleshooting expertise is essential in CNC machining, enabling operators to swiftly identify and resolve issues. This skill helps maintain productivity, prevent costly downtime, and ensure precision in operations. Skilled troubleshooters are vital in addressing both common problems and complex failures efficiently.
The Role of Troubleshooting in CNC Operations
CNC machining, with its intricate blend of mechanical and software components, often encounters a myriad of operational challenges. Troubleshooting expertise plays a pivotal role in ensuring these challenges are met swiftly and effectively. Without adept troubleshooting skills, minor issues can escalate, leading to costly downtime and production delays.
Common Troubleshooting Scenarios
- Tool Breakage: Often caused by improper cutting parameters or tool defects, understanding the root cause and taking corrective measures quickly can prevent further damage.
- Workpiece Clamping Errors: Incorrect clamping can lead to inaccuracies. A troubleshooter must assess and rectify clamping techniques to ensure stability during operations.
- Electrical Glitches: Minor electrical issues often disrupt operations. Identifying faulty circuits or connections requires a fundamental understanding of CNC electrical systems.
Addressing Complex Failures
Complex mechanical failures, such as a damaged spindle or worn-out ball screw, demand advanced troubleshooting skills. Diagnosing these issues requires comprehensive knowledge of the machine’s components and access to specialized tools. Here, advanced CNC troubleshooting techniques7 can be beneficial.
Essential Skills for Effective Troubleshooting
- Mechanical Aptitude: A solid understanding of CNC components enables troubleshooters to quickly pinpoint issues.
- Analytical Thinking: Breaking down problems into manageable parts helps in efficient resolution.
- Continuous Learning: Staying updated with the latest CNC technologies enhances troubleshooting capabilities.
Training and Resources
Given the complexity of CNC systems, formal training programs can significantly bolster troubleshooting expertise. Many resources offer insights into CNC maintenance best practices8, which are invaluable for operators aiming to hone their skills.
Incorporating structured training and continuous education ensures that operators remain adept at handling both routine and unexpected challenges in CNC machining.
Troubleshooting skills prevent CNC downtime.True
Effective troubleshooting minimizes disruptions, keeping CNC operations smooth.
Tool breakage is never a CNC issue.False
Improper cutting parameters often cause tool breakage in CNC machining.
Conclusion
CNC machining presents both challenges and rewards. With passion and practice, anyone can master the basics and even advanced techniques.
-
Explore different cutting tools to enhance machining knowledge.: Types of CNC Cutting Tools (With Illustrations) · #1 Drill Bits · #2 End Mill · #3 Face Mill · #4 Reamers · #5 Gear Cutters · #6 Hollow Mill · #7 Thread Mill. ↩
-
Discover advanced programming methods for complex CNC tasks.: In this instructable I’ll guide you through the process of creating advanced mathematical geometry using programming in combination with cnc-machining. ↩
-
Learn about managing tool wear for optimal machining performance.: Tool wear is the gradual breakdown of machine tools as a result of cutting operation, eventually leading to tool failure. ↩
-
Understand fundamental CNC codes to streamline programming efficiency.: Complete g code and m-code list for Fanuc, LinuxCNC, GRBL, and Haas. Defines each g code plus tutorials and examples. Easy to use! ↩
-
Understand how thermal expansion impacts CNC machining precision.: But the workpiece also shrank, by a different rate. The heat of the process will make both the workpiece and the ballscrews grow, but the … ↩
-
Discover top software solutions for enhancing CNC machining precision.: GibbsCAM is a highly capable CAM package that includes features such as multi-task machining and highly accurate machine simulations. GibbsCAM … ↩
-
Discover detailed methods for addressing complex CNC failures.: Troubleshooting: Inspect machine components for signs of wear or misalignment. Check and tighten loose parts. Balancing tools and components can also mitigate … ↩
-
Learn strategies to enhance CNC machine upkeep and performance.: Monthly Maintenance: · Clean/replace air filters · Check and clean coolant filters · Clean radiators and cooling fans · Review oil fill checklists … ↩