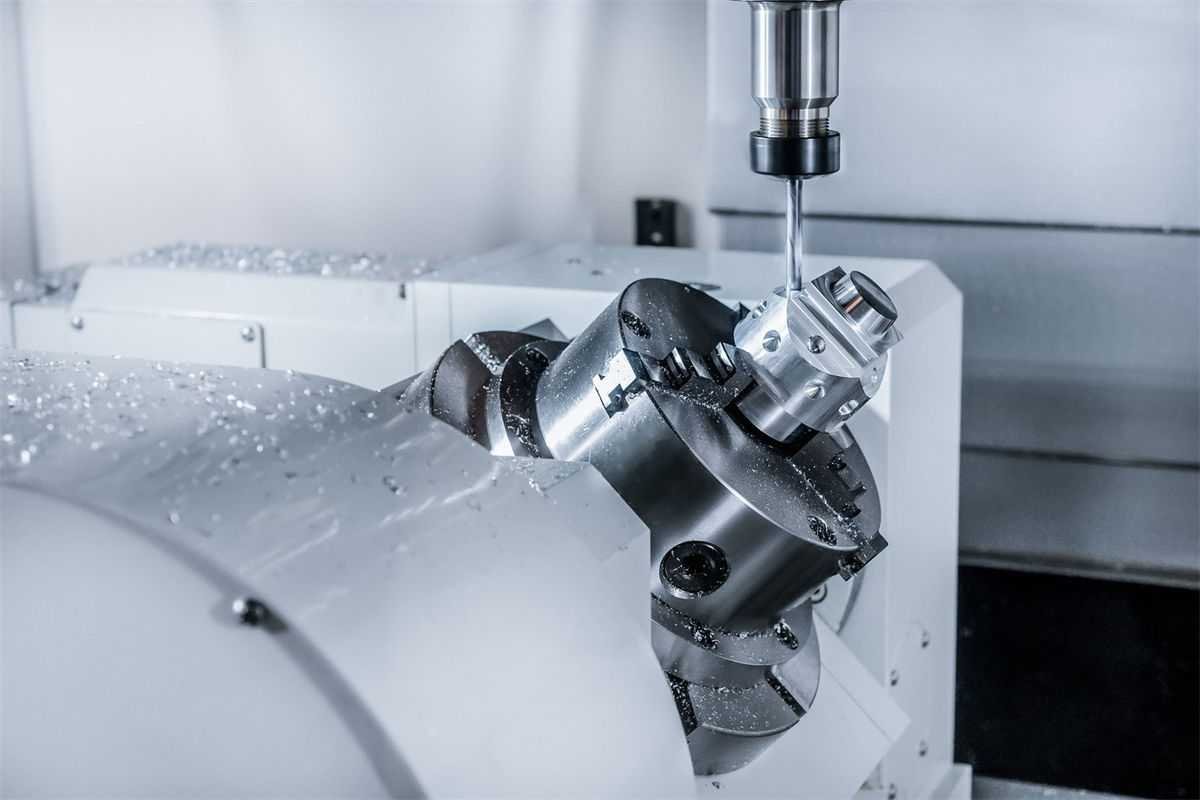
Buying a CNC mill? You’re not alone—many find it daunting! Let’s simplify this journey together.
Key factors to consider before buying a CNC mill include machining requirements, machine performance parameters, control system capabilities, cost budgets, and after-sales support. These elements ensure the machine meets your project needs and financial constraints.
While this overview provides a quick answer, delving deeper into each aspect will arm you with the knowledge to make a confident and informed investment. Continue reading to uncover detailed insights into each factor’s importance.
CNC mills with ATC improve multi-process efficiency.True
Automatic tool changers allow seamless transition between processes, boosting efficiency.
How Do Machining Requirements Influence CNC Mill Selection?
Selecting the right CNC mill is critical to meeting your machining needs. Understanding these requirements can significantly influence your choice.
Machining requirements dictate the selection of CNC mills by determining the workpiece size, precision levels, and types of machining processes needed. These requirements ensure that the chosen mill can handle specific project demands efficiently.
Understanding Workpiece Dimensions and Types
The dimensions and types of workpieces you plan to machine are fundamental in CNC mill selection. Large mechanical parts necessitate machines with substantial worktables and higher load capacities, while smaller precision parts require precise control systems.
For instance, machining large aerospace components1 demands a CNC mill with an expansive worktable, long travel distances on the X, Y, and Z axes, and robust load-bearing capabilities. Conversely, for small precision parts or complex geometries, such as those in medical device manufacturing, a machine with high positioning accuracy is imperative.
Precision Requirements and Expectations
Precision is paramount in CNC machining. The level of dimensional precision (tolerance control) and shape precision (flatness, cylindricity) required for your projects influences your machine choice. High-precision tasks often necessitate CNC mills with advanced positioning precision and repeatability metrics.
For example, achieving a tolerance within ±0.01mm may require a premium CNC mill with enhanced precision features, which subsequently affects budget considerations.
Types of Machining Processes Needed
Determine whether your operations require simple milling or involve additional processes like drilling, reaming, and tapping. A comprehensive understanding of these needs can guide the selection towards mills equipped with automatic tool changers (ATC) and versatile tool systems.
A typical scenario could involve a production line requiring multiple machining processes—choosing a mill with an ATC and a sophisticated tool management system can streamline operations and improve efficiency.
Balancing Requirements with Cost
Balancing your machining requirements with financial constraints is crucial. High-performance features that cater to specific needs often come at a premium. Consider both initial purchase costs and long-term operational expenses like maintenance, electricity, and tooling when selecting a machine.
In summary, aligning your CNC mill selection with detailed machining requirements ensures that the machine meets project specifications efficiently. This alignment not only enhances productivity but also maximizes return on investment over the machine’s lifecycle.
CNC mills with ATC are ideal for complex processes.True
Automatic tool changers streamline operations by handling multiple processes.
Large workpieces require CNC mills with small worktables.False
Large workpieces need mills with expansive worktables for support.
What Performance Parameters Are Crucial in a CNC Mill?
The performance parameters of a CNC mill are critical for ensuring precision, efficiency, and adaptability in machining tasks. Understanding these parameters can significantly impact the success of your projects.
Crucial performance parameters in a CNC mill include spindle speed and power, feed system capabilities, precision indicators, and control system compatibility. These factors determine the machine’s efficiency, accuracy, and suitability for specific materials and processes.
Spindle Parameters: Speed and Power
The spindle is the heart of a CNC mill, dictating its ability to cut materials effectively. Spindle speed, typically measured in revolutions per minute (RPM), must match the material being machined. For instance, aluminum machining2 requires higher speeds compared to steel.
Spindle power is another critical factor, influencing the cutting capacity. Machines with higher power can perform more intensive cuts, making them suitable for thicker materials or tougher jobs. Assessing the spindle power required for your projects can prevent costly miscalculations.
Feed System Capabilities
The feed system involves how the material is moved through the machine. Feed speed impacts both the efficiency and surface quality of the finished product. Machines with a broad feed speed range offer greater flexibility across different tasks.
Feed drive methods, such as ball screw or linear motor drives, affect precision and cost. Ball screws offer high precision at a lower cost, while linear motors provide faster speeds and better position control but at a higher expense.
Precision Indicators
Precision is paramount in CNC milling. Positioning precision and repeat positioning precision determine how accurately the machine can follow programmed paths. High precision is essential for industries requiring exact tolerances, like aerospace or medical equipment manufacturing.
Control System Compatibility
The choice of CNC control systems can impact operational efficiency and ease of use. Systems like FANUC3 or Siemens offer varying features, interfaces, and programming methods. Selecting a system compatible with your operators’ skills and production requirements can enhance productivity.
Consideration of Machining Processes
Understanding the types of machining processes required—such as milling, drilling, or tapping—can dictate the need for additional features like automatic tool changers (ATC). This capability enables the machine to perform multiple operations without manual intervention, increasing throughput and reducing errors.
Spindle speed affects CNC mill precision.True
Spindle speed must match material for precision, impacting cut quality.
Higher spindle power means lower cutting capacity.False
Higher spindle power increases cutting capacity, suitable for tough materials.
Why Is Understanding the Control System Important for CNC Mills?
Grasping the intricacies of CNC mill control systems is crucial for maximizing efficiency and precision in your machining projects.
Understanding CNC mill control systems is vital as they dictate machine operations, influence precision, and determine compatibility with software and external devices, ultimately impacting productivity and efficiency.
The Role of CNC Control Systems in Machine Operations
CNC control systems are the brain of a CNC mill, orchestrating every movement and function. They determine how the machine interprets machining instructions4 and carry out tasks with precision. A robust control system ensures that even the most complex designs are executed flawlessly, reducing errors and enhancing overall productivity.
Enhancing Precision and Efficiency
One of the core benefits of an advanced control system is the level of precision it offers. For instance, systems that support high-level programming features like spline interpolation can significantly improve the accuracy of intricate three-dimensional surfaces. Moreover, a reliable system optimizes operations by ensuring consistent speed and feed rates, which are crucial for maintaining surface finish quality5.
System Compatibility and Integration
A crucial aspect of any CNC control system is its compatibility with external software such as CAD/CAM. This compatibility enables seamless program transfers and real-time adjustments, enhancing workflow efficiency. Furthermore, integration capabilities with other automated devices, such as robotic arms for loading and unloading materials, can vastly improve production throughput6.
Types of CNC Systems: Choosing the Right Fit
There are various types of CNC systems available, each with unique features and interfaces. Popular systems like FANUC and Siemens offer different levels of customization and support. Selecting a system should consider operator familiarity, ease of use, and long-term support options from manufacturers. Opting for a system that aligns with your team’s skill set can minimize training costs7 and accelerate operational readiness.
Understanding these aspects of CNC control systems not only facilitates a smoother operation but also extends the longevity and reliability of your CNC milling equipment.
CNC control systems dictate machine operations.True
Control systems are central to how CNC machines function and execute tasks.
System compatibility doesn't affect CNC productivity.False
Compatibility with software and devices is crucial for efficient operations.
How Should You Evaluate Costs and After-Sales Support When Buying a CNC Mill?
Navigating the purchase of a CNC mill requires careful consideration of both costs and after-sales support. Balancing these elements is crucial for a sustainable investment.
Evaluate costs by considering the machine price, operating expenses, and training costs. For after-sales support, assess technical assistance, spare parts availability, and warranty policies. Together, these factors ensure long-term efficiency and reliability.
Evaluating Costs
When purchasing a CNC mill, understanding the full financial scope is essential. Start by examining the initial machine tool price, which varies based on brand, specifications, and performance. Opting for a reputable brand often ensures quality but at a higher cost. Balance this with your budget and the machine’s capabilities to avoid overspending or under-equipping your operations.
Next, consider operating costs. These include electricity consumption, especially if the machine boasts high spindle power, which directly affects energy bills. Also, factor in tool wear and coolant expenses, as frequent machining tasks will increase these costs.
Don’t overlook training costs. If your team lacks experience with CNC mills, investing in training is crucial. Evaluate whether internal training with experienced staff or external courses at professional institutions best suits your needs.
Analyzing After-Sales Support
A reliable after-sales support system can dramatically reduce downtime and enhance productivity. Key components include:
- Technical Support: Check if the manufacturer offers prompt technical assistance, either via phone consultations or on-site services. Quick troubleshooting can mitigate delays in production.
- Spare Parts Supply: Ensure the availability of spare parts throughout the machine’s lifespan. Delays in obtaining parts can prolong repair times, impacting operations significantly.
- Warranty Policy: Review the warranty terms, including duration and coverage. A comprehensive warranty reduces financial risk and ensures peace of mind.
To better understand how these elements integrate into your decision-making process, consider using a comparative table:
Aspect | Details |
---|---|
Machine Tool Price | Evaluate based on brand reputation and specifications. |
Operating Costs | Includes electricity, tool wear, and coolant expenses. |
Training Costs | Consider internal vs external training investments. |
Technical Support | Check for availability of timely assistance. |
Spare Parts Supply | Ensure easy accessibility throughout machine life. |
Warranty Policy | Review scope, duration, and conditions thoroughly. |
Evaluating these factors provides a comprehensive view of both initial and long-term investments required for a CNC mill. By focusing on both cost analysis and robust after-sales support, you ensure that your choice not only fits your current needs but also sustains future growth and productivity.
Reputable brands always offer better CNC mill quality.False
While often true, not all reputable brands guarantee superior quality.
Warranty terms affect the financial risk of a CNC mill purchase.True
Comprehensive warranties reduce financial risks by covering potential repairs.
Conclusion
Reflect on these essential factors to align your CNC mill choice with your unique needs for optimal productivity.
-
Discover specific needs for machining aerospace parts efficiently.: CNC machining for the aerospace industry requires high precision and attention to detail. Here are the benefits of the process and tips for … ↩
-
Discover optimal speeds for enhancing aluminum machining efficiency.: Currently running a spindle speed of 11k on a small diy machine. Can’t cut any deeper then . 2mm without chatter. ↩
-
Learn about FANUC system’s unique features for improved machining control.: FANUC CNCs are known for their rock-solid reliability and unbeatable performance. We have controls to meet all machining needs, from highly complex 5-axis … ↩
-
Explore how CNC instructions influence precision and machining outcomes.: One of the major CNC machining benefits is accuracy. Because CNC machines receive precise instructions from a computer — and the movements … ↩
-
Learn how control systems maintain high-quality surface finishes.: Employing vibration-dampening techniques like adaptive control systems or tuned mass dampers can further enhance surface finish quality. Another way to … ↩
-
Understand the benefits of integrating CNC mills with automation.: It facilitates the connection of your robot arm with various CNC or automation devices to interact with each other by using the drag-and-drop building blocks … ↩
-
Discover strategies to minimize CNC operator training expenses.: Documenting your company’s policies and procedures can save considerable time and money. ↩