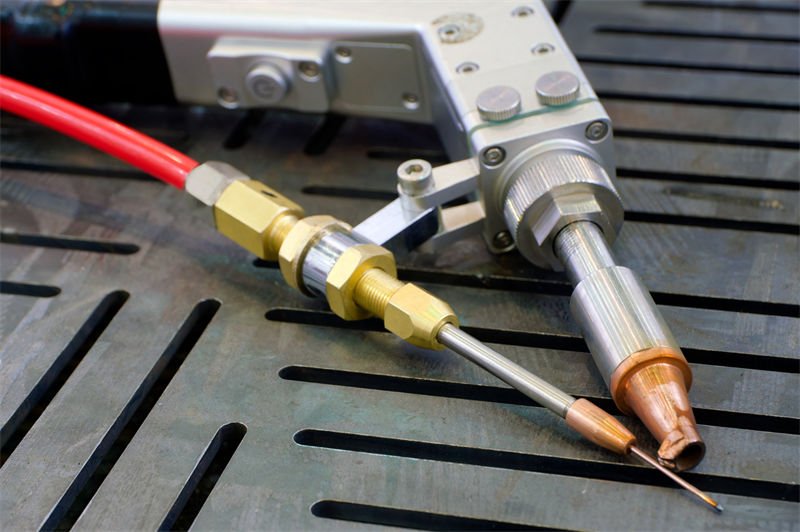
Navigating the maze of handheld laser welding machines can feel overwhelming, but don’t worry, I’ve been there too!
When it comes to small workshops, finding the best handheld laser welding machines means looking for models that offer a sweet spot between power, versatility, and cost. The Ironsten XING Laser 1500W and ZAC 1500Watt MAX Fiber Laser Welder stand out, boasting features like welding, cutting, and cleaning in one compact package, perfect for tight spaces.
I remember the first time I had to choose a welding machine for my workshop. It felt like I was looking for a needle in a haystack. There are so many options out there, each promising to be the ‘best.’ But what really matters is finding a machine that fits your unique needs—much like hunting for that perfect pair of shoes. They need to fit just right and work well with everything else you have going on.
Let’s dive deeper into what makes these models so special. The Ironsten XING Laser 1500W is like a multitool for your workshop, ready to tackle anything from welding to cutting and even cleaning. On the other hand, the ZAC 1500Watt MAX Fiber Laser Welder packs a punch with its fiber laser tech, making it versatile enough to handle materials like carbon steel and titanium.
Think about your space constraints too. Compact machines not only fit better but also allow you to move them around easily if needed. I often find myself rearranging things in my workshop to make room for new projects, and having a portable machine has been a lifesaver.
Ultimately, it’s about matching these features with what you need most. Whether you’re looking at power output, functionality, or budget considerations, understanding these aspects will lead you to a choice that feels just right for your small workshop’s demands.
Ironsten XING Laser 1500W is suitable for small workshops.True
It offers power, versatility, and cost-efficiency ideal for confined spaces.
ZAC 1500Watt MAX Fiber Laser Welder lacks versatility.False
The model includes welding, cutting, and cleaning functions, proving versatile.
What Should You Look For in a Laser Welding Machine?
Buying a laser welding machine isn’t just about ticking off features—it’s about finding the right fit for your workshop’s unique needs.
When choosing a laser welding machine, focus on power output, functionality, portability, and material compatibility to ensure it meets your workshop’s specific needs and enhances productivity.
Power Output: Finding the Right Balance
Back when I first started out, balancing power output with cost was a tricky dance. In my experience, a power range between 1000W and 1500W usually offers just the right blend of efficiency and affordability for most small workshops. I remember upgrading to a model with adjustable power settings; it was like having a Swiss Army knife at my disposal. Suddenly, every project seemed manageable.
Functionality: More Than Just Welding
I can recall the excitement of discovering that some machines could do more than just weld. The first time I got my hands on an Ironsten XING Laser 1500W, I realized how much space and money I could save with its multifunctional capabilities. It’s not just about welding anymore—cutting and cleaning became integral parts of my workflow, all packed into one neat machine.
Model | Power (W) | Functions | Portability |
---|---|---|---|
Ironsten XING | 1500 | Welding, Cutting, Cleaning | High |
STYLECNC | 1000 | Welding | High |
Portability: Maneuverability Matters
In my compact workshop, every inch counts. That’s why I was thrilled to find portable machines like the STYLECNC 1000W. It’s lightweight and easy to move around—perfect for the ever-changing layout of a busy workshop. I remember the relief of being able to rearrange my space without worrying about the logistics of shifting heavy equipment.
Material Compatibility: Versatility in Application
One lesson I’ve learned is the importance of material compatibility. The Royell Handheld Fiber Laser stands out for its versatility. It handles everything from carbon steel to aluminum effortlessly. Plus, its ergonomic design means I can work longer hours without feeling like I’ve been wrestling with a bear all day.
Budget Considerations
I’ve been down the road where budget constraints were tight. While top-tier models offer extensive features, I’ve found entry-level options like the STYLECNC 1000W strike a good balance between cost and functionality. It’s crucial to weigh these costs against your long-term goals—after all, every penny counts1 in business planning.
A 1000W laser welder is sufficient for small workshops.True
A 1000W laser welder balances capability and cost for small workshops.
Ironsten XING Laser 1500W lacks cutting functionality.False
Ironsten XING Laser 1500W includes welding, cutting, and cleaning functions.
How Does Power Output Affect Laser Welding Performance?
Have you ever wondered how the power settings on your laser welder might be the secret to perfect welds every time?
Power output in laser welding determines the weld’s depth and speed. Higher power can achieve deeper penetration and faster processing, enhancing efficiency but might cause overheating and quality issues if not properly managed.
I remember the first time I played around with a laser welder. The hum of the machine was electrifying, and I was eager to see it in action. But what I quickly learned was that tweaking the power output was like fine-tuning a musical instrument—too much or too little could make all the difference.
The Role of Power Output in Weld Penetration
One of my early experiments involved trying to weld two pieces of metal that were way thicker than I was used to. It hit me then how crucial power output is for penetration depth. If you think of power output as the engine of your car, you’ll understand why more power can get you further—or in this case, deeper—into thicker materials. For example, using a 1500W laser welder instead of a 1000W model allowed me to weld through thicker metal with ease.
Power Output (W) | Material Thickness (mm) | Typical Applications |
---|---|---|
1000 | Up to 3 | Thin sheet metals |
1500 | 3-6 | Medium thickness parts |
2000+ | Over 6 | Heavy-duty applications |
Of course, cranking up the power isn’t always the best idea. I remember ruining a perfectly good piece of thin metal by burning right through it because I’d set the power too high. It’s all about finding that sweet spot2 where you balance power with material thickness for optimal results.
Impact on Welding Speed and Efficiency
I once had to meet a tight deadline, and increasing the power output was a lifesaver because it sped up the welding process significantly. It’s like turning up the heat when you’re cooking; things happen faster. But just like cooking, you have to watch out for overdoing it. Too much heat and you might end up with defects like distortion or spatter, which I’ve learned the hard way.
Increasing power output generally increases welding speed as more energy is available to melt material quickly, enhancing productivity by reducing cycle times in manufacturing processes.
The challenge lies in controlling heat input to avoid defects such as distortion or spatter. Careful calibration and monitoring are needed to maximize efficiency3 without compromising quality.
Quality Considerations and Control
I’ve found that while higher power can be a game-changer, it also requires meticulous attention to quality control. There was this one time when everything seemed perfect until I discovered tiny cracks in the weld—a sign that I hadn’t managed the increased power correctly. Real-time monitoring systems have become my best friend, allowing me to adjust parameters as needed.
While higher power outputs offer advantages, they also necessitate stringent quality control measures. The risk of defects like porosity or cracking increases with elevated power if not managed correctly.
Understanding how different materials react to heat has also been crucial. I recall working with aluminum and being surprised at how easily it oxidized under high power. Materials like titanium need their unique adjustments in power to avoid problems like embrittlement.
With today’s adaptive control technologies, it’s easier than ever to fine-tune power settings dynamically, ensuring optimal performance4 across different applications and materials. In my journey, these insights have transformed my approach to laser welding, making each project not just a task but an exploration.
Higher power leads to deeper weld penetration.True
Higher power levels enable deeper penetration, essential for welding thicker materials.
Excessive power always improves welding quality.False
Excessive power can cause issues like burn-through or excessive melt pool in thin materials.
Why is material compatibility crucial in choosing a machine?
Ever wondered why your machine seems to fight against you rather than work with you? Let me tell you, material compatibility might just be the unsung hero or villain in your workshop tale.
Material compatibility ensures a machine can handle specific materials effectively, preventing damage and inefficiencies. It’s crucial for optimal performance, safety, and cost-efficiency in manufacturing, much like finding the right dance partner who matches your rhythm perfectly.
Understanding Material Compatibility
When I first started working with machines, I remember thinking that they were like people—each one had its quirks and needed the right match to perform at their best. Material compatibility is just that; it’s about ensuring that your machine and materials are a perfect pair. Imagine trying to weld aluminum with a laser welding machine5 designed for stainless steel; it’s like forcing a square peg into a round hole—frustrating and ineffective.
Importance in CNC Machines
Take CNC machines, for instance. These marvels of precision engineering need to be matched with the right materials to deliver those crisp, clean cuts we all love. I recall an instance when I tried using a cutter meant for wood on metal. The result? A mess of splintered metal and a tool that wore out faster than you can say "incompatible." Using compatible tools ensures precision and efficiency6 and extends the life of your equipment.
Factors to Consider
- Thermal Properties: Ever tried to bake without preheating the oven? Machines need to match thermal properties with materials to avoid overheating or warping.
- Chemical Resistance: Just like you wouldn’t pair vinegar with soda, some materials can corrode machine parts if they’re not compatible.
- Mechanical Strength: Think of it as ensuring your machine is strong enough to handle the tough stuff without breaking down.
Real-World Examples
Consider using a fiber laser welder7 on carbon steel—it’s a dream. But switch that steel for copper, and suddenly, it’s a nightmare. Copper’s high thermal conductivity means energy is lost rather than used effectively, causing potential damage to your machine.
Material | Compatible Machine | Key Considerations |
---|---|---|
Aluminum | Fiber Laser Welder | Thermal conductivity |
Stainless Steel | CNC Milling Machine | Tool hardness |
Copper | CO2 Laser Cutter | Energy absorption rates |
Understanding material compatibility is like knowing the secret ingredient in your favorite dish—it makes all the difference. For workshops keen on optimizing their processes, this knowledge can prevent costly inefficiencies and potential equipment failures8.
CNC machines are compatible with all materials.False
CNC machines have specific material compatibilities, affecting precision and wear.
Material compatibility affects machine lifespan.True
Using incompatible materials can cause excessive wear, reducing machine lifespan.
Are There Budget-Friendly Options for High-Quality Laser Welders?
I remember the first time I searched for a laser welder, feeling daunted by the price tags. You’re not alone in wanting quality without a hefty bill. Let’s dig into affordable options that don’t skimp on excellence.
Yes, budget-friendly high-quality laser welders exist, perfect for small workshops and hobbyists. Brands like STYLECNC and Royell offer entry-level models balancing affordability and performance, ideal for beginners and small operations.
Understanding the Basics of Laser Welding
Laser welding might sound like something out of a sci-fi movie, but it’s a solid reality in today’s manufacturing world. I learned about its precision and strength during my early days tinkering with metal projects. It uses a laser to fuse materials, usually metals, by delivering intense heat9 to a tiny area, ensuring neat and strong joints. Despite its reputation for being costly, technological advancements have thankfully brought it within reach for smaller setups.
Entry-Level Options
I know what it’s like to hunt for tools that fit both your needs and budget. If you’re in the same boat, consider these entry-level models that I’ve found particularly promising:
Model | Power Output | Features | Price |
---|---|---|---|
STYLECNC 1000W | 1000W | Handheld, Portable | Around $4,600 |
Royell Handheld | 1000W-2000W | Versatile, Ergonomic | Varies |
These models are excellent starting points for small workshops10 needing reliability without the overwhelming cost.
Key Factors in Choosing a Budget-Friendly Welder
When I was choosing my first welder, I learned a few crucial things to consider:
- Power Output: Opt for machines with power outputs between 1000W and 1500W. This range provides enough oomph for most tasks while keeping costs down.
- Multi-functionality: Machines that also offer cutting and cleaning functions can be real game-changers, maximizing your investment.
- Material Compatibility: Ensure the welder can handle materials you frequently work with, like stainless steel or aluminum.
- Support and Service: Brands offering comprehensive technical support11 make life easier when setting up or troubleshooting.
Brands to Consider
- STYLECNC: Their user-friendly designs are perfect for beginners dipping their toes into laser welding.
- Royell: Known for precision and versatility, with strong technical support to back you up.
Finding the right model means balancing upfront costs with long-term savings on maintenance and repairs. With careful consideration of your specific needs, you can snag a laser welder that fits your budget without sacrificing quality.
Laser welding is traditionally expensive.True
Historically, laser welding technology required high initial investment, limiting access.
STYLECNC models are not suitable for beginners.False
STYLECNC is known for user-friendly designs ideal for beginners.
Conclusion
Discover the best handheld laser welding machines for small workshops, focusing on models like Ironsten XING and ZAC 1500W that balance power, versatility, and affordability.
-
Understand how to align costs with long-term business goals and financial planning by evaluating entry-level and advanced models. ↩
-
Learn techniques to balance power and material thickness for optimal welding outcomes. ↩
-
Discover strategies to enhance welding speed and efficiency without sacrificing quality. ↩
-
Explore how adaptive control technologies improve laser welding performance and quality. ↩
-
Learn about laser welding applications to ensure you’re using it effectively in your workshop. ↩
-
Understand how material compatibility influences CNC machine precision to improve your manufacturing quality. ↩
-
Discover best practices for using fiber laser welders to enhance your welding processes. ↩
-
Find out how material incompatibility can lead to equipment failures to prevent costly breakdowns. ↩
-
Understanding the fundamentals of laser welding can help you make informed decisions about equipment choices. ↩
-
Exploring recommendations specific to small workshops ensures you find a model tailored to your needs. ↩
-
Having access to technical support can significantly ease the setup and maintenance process. ↩