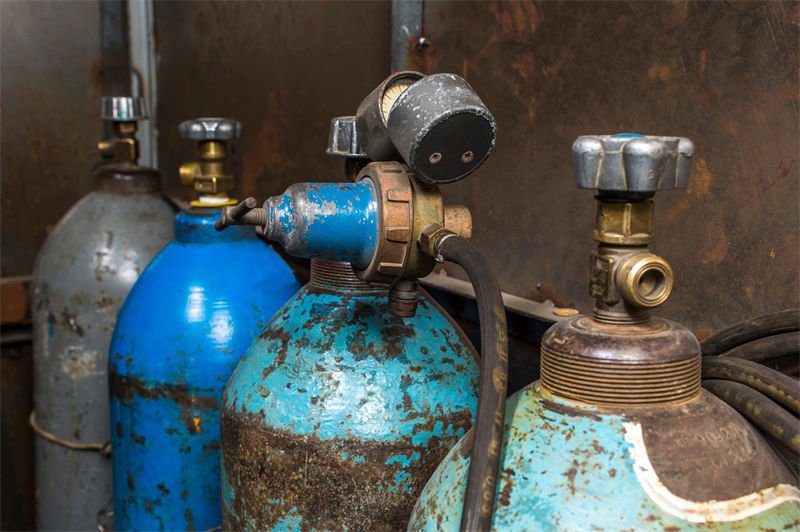
Ever tried fixing something at home and realized you had the wrong tool? That’s what choosing the wrong gas for plasma CNC cutting feels like.
To pick the right gas for plasma CNC cutting, start by matching it to the material: compressed air for versatility, nitrogen for smooth stainless steel cuts, oxygen for quick carbon steel slices, and argon-hydrogen for tackling thick stainless steel and aluminum.
When I first started with CNC cutting, I was overwhelmed by the sheer number of choices. It’s not just about getting the job done; it’s about doing it well. Picking the right gas can be daunting, but it’s essential for achieving that perfect edge finish. Consider factors like cost, the quality of the cut edges, and the specific needs of the material you’re working with. Dive into the details, and you’ll find the perfect balance that works for you.
Compressed air is suitable for cutting aluminum.False
Compressed air is versatile but not ideal for aluminum; argon-hydrogen is better.
Oxygen speeds up cutting on carbon steel.True
Oxygen enhances cutting speed and efficiency on carbon steel due to its reactivity.
What Factors Should Influence Your Gas Choice?
Choosing the right gas for your CNC operations isn’t just a technical decision—it’s personal. Let’s dive into how the right choice can transform your work.
Selecting the right gas depends on the material type, desired cut quality, and cost. Compressed air is versatile; nitrogen offers high-quality cuts; oxygen suits fast cuts on carbon steel; argon-hydrogen is ideal for thick materials.
Material Type and Suitability
When it comes to choosing the right gas for my CNC operations, I’ve learned that it’s much more than just a technical decision—it’s a bit like choosing the perfect tool for a job, or even the right seasoning for a dish. Each option has its own unique flavor and impact on the final product.
Over the years, I’ve found that understanding the material I’m working with is crucial. For instance, compressed air is my go-to for mild steel1 because it’s so versatile. But when I’m dealing with stainless steel or aluminum, nitrogen never lets me down—it’s like having an ace up my sleeve.
Gas Type | Material Suitability |
---|---|
Compressed Air | Mild Steel, Aluminum, Stainless Steel |
Nitrogen | Stainless Steel, Aluminum |
Oxygen | Carbon Steel |
Argon-Hydrogen | Thick Stainless Steel, Aluminum |
Desired Cut Quality
The pursuit of the perfect edge is one that resonates deeply with me. Oxygen might offer fast cuts with squared edges, but it often leaves an oxidized finish that doesn’t always meet my standards. On the other hand, nitrogen provides those clean edges that make me proud of my work, especially when quality is non-negotiable.
Cost Considerations
Cost is always on my mind. Compressed air is economical and easy to source, but it does have its drawbacks, like sometimes needing extra post-processing2. For those premium jobs where precision is key, I don’t mind shelling out a bit more for argon-hydrogen—it’s worth every penny when it comes to edge perfection.
Gas Type | Pros | Cons |
---|---|---|
Compressed Air | Economical, easily available | May require extra processing |
Nitrogen | High-quality cuts, minimal oxidation | More expensive, requires good supply |
Oxygen | Fast cutting speeds | Causes edge oxidation |
Argon-Hydrogen | Smooth cuts on thick materials | High cost |
Environmental Impact and Safety
Finally, safety and the environment are things I can’t ignore. Using compressed air might be light on the wallet, but in humid conditions, I’ve learned that investing in air dryers3 can make a big difference in maintaining cut quality. And when handling gases like oxygen and hydrogen, I always follow safety regulations to ensure everyone goes home safe.
Choosing the right gas isn’t just about the immediate task—it’s about setting myself up for success both in terms of quality and safety. It’s a decision that impacts everything from cost-efficiency to the final product’s integrity.
Nitrogen is ideal for cutting mild steel.False
Nitrogen is best for stainless steel and aluminum, not mild steel.
Compressed air is the most economical gas choice.True
Compressed air is cost-effective and widely available, making it economical.
How Does Each Gas Impact Edge Quality and Finish?
When it comes to CNC plasma cutting, picking the right gas can feel like choosing the perfect spice for your favorite dish. Each one brings out unique flavors—or in this case, effects on edge quality and finish.
In CNC plasma cutting, each gas—compressed air, nitrogen, oxygen, and argon-hydrogen mixtures—impacts edge quality differently. Compressed air is versatile but can oxidize; nitrogen offers clean cuts; oxygen is fast but may oxidize; and argon-hydrogen excels with smooth cuts on thick materials.
Compressed Air: Cost-Effective Versatility
Let me tell you about the time I decided to tackle a project with good old compressed air. It’s like the multi-tool in my workshop—always reliable and ready to get the job done on mild steel, aluminum, and stainless steel. However, those oxidized edges it left behind reminded me of the times I tried to cut corners on sanding after a woodworking project. It does the trick for basic jobs, but if you’re looking for a pristine finish, you might need to go the extra mile with some post-processing.
Pros: Budget-friendly, easy setup.
Cons: Might need some elbow grease for post-processing4.
Nitrogen: Clean Cuts with Precision
I remember when I first used nitrogen, it felt like discovering a new favorite coffee blend—smooth, rich, and just right. Especially on stainless steel and aluminum, the cuts were crisp with barely any oxidation. It’s no wonder industries that prioritize aesthetics lean towards nitrogen. Just like that premium coffee, though, it comes at a higher price point.
Material | Pros | Cons |
---|---|---|
Stainless Steel | Clean edges | Higher cost |
Aluminum | High speed | Requires reliable supply |
Oxygen: Fast and Efficient
Using oxygen is like shifting into high gear on an open road. The speed at which it slices through carbon steel is impressive. But much like driving fast can wear your tires quicker, oxygen’s oxidation can leave the edges needing some TLC if they’re destined for certain applications.
Argon-Hydrogen Mixtures: Smooth Excellence
Whenever I have to cut through thick stainless steel or aluminum, I turn to argon-hydrogen mixtures. It’s like having that expert chef at a barbecue who knows exactly how to get those ribs just right—smooth, minimal dross, and worth every penny for challenging cuts.
Material Suitability: Great for thick sections.
Handling: Needs specialized equipment6.
Analyzing Cost vs. Quality
Finding the sweet spot between cost and edge quality can be a bit like balancing a seesaw. While compressed air holds its own for basic projects, sometimes you just need that extra finesse that nitrogen or argon-hydrogen brings to the table. Depending on what you’re cutting and its final purpose, a hybrid approach7 might just be the ticket to optimizing both cost and quality.
Compressed air is the most cost-effective gas for cutting.True
Compressed air is affordable and widely available, making it cost-effective.
Nitrogen cuts are slower than oxygen cuts on carbon steel.True
Oxygen cuts carbon steel quickly, while nitrogen focuses on precision.
What Are the Cost Implications of Different Gases?
Ever wondered how the choice of gas impacts your budget and the environment?
The cost implications of different gases vary based on factors like availability, market demand, production costs, and geopolitical influences. Understanding these elements can help you make informed decisions about which gas is most economical and environmentally sound for your needs.
Availability and Market Demand
Picture this: you’re in a bustling market, and suddenly there’s a rush on apples because everyone’s making pies for a festival. Prices shoot up! It’s similar with gases. Natural gas8 tends to be cheaper because it’s widely available and has an established distribution network. But like those apples, if demand surges unexpectedly, prices can skyrocket.
Production Costs
Think of hydrogen as that fancy dessert you love but rarely indulge in because it’s a labor of love to make. Its production is energy-intensive, which hikes up the cost. On the other hand, methane is more like your everyday bread—easier and cheaper to produce because it comes from natural sources. Understanding these production processes9 can help anticipate potential price changes.
Geopolitical Influences
Remember those tense times when world news felt like a rollercoaster? Well, geopolitical stability—or the lack thereof—can send gas prices on a wild ride too. Take the Middle East; any tension there can ripple across global oil and gas prices. Monitoring geopolitical trends10 helps in predicting price shifts.
Environmental Regulations
Governments are stepping up their game to protect our planet, imposing strict environmental laws. These regulations mean higher production costs for gas companies, which trickle down to us, the consumers. Staying updated on these regulations11 can help you plan your budget better.
Gas Type | Typical Use | Cost Factors |
---|---|---|
Natural Gas | Heating and electricity | Supply chain efficiency |
Hydrogen | Fuel cells | Production energy costs |
Propane | Residential heating | Extraction and transport costs |
Oxygen | Industrial applications | Purity requirements |
Understanding these cost implications lets you make smarter choices, whether you’re adjusting business operations or keeping an eye on personal expenses. It’s all about finding that balance between cost, efficiency, and impact.
Natural gas is often cheaper due to its abundance.True
Natural gas is abundant and has extensive distribution networks, reducing costs.
Stricter environmental laws decrease gas production costs.False
Stricter laws increase compliance costs, which are often passed to consumers.
How do I stay safe while using plasma cutting gases?
Ever found yourself in a whirlwind of sparks and metal, wondering about the best way to handle those plasma cutting gases safely?
To ensure safety with plasma cutting gases, always ensure proper ventilation, wear suitable personal protective equipment (PPE), inspect for leaks regularly, and adhere to manufacturer guidelines.
Understanding Plasma Cutting Gases
I remember the first time I watched a skilled technician cut through metal with a plasma cutter. It was like watching magic—fireworks of sparks and precision. Plasma cutting uses a superheated jet of ionized gas to slice through metal, and the gases involved—compressed air, nitrogen, oxygen, and argon-hydrogen mixtures—each have unique properties that call for specific safety measures12.
Personal Protective Equipment (PPE)
Once, I forgot my gloves during a quick cut and ended up with a nasty burn. Lesson learned: never skip on PPE. Flame-resistant clothing, safety glasses, and gloves are must-haves. If you’re working in a less ventilated area, a respirator might save you from inhaling harmful fumes. Make sure all your gear meets industry standards13.
PPE Type | Purpose |
---|---|
Flame-resistant | Protects against burns |
Safety glasses | Shields eyes from sparks |
Gloves | Prevents cuts and burns |
Respirator | Filters harmful fumes |
Ensuring Proper Ventilation
There’s nothing worse than working in a cloud of fumes. Good ventilation is key to dissipating those gases. Use local exhaust systems or make sure you’re in a well-ventilated space. Cutting in confined spaces without adequate ventilation14 can be risky.
Regular Equipment Inspections
I make it a point to inspect all hoses and connections before getting started. A leak could mean gas buildup, which is dangerous. A trick I picked up is using a soapy water solution to check for leaks15—watch for bubbles at potential leak points.
Following Manufacturer Guidelines
Adhering to the manufacturer’s guidelines isn’t just bureaucratic; it’s about safety and efficiency. Incorrect settings can lead to poor cuts or accidents. I always double-check the recommended gas pressures and flow rates to avoid unnecessary risk16.
By staying proactive about safety, we can minimize the risks that come with plasma cutting gases, ensuring not just a safer work environment but also peace of mind for everyone involved.
Compressed air is the only gas used in plasma cutting.False
Plasma cutting uses various gases like nitrogen, oxygen, and argon-hydrogen.
Regular equipment inspections prevent gas buildup risks.True
Inspecting hoses and connections for leaks prevents dangerous gas accumulation.
Conclusion
Selecting the right gas for plasma CNC cutting depends on material type: compressed air for versatility, nitrogen for stainless steel, oxygen for carbon steel, and argon-hydrogen for thick materials.
-
Explore various gas options suitable for cutting mild steel to enhance your operations. ↩
-
Learn effective post-processing techniques to improve oxidized metal edges. ↩
-
Discover how air dryers impact CNC cutting in humid conditions. ↩
-
Explore techniques to treat oxidized edges left by compressed air cutting for a refined finish. ↩
-
Learn how oxidation from oxygen cutting affects welding processes and how to mitigate it. ↩
-
Discover what specialized equipment is necessary for safely using argon-hydrogen mixtures. ↩
-
Uncover strategies for using multiple gases in CNC cutting to enhance both cost-efficiency and quality. ↩
-
Natural gas is a common fuel source with fluctuating prices; understanding current trends aids in budgeting. ↩
-
Knowing how hydrogen is produced reveals why it’s costlier, aiding in decision-making for industrial applications. ↩
-
Geopolitical events can disrupt supply chains, causing price fluctuations; staying informed helps mitigate risks. ↩
-
Environmental laws impact production costs; understanding them aids compliance and budgeting. ↩
-
Discover how each plasma gas type demands specific safety measures to ensure proper handling and operation. ↩
-
Learn about the essential standards for PPE to ensure maximum protection during plasma cutting tasks. ↩
-
Explore the best practices for ventilating workspaces during metal fabrication to prevent inhalation of harmful fumes. ↩
-
Find out effective methods for detecting gas leaks in industrial equipment to prevent accidents. ↩
-
Gain insights into why following manufacturer guidelines is crucial for safe and efficient plasma cutting operations. ↩