
Choosing the perfect CNC lathe feels like a journey, with each decision potentially transforming your production line.
When selecting a custom CNC turning lathe, consider the size and shape of parts, precision requirements, material characteristics, and performance specifications. It’s crucial to evaluate automation features and cost to ensure it aligns with your operational needs and goals.
Let’s break it down further. I remember when I first delved into this world—standing in front of those massive machines, feeling a mix of excitement and intimidation. It’s not just about the machine’s specs; it’s also about envisioning how it fits into your workflow, much like piecing together a giant puzzle. Understanding the nuances of these factors can dramatically impact your decision-making process, offering insights and advice that could make all the difference in your final choice. It’s about ensuring that every piece of your production puzzle fits perfectly.
A CNC lathe with multi-axis movement is needed for simple parts.False
Simple parts don't require multi-axis movement; basic turning suffices.
High spindle precision is crucial for shape precision in CNC lathes.True
Spindle precision affects cylindricity, roundness, and straightness.
How do processing requirements influence your lathe choice?
Ever tried to pick the perfect lathe, only to feel overwhelmed by all the options? Let’s break down how your specific needs can guide your choice.
Processing requirements shape your lathe choice by influencing size, precision, power, and tool compatibility. Consider part size, complexity, precision, and material properties to ensure optimal machining performance.
Part Size and Complexity
When selecting a lathe, understanding the size and complexity of parts is crucial. Larger parts require lathes with extended beds and greater spindle distances. For example, processing large shaft-like parts1 demands significant bed lengths to accommodate these dimensions. Conversely, smaller precision parts necessitate lathes with fine movement control and high precision to ensure accurate results.
The complexity of part shapes also dictates lathe choice. Parts with intricate curves or grooves may require multi-axis capabilities for precise cutting. A lathe with these features can effectively manage complex geometries, ensuring that the tool can reach all necessary areas without sacrificing accuracy.
Precision Requirements
Precision needs vary across industries. High-precision fields like aerospace demand lathes capable of achieving tolerances as tight as ±0.01mm. This requires precise positioning and repeat positioning capabilities, ensuring consistent accuracy in batch production.
To meet these needs, consider lathes with high positional accuracy2, often needing precision feed systems that manage small adjustments for exact cutting dimensions. In contrast, industries with looser precision standards might prioritize different lathe attributes.
Material Characteristics
The material being machined significantly influences lathe selection. High-hardness materials like quenched steels require lathes with robust spindles and sufficient power to handle tough cutting operations. This involves ensuring the spindle system can support strong cutting forces without compromising on accuracy.
For softer materials like aluminum, the focus shifts to preventing material deformation. Lathes with refined feeding systems can manage smaller feed rates, reducing potential deformation during processing and ensuring superior surface quality.
Processing Techniques and Tool Compatibility
Different processing techniques necessitate specific lathe functions. Lathes designed for multiple operations such as drilling, boring, and tapping should feature appropriate functional modules. For instance, tapping operations3 require precise pitch control to maintain thread quality.
Tool compatibility is another vital consideration. A lathe should be able to accommodate a range of tools for various operations while maintaining quick tool change capabilities to maximize efficiency and reduce downtime in production cycles.
CNC lathes need high spindle precision for aerospace parts.True
Aerospace parts require high dimensional precision, demanding precise spindle control.
Automatic tool changing reduces CNC lathe efficiency.False
Automatic tool changing actually enhances efficiency by minimizing downtime.
What Performance Parameters Are Critical for CNC Lathes?
Imagine the hum of a CNC lathe as the heart of your workshop, where the right tweaks can transform precision machining into an art form.
Critical performance parameters for CNC lathes include spindle speed, torque, power, feeding speed, precision, and resolution. Each of these plays a vital role in how the machine handles materials and achieves desired outcomes. Properly adjusting these parameters can greatly enhance precision and efficiency in machining tasks.
Spindle Speed and Torque
Let me take you back to the first time I realized how spindle speed can be a game-changer. I was working on an aluminum part, and upping the spindle speed4 brought that smooth finish I was chasing. Spindle speed determines how fast the workpiece spins, impacting both the cutting force and surface finish. High speeds are essential for softer materials like aluminum, while tougher materials like steel may need lower speeds to avoid tool damage.
Then there’s torque. Picture torque as the muscle behind the spindle’s spin. When I tackled a hardened steel piece, having enough torque meant my tool didn’t stall during deep cuts—an absolute lifesaver.
Feeding Speed and Precision
Feeding speed was another revelation for me. During a roughing operation, I cranked it up to clear material fast; yet, when it came to finishing touches, slowing it down was key to nailing that fine detail. A higher feed rate5 might be advantageous for roughing operations to remove material rapidly. Conversely, finishing operations typically require a slower feed rate to ensure surface smoothness and dimensional accuracy.
Precision and resolution in the feeding system are essential for achieving detailed work. These factors determine the smallest movement increment possible, influencing the machine’s ability to produce intricate designs with high accuracy.
Power and Efficiency
Power is like the backbone of the CNC lathe—it keeps everything running smoothly even under pressure. I remember this one high-power machine I worked with that could handle large cuts without breaking a sweat. It’s a dream when time is money, and efficiency becomes a must-have.
Efficiency isn’t just about speed, though; it involves considering the tool holder system6 too. Quick tool changes are a time-saver, while stability during operations keeps precision in check.
Automation and Control
Automation in modern CNC lathes is like having an extra set of hands. With automated loading/unloading systems reducing manual intervention, I could focus on other tasks while the machine did its thing—perfect for high-volume jobs.
Control systems allow for easy programming and real-time monitoring so adjustments are a breeze when things don’t go as planned.
Material and Process Compatibility
The flexibility to handle different materials7 is crucial. Machines equipped to handle various materials offer greater versatility in production processes. Whether it’s threading or grooving, precise control over tool paths and speeds ensures quality isn’t compromised.
Environmental and Cost Factors
Operational costs always sneak up on you. Machines with energy-efficient designs can keep these in check over time by reducing power consumption significantly. Understanding tooling costs and maintenance schedules means fewer surprises down the line.
In short, mastering these parameters is like having a secret recipe for top-notch CNC operations—it’s all about quality and efficiency in the workshop.
CNC lathe's spindle speed affects surface roughness.True
Higher spindle speeds can improve surface finish by reducing tool marks.
All CNC lathes can process complex shapes like engine blades.False
Only multi-axis CNC lathes can handle complex shapes due to their movement capabilities.
Why Is Material Compatibility Important in CNC Machining?
Ever tried baking cookies without the right ingredients? CNC machining is similar, where choosing compatible materials is key to precision and quality.
Material compatibility in CNC machining is crucial for optimal performance and part quality. It influences tool wear, machining efficiency, and meeting design specifications.
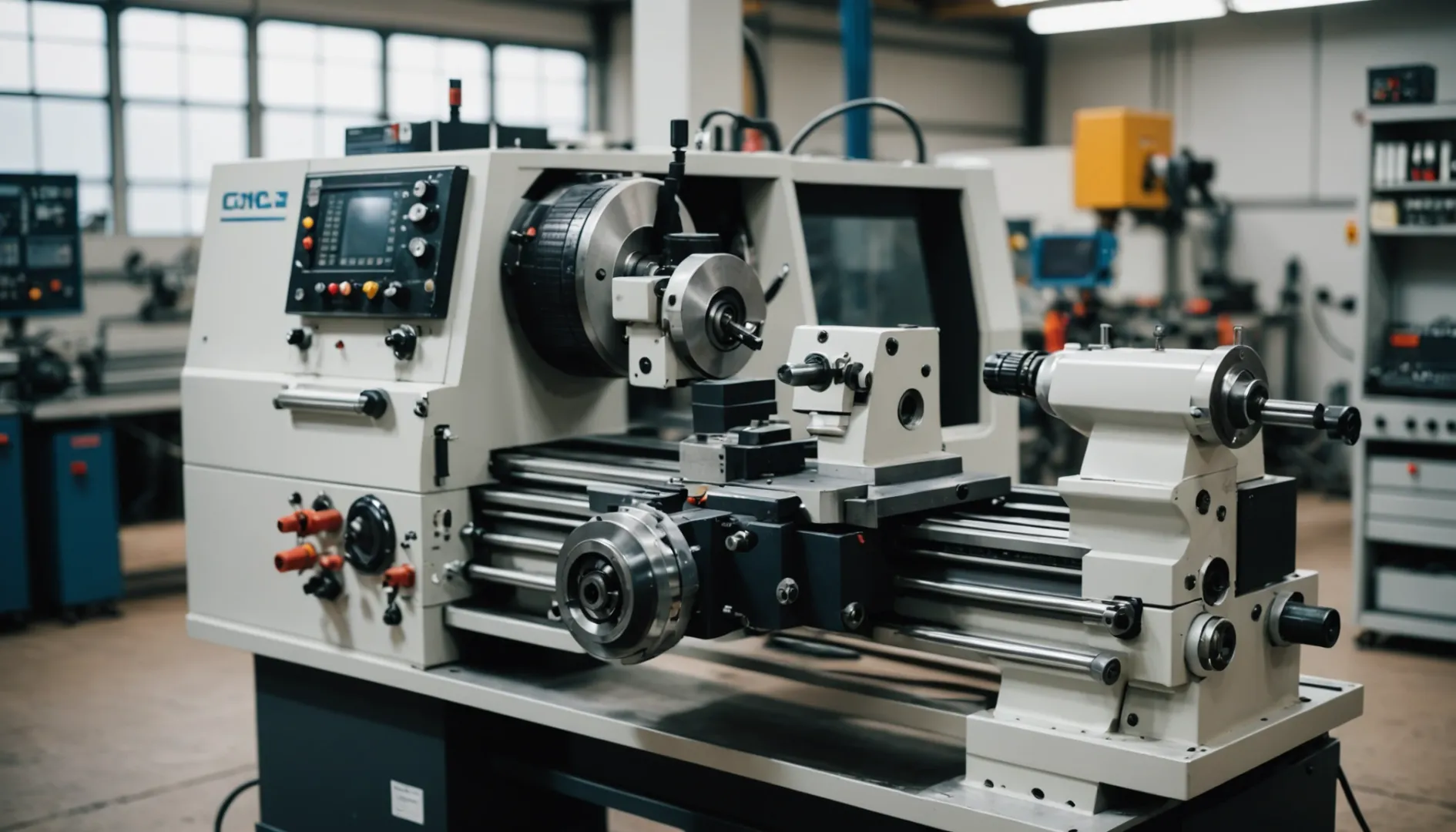
Understanding Material Properties
The selection of materials in CNC machining isn’t just about availability or cost; it revolves around understanding the material properties8 that affect machining performance. You know that feeling when you buy a new gadget and have to figure out which cords and accessories are compatible? Choosing materials for CNC machining can feel just like that. It’s not just about picking what’s available or the cheapest option—it’s about understanding what each material brings to the table. For instance, I once had to choose between aluminum and stainless steel for a project. Aluminum won for its light weight and machinability, whereas stainless steel offered that all-important corrosion resistance. These choices guide what tools we use and how we set up our machines, much like how you’d pair a specific phone charger with your phone.
Impact on Tool Wear
Material compatibility significantly influences the wear and tear on CNC tools. Imagine using a butter knife to chop a tree—it wouldn’t last long, right? That’s the dilemma with tool wear in CNC machining. Harder materials, such as titanium alloys, demand robust tools that can withstand high friction and heat, leading to increased wear if not compatible—it’s like trying to cut steak with a plastic knife. Conversely, softer materials like plastics can cause issues like buildup on cutting edges9, affecting surface finish quality. Understanding these interactions helps in selecting suitable tools and machining parameters.
Efficiency and Speed Considerations
Think of this like driving a car: you need the right fuel for optimal performance. Choosing the right material affects the overall efficiency and speed of the CNC machining process. Compatible materials enable smoother cuts, reducing cycle time and enhancing production throughput. Materials like brass offer machinability benefits that allow us to speed things up without losing quality—kind of like hitting the highway in a well-tuned car—but when dealing with tougher materials, slowing down becomes crucial to maintain precision; it’s all about balance.
Meeting Design Specifications
Remember when you tried building a model that fell apart because the pieces didn’t fit perfectly? In CNC machining, material compatibility is pivotal in meeting design specifications during CNC machining. Each material possesses unique characteristics affecting strength and thermal stability influencing the final part’s strength, durability, and thermal properties. Just as a building needs the right foundation, high-performance applications may require materials with specific thermal expansion rates10 to maintain dimensional stability under varying temperatures.
Ensuring Part Integrity
It’s like choosing the right shoes for hiking—using unsuitable materials can lead to failure in high-stress environments. Finally, material compatibility ensures that parts won’t buckle under mechanical stress ensuring their integrity in machined parts. For instance, aerospace components need to withstand significant stress without bending or breaking require materials that can withstand high stress without deforming. Picking the wrong material could lead to disastrous outcomes emphasizing why understanding material stress limits11 is essential.
CNC lathes require multi-axis for complex shapes.True
Complex shapes need multi-axis movement for precise cutting.
High-hardness materials need low spindle power in CNC lathes.False
High-hardness materials require high spindle power for cutting.
How Do Costs and After-Sales Service Affect Your Decision?
Ever tried picking the perfect piece of equipment and felt overwhelmed by the hidden costs and support services?
Costs and after-sales service significantly influence buying choices by shaping budget decisions and ensuring product reliability. Finding the right balance between initial cost and ongoing support is key to maximizing value and achieving long-term satisfaction.

Understanding the Impact of Purchase Costs
Ah, the moment when I stood on the shop floor, staring at a shiny new CNC lathe, contemplating whether those extra bells and whistles were worth the dent they would make in my wallet. High-end models can be a big investment, but if you’re into crafting intricate aerospace components like I am, those added features might be your best friend. On the flip side, for simpler tasks, a mid-range lathe could be just the ticket, offering a sweet spot between functionality and cost.
I’ve also learned the hard way that customization can rack up those expenses quickly. It’s crucial to weigh these costs against potential boosts in productivity or quality. Understanding budget constraints12 is essential when considering these customizations.
Analyzing Running Costs
Picture this: You’ve bought your dream lathe, but then the electricity bills come knocking, and you’re left wondering if it was all worth it. CNC lathes with high spindle power might gobble up more energy, but they also slash processing times. It’s a dance between operational costs and efficiency—one I’ve had to master over countless cups of coffee.
Beyond initial purchase costs, running expenses such as electricity consumption and maintenance play a pivotal role in decision-making. Evaluating these factors helps optimize long-term expenditure.
The Role of After-Sales Service
Nothing beats the peace of mind that comes from knowing help is just a call away. When my machine breaks down in the middle of a project, it’s not just frustrating—it’s potentially costly. A solid after-sales service can save the day by offering installation help, maintenance, and quick repairs. I’ve learned to prioritize suppliers who provide excellent service as it pays off in reduced downtime and longer equipment life.
After-sales service ensures that your equipment remains operational and efficient. Engaging with suppliers known for reliable service13 can lead to lower overall costs by minimizing downtime and extending equipment lifespan.
Comparing Cost-Effectiveness of Different Suppliers
When I started comparing suppliers, I realized that sometimes paying a bit more upfront gets you a far better deal in the long run. Those suppliers who offer slightly pricier machines often come through with exceptional service packages that cut down on maintenance costs and extend warranties.
When evaluating potential suppliers, it’s beneficial to compare not only their pricing but also their after-sales support quality. Understanding these comparative advantages14 really helps when making an informed decision.
All in all, weighing both the initial cost and the quality of after-sales service offers a comprehensive picture of what you’re getting into. This approach ensures that your choice not only meets today’s production demands but also aligns with future business growth.
CNC lathes require high spindle power for soft materials.False
Soft materials like aluminum need less spindle power due to lower cutting forces.
High-precision CNC lathes can achieve ±0.01mm accuracy.True
Industries like aerospace demand CNC lathes with ±0.01mm precision for parts.
Conclusion
When choosing a custom CNC turning lathe, consider part size, precision requirements, material characteristics, automation features, and cost to optimize production efficiency and meet operational goals.
-
Explore large shaft machining lathes for accommodating extensive part dimensions.
-
Understand CNC lathe positional accuracy requirements for high-precision industries.
-
Learn about precise pitch control in CNC lathes for tapping operations.
-
Understand how spindle speed affects cutting conditions and material handling.
-
Learn about feed rate’s impact on material removal and surface finish.
-
Explore how tool holder systems enhance stability and precision.
-
Discover how material versatility enhances production flexibility.
-
Learn about how material properties impact CNC machining processes.
-
Understand the importance of thermal expansion rates in material selection.
-
Explore how material stress limits affect CNC machined parts.
-
Explore strategies for balancing budget with CNC lathe requirements.
-
Discover why dependable after-sales support enhances equipment longevity.
-
Learn how to assess suppliers based on pricing and service value.