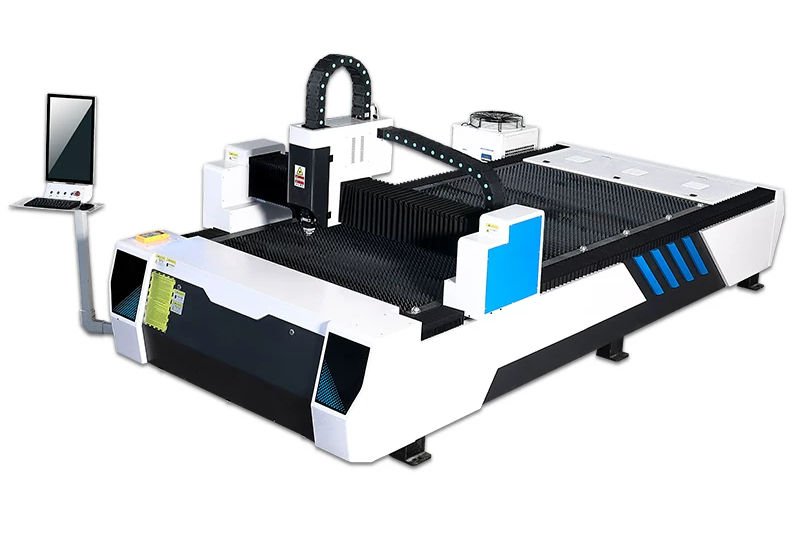
Choosing the right laser cutter for your business is more than just a purchase; it’s a step into a world of creativity and efficiency.
To choose the right laser cutter for your business, consider factors such as material compatibility, power requirements, cutting precision, and budget. Understanding these elements ensures that you select a machine that meets your specific needs and operational goals.
While these initial criteria set the stage, delving deeper into each factor will unveil insights crucial to your specific industry and application. Let’s explore these considerations in detail!
Fiber lasers are best for cutting metals.True
Fiber lasers offer high energy density, ideal for precise metal cutting.
How Does Material Type Influence Your Laser Cutter Choice?
Choosing the right laser cutter hinges significantly on the types of materials you intend to cut.
The type of material you work with is crucial in determining your laser cutter choice. Fiber lasers excel in cutting metals like steel and aluminum, while CO₂ lasers are more suited for non-metals such as wood and acrylic. Understanding material compatibility ensures efficient cutting performance and quality results.
Understanding Material Compatibility
When selecting a laser cutter, the first consideration should be the material types you intend to work with. This decision can significantly impact the efficiency and effectiveness of your operations.
Metals vs. Non-Metals
- Metal Cutting: If your business primarily deals with metals like stainless steel or aluminum, a fiber laser cutter would be more suitable. These cutters provide excellent precision and speed due to their high energy density, making them ideal for industries requiring intricate metalwork.
- Non-Metal Cutting: For businesses focusing on materials such as wood, acrylic, or leather, a CO₂ laser cutter is typically recommended. The wavelength of CO₂ lasers matches well with non-metals, allowing for clean cuts and engravings.
Impact of Material Thickness
Material thickness also plays a role in laser cutter selection. Different machines have varying capabilities based on their power levels.
Material | Recommended Laser Type | Power Requirement (Watts) |
---|---|---|
Thin Metals (< 3mm) | Fiber Laser | 1000 – 1500 |
Thick Metals (10 – 20mm) | Fiber Laser | 3000 – 4000 |
Wood (5 – 10mm) | CO₂ Laser | 80 – 100 |
Understanding these nuances can help you choose a laser cutter that not only meets your current needs but also accommodates future projects.
Considerations for Specific Industries
Each industry has unique requirements that further influence the choice of laser cutter:
- Advertising Production: Industries using acrylic or PVC benefit from CO₂ lasers due to their ability to handle intricate shapes and engravings.
- Metal Fabrication: For industries requiring precision in metal parts, fiber lasers are preferred for their fine beam quality.
- Craft and Design: Smaller CO₂ lasers are ideal for artisans working with wood or leather, offering precision without compromising creativity.
By aligning your choice of laser cutter with the materials and industry requirements, you optimize performance and output quality. For further insights into material-specific laser cutting1, explore expert recommendations tailored to your business needs.
Fiber lasers are best for cutting metals.True
Fiber lasers excel in cutting metals like steel and aluminum.
CO₂ lasers are unsuitable for wood cutting.False
CO₂ lasers are ideal for cutting non-metals like wood and acrylic.
What Are the Power Requirements for Different Materials?
Understanding power requirements is key to optimizing laser cutter performance for diverse materials.
The power requirements for different materials vary significantly. Metals typically require higher power levels, ranging from 1000W to 4000W for effective cutting, whereas non-metallic materials like wood and acrylic can be processed with lower power settings, generally between 40W to 150W. Selecting the right power ensures precision and efficiency.
Power Needs for Metal Cutting
When it comes to metal cutting, the power requirements are crucial due to the hardness and density of metals. Fiber laser cutters2 are commonly used for their high energy density and efficient metal penetration.
-
Thin Metals (up to 3mm): For materials like thin stainless steel or aluminum, a laser cutter with a power range of 1000W to 1500W is adequate. This power level allows for clean cuts without excessive heat.
-
Medium Metals (3mm to 10mm): Metals such as carbon steel in this thickness range require a higher power level, typically around 2000W to 3000W. This ensures both precision and speed, balancing productivity with quality.
-
Thick Metals (10mm to 20mm): For thicker sheets, especially those used in heavy-duty applications, a power level of 3000W to 4000W is recommended. High power ensures deep penetration and smooth cutting edges.
Power Needs for Non-Metallic Materials
Non-metallic materials, widely used in industries such as advertising and handicrafts, have different power needs compared to metals.
-
Wood: A CO₂ laser cutter with a power range of 40W to 100W can efficiently handle various wood types. For instance, softer woods may require less power, while harder varieties like oak might need closer to the upper range.
-
Acrylic and Plastics: These materials typically require laser powers between 60W to 150W. Lower power settings are sufficient for thinner sheets or detailed engraving, whereas thicker acrylics demand higher power for smooth edges and precise cuts.
-
Textiles: For fabric cutting, a 60W to 100W CO₂ laser cutter is ideal. This setting prevents fraying by cauterizing the edges as it cuts, making it perfect for the garment industry.
The Balance of Power and Precision
Achieving the right balance between power and precision is critical. Overpowering can lead to material warping or burns, while underpowering might cause incomplete cuts or slow production speeds. High-precision laser cutters3 often incorporate advanced control systems that optimize these parameters based on material feedback.
Material | Power Range (Watts) | Comments |
---|---|---|
Thin Metals | 1000 – 1500 | Suitable for detailed work |
Medium Metals | 2000 – 3000 | Balances speed and precision |
Thick Metals | 3000 – 4000 | Ensures smooth cuts |
Wood | 40 – 100 | Varies with wood type |
Acrylic | 60 – 150 | Higher for thick sheets |
Textiles | 60 – 100 | Ideal for non-frayed edges |
Understanding these power requirements not only enhances cutting performance but also optimizes operational costs and material utilization. By selecting the appropriate laser cutter power settings, businesses can achieve superior results tailored to their specific material needs.
Metals require higher laser power than wood.True
Metals need 1000W-4000W, while wood requires 40W-100W.
Acrylic cutting needs more power than textile cutting.True
Acrylic uses 60W-150W; textiles use 60W-100W.
Why Is Cutting Precision Crucial for Your Business Needs?
Precision in cutting is vital for maintaining the quality and efficiency of manufacturing processes.
Cutting precision is crucial for businesses as it ensures product quality, minimizes material waste, and enhances production efficiency. Precise cutting leads to consistent output, meeting industry standards and customer expectations, ultimately impacting profitability and brand reputation.
The Impact of Precision on Product Quality
In industries like electronics and aerospace, cutting precision is non-negotiable. For example, in electronics manufacturing4, components often require cuts that adhere to tolerances within micrometers. This level of precision ensures that parts fit perfectly, maintaining device functionality and safety standards.
Consider a scenario where a mobile phone casing needs precise cutouts for camera lenses. A deviation in precision could result in malfunction or aesthetic flaws. By using high-precision cutting equipment, businesses can avoid costly errors and maintain a high level of product quality.
Minimizing Material Waste with Precision
Accurate cutting leads to optimal material utilization. When cuts are precise, the margin for error decreases, reducing excess material waste. This not only saves costs but also aligns with sustainable business practices. For instance, in the garment industry, fabric patterns are cut with exact precision to ensure maximum use of the material, minimizing offcuts.
Example Table: Waste Reduction through Precision
Industry | Material Type | Waste Reduction Benefit |
---|---|---|
Garment | Fabric | Lower material costs |
Metal Fabrication | Steel | Reduced scrap metal generation |
Woodworking | Timber | Efficient use of valuable resources |
Enhancing Production Efficiency
Precision cutting machines contribute to faster turnaround times without compromising quality. For batch productions, this means a significant increase in output. In industries such as automotive manufacturing, where large volumes of parts are required quickly and accurately, high-speed precision cutters ensure that production schedules are met efficiently.
Moreover, precision allows for seamless integration with automated systems. By utilizing software-driven cutting paths, machines can achieve consistent results with minimal human intervention, further enhancing efficiency5 and reducing labor costs.
Maintaining Competitive Advantage
In a competitive market, the ability to deliver high-quality products consistently can be a differentiator. Businesses that invest in precision cutting technology often find themselves ahead of competitors who rely on less accurate methods. This advantage can lead to increased market share and customer loyalty.
Furthermore, precision cutting supports innovation. It allows for intricate designs and complex geometries that were previously unattainable with conventional cutting methods. This capability opens new avenues for product development and customization, catering to evolving customer demands.
Precision cutting reduces material waste in manufacturing.True
Precise cuts optimize material use, minimizing waste and costs.
Inconsistent cutting does not affect product quality.False
Inconsistent cuts lead to defects, impacting quality and reliability.
How Do Budget Constraints Affect Your Laser Cutter Selection?
Budget constraints significantly influence the selection of a laser cutter, balancing between initial costs and long-term investment returns.
Budget constraints affect laser cutter selection by determining the balance between upfront purchase costs and long-term operational expenses. Assessing these factors helps ensure that the machine aligns with both financial capabilities and production requirements.
Evaluating Initial Purchase Costs
When selecting a laser cutter within budget constraints, understanding the initial cost is vital. Laser cutters vary widely in price, from affordable CO₂ models suitable for small-scale operations to more expensive fiber lasers designed for industrial use.
- Small Enterprises: A small handicraft shop might opt for a CO₂ laser cutter6 priced in the tens of thousands, focusing on non-metallic materials like wood or acrylic.
- Large Industries: Conversely, a metal processing plant may require a high-power fiber laser cutter, costing upwards of millions, to handle thicker materials and ensure high precision.
Business Type | Recommended Laser Type | Approximate Cost Range |
---|---|---|
Handicraft Shop | CO₂ | $10,000 – $30,000 |
Metal Processing | Fiber | $100,000 – $1,000,000 |
Calculating Long-Term Operating Costs
Operating costs can also sway the choice of a laser cutter. Consider energy consumption, maintenance, and consumables when evaluating long-term expenses.
- Energy Efficiency: Fiber lasers are known for lower energy consumption compared to CO₂ lasers, which can result in significant savings over time.
- Consumable Longevity: Fiber lasers boast a longer lifespan for critical components like laser generators, reducing replacement frequency and costs.
Balancing Performance with Financial Limitations
While budget constraints may dictate certain limitations, they shouldn’t compromise performance essential to your business operations.
- Prioritize Features: Identify essential features that align with your production needs without exceeding your budget. For example, prioritize cutting precision over speed if your business requires high accuracy.
- Explore Financing Options: Consider leasing or financing plans that allow access to higher-end models without upfront full payment, easing cash flow pressures.
In conclusion, navigating budget constraints while selecting a laser cutter involves a thorough assessment of both immediate and ongoing expenses. By strategically evaluating these elements, businesses can ensure they invest in a machine that supports their operational and financial goals efficiently.
CO₂ lasers are more energy-efficient than fiber lasers.False
Fiber lasers are generally more energy-efficient than CO₂ lasers.
Fiber lasers have longer component lifespans than CO₂ lasers.True
Fiber lasers typically require less frequent component replacements.
Conclusion
By carefully weighing material compatibility, power needs, precision, and budget, you can confidently choose a laser cutter that enhances your business productivity.
-
Explore detailed insights into matching laser cutters with material types.: There are several laser cutting materials available ranging from wood, acrylic, metals, and foam. Learn more about laser cutting and the …
-
Discover how fiber lasers excel in precision metal cutting.: Cut full sheets of carbon and stainless steel, as well as aluminum, titanium, brass, bronze, copper, and more with laser accuracy on Hytek Tools Fiber Lasers.
-
Explore advanced laser cutters that enhance precision and efficiency.: High-precision fiber laser cutter can be used in cutting carbon steel, stainless steel, aluminum alloy, brass, copper, galvanized sheet, silicon steel plate, …
-
Learn why precision is vital for electronics quality and safety.: Precision manufacturing is what happens when a design is developed that requires highly accurate components and is made into a workable part.
-
Explore how precision boosts production speed and reduces costs.: By improving your cutting, you can increase your speed and consistency, and so reduce the need for time-consuming grinding and polishing. In this article, our …
-
Learn about CO₂ laser costs and benefits for informed decision-making.: CO2 laser cutters, ideal for non-metal materials, typically range from $8,000 to $50,000, with power outputs of 100W to 500W. When you invest in …