CNC Plasma cutting machines
Unlock the power of precision and performance with our CNC Plasma Cutting Machines. Whether you need a cnc plasma cutter for industrial use or a hobby cnc plasma cutting machine for DIY projects, we have the right solution. Explore our range from cnc plasma cutter tables to cnc plasma cutter portable models, ensuring versatility for any workspace. For complex tasks, our cnc plasma tube cutting machines provide cutting-edge technology to handle specialized requirements. If you’re a DIY enthusiast, our diy cnc plasma cutting table kits are perfect for building your own system. Get ready to elevate your cutting experience with reliable and cost-effective options, designed for businesses of all sizes.
Product Showcase
In our Product Showcase, you’ll find a diverse range of CNC plasma cutting machines to meet various needs. From robust cnc plasma cutter systems for large industrial tasks to compact and versatile options like the cnc plasma cutter portable and cnc plasma cutter small, we’ve got you covered. For specialized tube cutting, our cnc plasma tube cutting machine delivers precision and efficiency. Whether you’re looking for a 3D plasma cutter or a machine for cnc plasma cutting aluminum, we have the perfect solution. DIY enthusiasts will love our diy cnc plasma cutting table kits and diy cnc plasma cutter options, allowing you to build your own cutting platform. From hobby cnc plasma cutting machines to affordable cnc plasma cutters, our products cater to all levels, ensuring exceptional performance for cnc plasma cutting metal tasks.
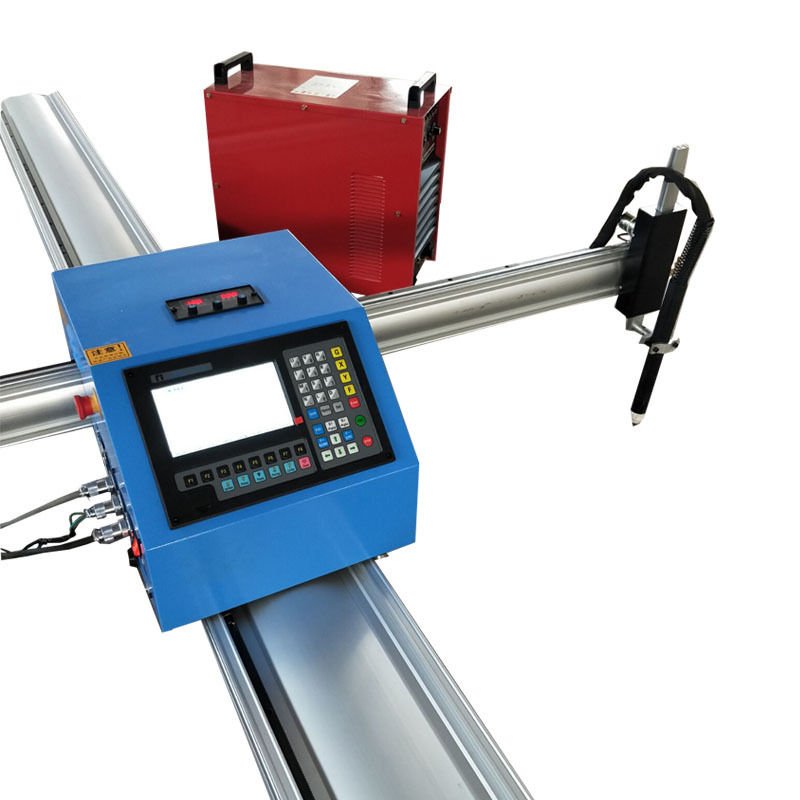
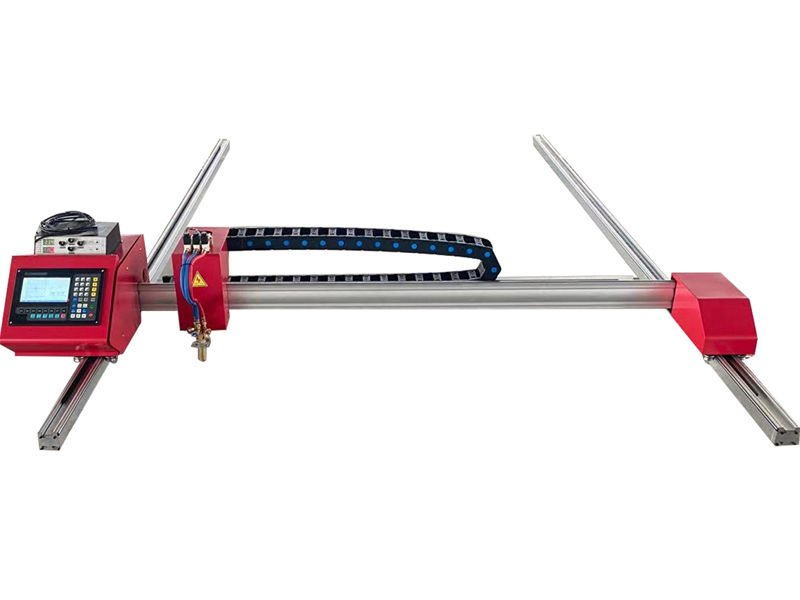
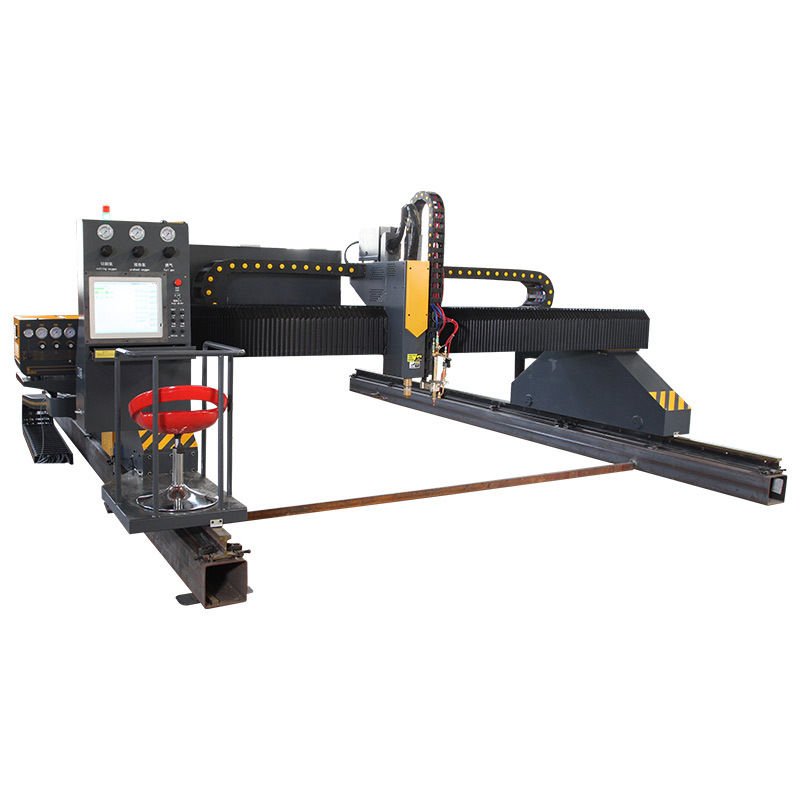

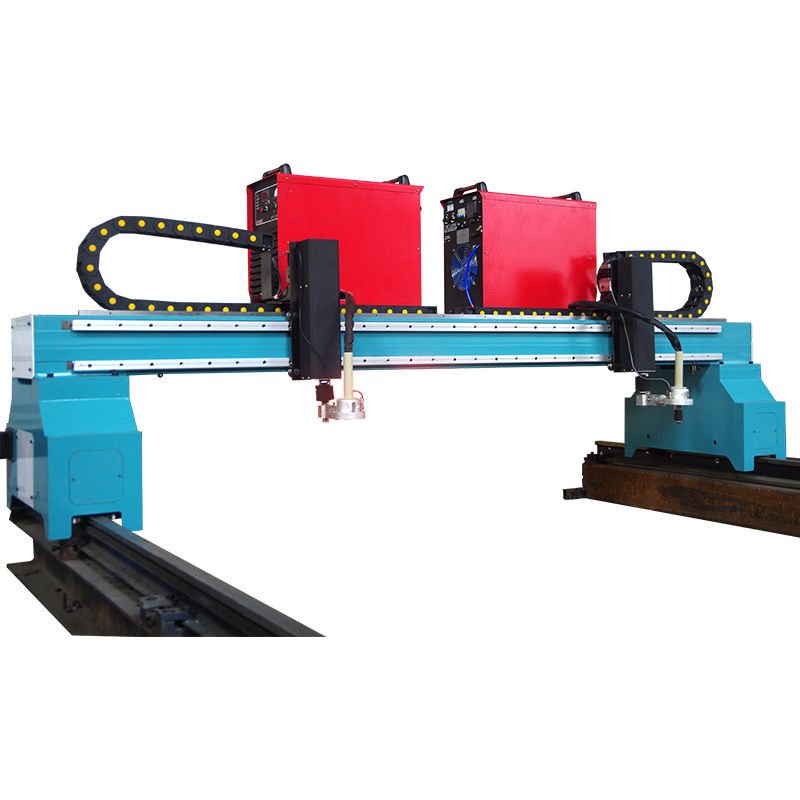


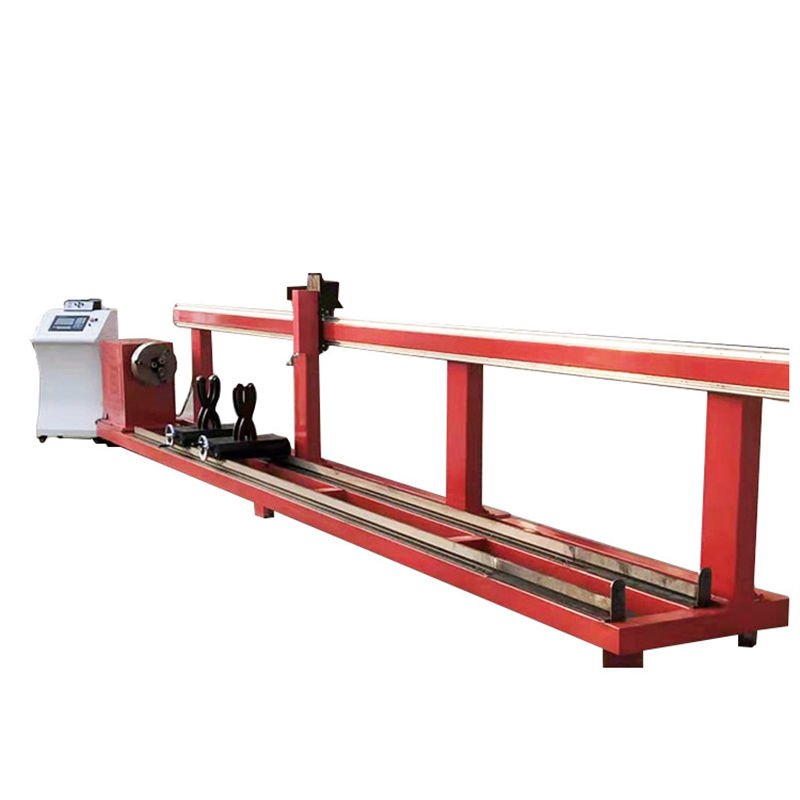
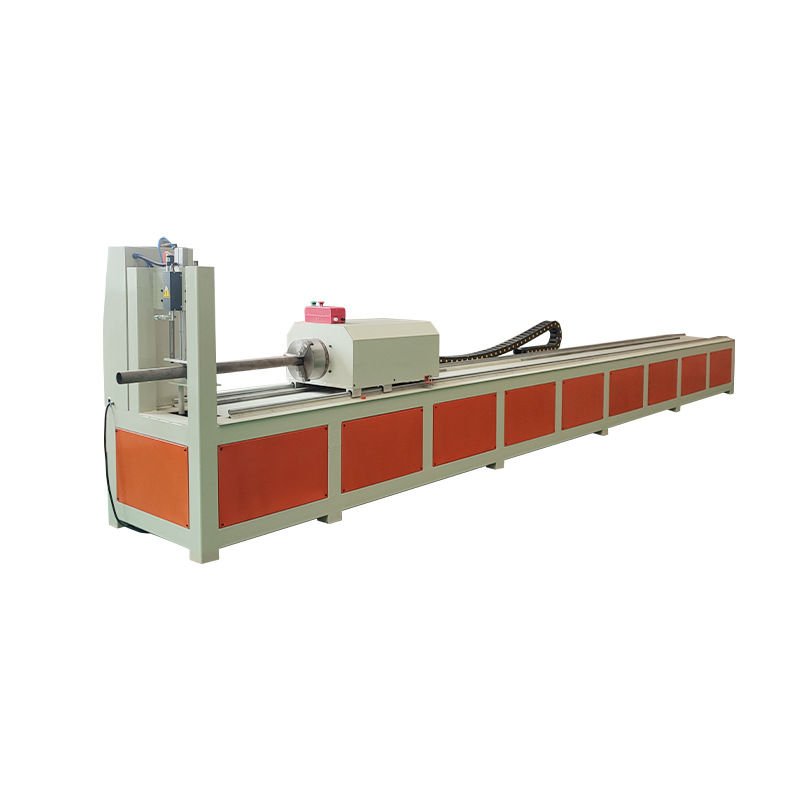
Still not finding what you're looking for? Contact our consultants for more available products.
Features of Our CNC Plasma Cutting Machines
Comprehensive Equipment Protection
Our CNC plasma cutting machines are equipped with advanced protection systems, ensuring reliable and stable operation in even the most demanding environments. Whether you’re using a cnc plasma cutter table, cnc plasma cutter portable, or cnc plasma cutter small, our machines are built to maintain peak performance for long-term use.
Exceptional Durability
Built from premium materials, our affordable CNC plasma cutters are designed to withstand intensive use and high mechanical stress. They provide consistent performance on a wide range of metals, including aluminum and steel, reducing the need for frequent repairs or maintenance.
Versatile Applications
Our CNC plasma cutting machines offer versatility for various applications. From intricate cuts on cnc plasma cutting aluminum to complex tasks with a cnc plasma tube cutting machine, our equipment is perfect for both industrial users and DIY enthusiasts. Whether you’re using a hobby CNC plasma cutting machine or a larger cnc plasma cutter system, our machines provide the precision you need to tackle any project.
Optimized Performance
Engineered for speed and precision, our CNC plasma cutting machines ensure optimized cutting performance on various metal types. With advanced control systems, our machines allow for fast, accurate cuts, helping you improve productivity while delivering high-quality results every time.
Easy Installation and Maintenance
Designed with user-friendliness in mind, our CNC plasma cutters are easy to install and maintain. The modular design enables quick part replacements and upgrades, minimizing downtime. Whether you’re using a diy cnc plasma cutter or a larger industrial model, keeping your machine running smoothly is simple and straightforward.
Cost-Effective Solutions
Our CNC plasma cutting machines deliver high performance at competitive prices. From affordable CNC plasma cutters for personal projects to powerful machines for professional use, we provide cost-effective solutions that combine quality and efficiency for businesses of all sizes.
I.what are plasma cutters used for?
Plasma cutters are widely used for cutting conductive materials, primarily metals, by utilizing a high-velocity jet of ionized gas (plasma) to melt and slice through the material with precision and speed. They are commonly employed in metal fabrication industries such as automotive, aerospace, and shipbuilding, where they are used to cut steel, aluminum, and other metals. In the construction sector, plasma cutters are essential for cutting structural steel, pipes, and metal sheets. Manufacturing industries rely on them for producing machinery, equipment, and metal components, while maintenance and repair shops use plasma cutters to cut and customize metal parts for various applications.
Plasma cutters are also popular in the art and sculpture world, where artists use them to create detailed metal artwork and intricate designs. Additionally, in DIY and hobby projects, plasma cutters are an ideal tool for home-based metalworking, allowing hobbyists to work on a variety of custom tasks. Their ability to make precise and intricate cuts on both thick and thin materials makes plasma cutters indispensable across many industries.
II.will plasma cutter cut aluminum?
Yes, a plasma cutter can cut aluminum. Plasma cutters are capable of cutting various conductive metals, and aluminum is one of them. Due to aluminum’s high thermal conductivity, it can sometimes be more challenging to cut compared to steel, but modern plasma cutters handle aluminum effectively by adjusting the cutting speed and power settings. Plasma cutters are widely used in industries for cutting aluminum sheets, plates, and other components with precision and efficiency.
III.will a plasma cutter cut cast iron?
Yes, a plasma cutter can cut cast iron. Plasma cutting works on any conductive material, and cast iron is no exception. However, cast iron is more brittle and dense than other metals like steel, so cutting it may produce rougher edges or more slag. Despite this, modern plasma cutters, with proper settings, can effectively cut through cast iron, making it a useful tool for metalworking projects involving this material.
IV.how many watts does a plasma cutter use?
The power consumption of a plasma cutter depends on its model, usage, and the thickness of the material being cut. Typically, plasma cutters can consume anywhere between 3 kW to 20 kW or more, with several factors influencing the exact power usage.
Small, portable plasma cutters: These are designed for light-duty tasks, such as cutting thin metal sheets, and are often used in home workshops or small businesses. The power consumption for these machines usually ranges from 3,000 to 6,000 watts (3-6 kW). They are energy-efficient and well-suited for tasks that don’t require heavy power, such as cutting aluminum or stainless steel sheets.
Medium-sized plasma cutters: These machines are more powerful, designed to cut medium-thickness metals, and are commonly used in construction or mid-sized manufacturing facilities. Their power consumption can range from 6 kW to 10 kW, offering a balance between power and precision. They handle thicker materials while maintaining reasonable energy usage and cutting speed.
Large industrial plasma cutters: Designed for heavy-duty, industrial applications, these machines are used for cutting thick materials like steel plates and cast iron. The power usage for these systems typically ranges between 10,000 to 20,000 watts (10-20 kW) or higher. Industrial plasma cutters are built for continuous, high-intensity operations, ensuring high performance and durability over long periods of use.
Several factors influence the actual power consumption of a plasma cutter:
- Material thickness: Thicker materials require more power to ensure smooth and efficient cutting. For instance, cutting through thick steel or cast iron will consume more power than cutting thin aluminum sheets.
- Cutting amperage and voltage: The higher the cutting amperage, the more power the plasma cutter will consume. Adjusting the voltage settings for different tasks also affects overall power usage.
- Duty cycle: A plasma cutter’s duty cycle refers to the percentage of time it can operate at maximum power within a given timeframe. Machines with a higher duty cycle are designed for longer, more intensive use, which increases energy consumption during extended operations.
- Operation time and frequency: The longer and more frequently the machine is used, the higher its overall energy consumption. In industrial settings where plasma cutters are used continuously, power usage will naturally be greater.
Overall, the power consumption of a plasma cutter varies widely depending on its application. Selecting the right machine with appropriate power capacity ensures not only efficiency and performance but also reduces unnecessary energy costs.
V.how much does plasma cutting cost?
The cost of plasma cutting is influenced by several factors, including material thickness, machine power, consumables, electricity, and labor. First, consumables like electrodes, nozzles, and shields need regular replacement, and the cost for these can range from $1 to $5 per hour, depending on the type of machine and the quality of the consumables. In heavy industrial use, these costs may increase due to faster wear.
Next, electricity costs contribute significantly. Smaller plasma cutters, typically consuming between 3 to 6 kW, can cost around $0.50 to $1.50 per hour to operate, assuming an electricity rate of $0.10 per kWh. For larger, industrial-grade machines with power consumption of 10 to 20 kW, electricity costs can rise to $1 to $2.50 per hour or more for continuous operation.
Labor costs are another critical component, especially in industrial settings. Skilled operators are needed to ensure precision and proper machine maintenance. Depending on the region and complexity of the work, labor costs can range from $20 to $50 per hour or more, particularly for custom or intricate cutting tasks.
In addition, the material cost plays a role. Cutting thicker or harder materials like steel or stainless steel requires more power, slower cutting speeds, and higher consumable usage, which can drive up costs compared to cutting thinner metals like aluminum.
Other factors include setup and programming costs, especially for CNC plasma cutters, where custom cuts may require additional programming time. The use of gases like compressed air, nitrogen, or argon also adds to the total cost, particularly in higher-end machines.
Overall, plasma cutting for smaller-scale or hobby use typically costs around $2 to $5 per hour, while industrial applications, with more powerful machines, thicker materials, and skilled labor, can reach $20 to $30 per hour or more. The exact cost will depend on the specific requirements of the project and the machine being used.
VI.how much does a cnc plasma cutter cost?
The price of a CNC plasma cutter can vary significantly based on its features, specifications, and application. Factors such as machine size, power, cutting thickness, speed, CNC control system sophistication, and automation features all influence the cost. Here’s a detailed breakdown of the different price ranges and their characteristics:
1. Entry-Level or Hobby CNC Plasma Cutters (Price Range: $2,000 to $8,000)
These machines are designed for small-scale projects, personal use, or light-duty tasks. They are ideal for home workshops, hobbyists, or small businesses. Entry-level machines typically have smaller cutting tables and are suitable for cutting thinner metals like aluminum or stainless steel. They have lower power ratings and offer basic CNC controls, making them more affordable but with limited cutting capacity. Despite their modest features, they offer great value for users on a budget.
Ideal for:
- Personal DIY projects
- Small-scale metal art or sculpture
- Low-volume, light metal cutting tasks
2. Mid-Range CNC Plasma Cutters (Price Range: $10,000 to $30,000)
Mid-range machines are designed for small businesses or light industrial use. These cutters come with larger cutting tables, more powerful plasma systems, and can handle thicker materials. They often feature more advanced CNC controls and greater precision, with additional automation capabilities like height adjustment, plate detection, and automated path optimization. These machines are popular for businesses requiring higher productivity and efficiency.
Ideal for:
- Small businesses needing more power and precision
- Medium-scale metal fabrication and manufacturing
- Cutting thicker materials and higher precision tasks
3. Industrial-Grade CNC Plasma Cutters (Price Range: $40,000 to $100,000+)
Industrial-grade CNC plasma cutters are designed for heavy-duty, high-volume production environments. These machines can handle thick materials, often exceeding 50mm in thickness, such as carbon steel, stainless steel, and aluminum. They come equipped with highly advanced CNC systems and offer a wide range of automated features, such as material loading, cutting path optimization, remote monitoring, and high-speed cutting. These machines are built for long-term use in industries like shipbuilding, structural steel fabrication, and heavy machinery manufacturing.
Ideal for:
- Large metal fabrication shops
- Heavy industries like shipbuilding, construction, and machinery manufacturing
- Continuous cutting operations with high throughput demands
4. High-End Custom CNC Plasma Cutting Systems (Price Range: $100,000+)
For specialized needs, some businesses opt for custom-built CNC plasma cutting systems. These high-end machines are tailored to specific requirements, such as multi-torch setups, 3D cutting capabilities, or integration with fully automated production lines. These machines are commonly used in industries like aerospace, automotive manufacturing, and energy equipment production, where precision and complexity are paramount. High-end custom systems often include advanced software, remote diagnostics, automation of routine tasks, and integration into larger manufacturing processes.
Ideal for:
- Aerospace, automotive, and high-precision industries
- Complex, custom cutting operations
- Fully automated production lines with sophisticated needs
Additional Costs to Consider
Beyond the purchase price of the machine, there are several ongoing costs associated with operating CNC plasma cutters:
- Consumable Costs: Plasma cutters require consumables like electrodes, nozzles, and shields, which need regular replacement. Consumable wear depends on the material being cut and its thickness, contributing to operational costs.
- Electricity Costs: Plasma cutters, especially larger machines, consume significant amounts of electricity. The higher the machine’s power rating, the higher the electricity costs, particularly for long-term, continuous operation.
- Maintenance and Repairs: Regular maintenance is crucial for ensuring the machine operates efficiently and maintains precision. Industrial-grade machines, in particular, require more frequent and costly maintenance to avoid downtime.
- Training and Labor Costs: CNC plasma cutters require skilled operators, and investing in training for employees or hiring experienced personnel can add to the long-term cost. Proper training is necessary to ensure safe operation and optimal performance.
Summary
Choosing the right CNC plasma cutter depends on your specific needs, budget, and project scale. From entry-level models to high-end industrial systems, there is a wide range of machines available with varying levels of automation, cutting precision, and power. While the initial investment may be high for industrial users, the benefits of advanced automation and high productivity can lead to significant long-term returns. Additionally, ongoing operational costs such as consumables, electricity, and maintenance should be factored into the total cost of ownership.
Get Free Quote
Contact us for a free quote and more expertise on customizing laser equipment and accessories. Royell will provide the right solution for your project.
Get in Touch
- +853-62196448
- chenly@royelltec.com
Address
- Qikuo Optoelectronics Technology Co., Ltd.,Building 20, Lichen Road, Hongqiao Town, Changxing County, Huzhou City, Zhejiang Province